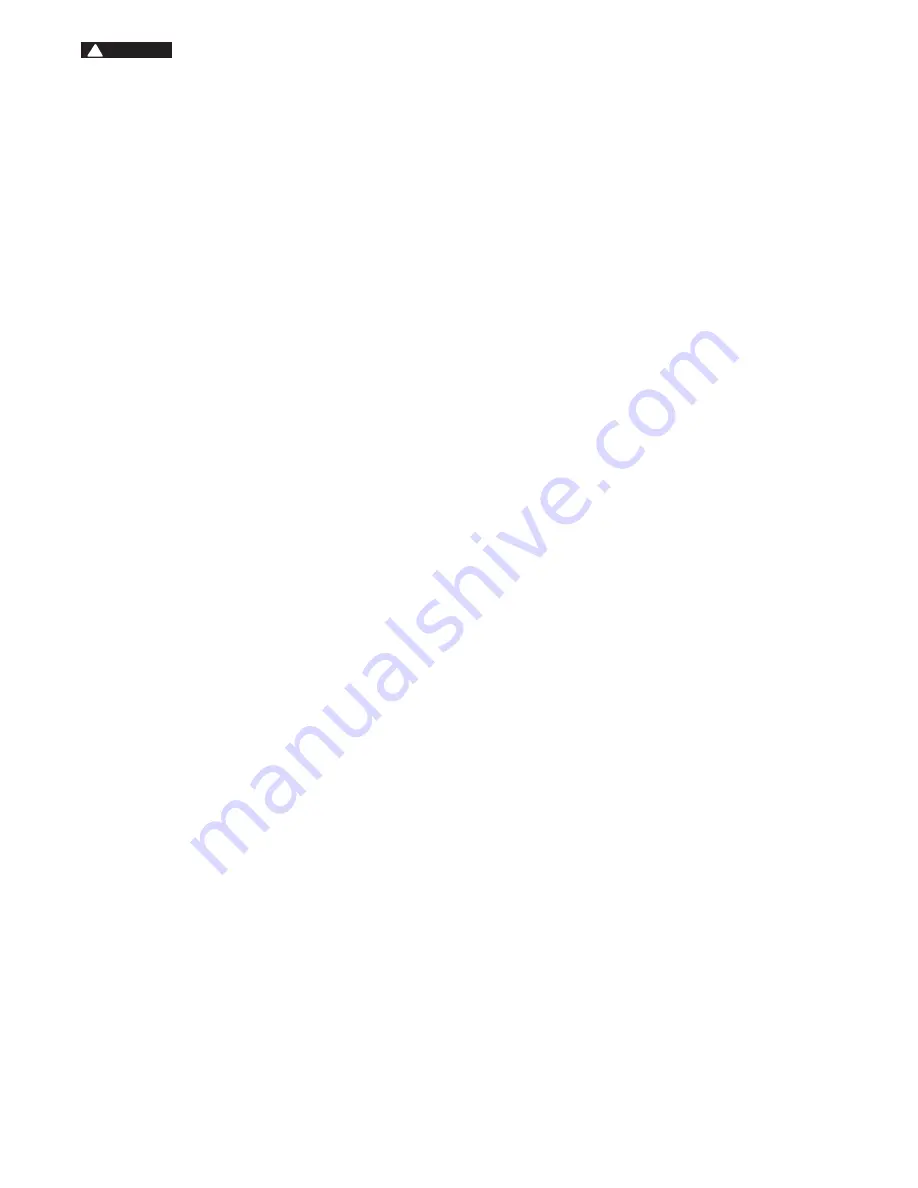
PWF Filter Systems
3
WARNING
!
This water conditioner’s control valve conforms to UL/
CE Standards. Generic valves were tested and certified for
compliance as verified by the agency listing. This water
conditioning system is to be used only for potable water.
Inspect the water conditioning system for carrier shortage or
shipping damage before beginning installation.
Operating Perameters:
• Operating ambient temperature: 40° to 110°F (5° to 43°C).
• Operating water temperature: 40° to 110°F (5° to 43°C).
• Operating water pressure range : 25 to 120 psi (1.7 to
8.27bar).
Installation Perameters:
All plumbing should be done in
accordance with local plumbing codes.
• Do not use pipe dope or other sealants on threads. Use Teflon
tape on the threaded inlet, outlet and drain fittings. Teflon tape
is not necessary on the nut connection or caps because of
o-ring seals.
• All plastic connections should be hand tightened. Teflon® tape
may be used on connections that do not use an O-ring seal.
Do not use pipe dope type sealants on the valve body.
Do not
use pliers or pipe wrenches.
• Observe drain line requirements.
• Keep the media tank in the upright position. Do not turn upside
down or drop. Turning the tank upside down or laying the tank
on its side can cause media to enter the valve.
• The pipe size for the drain line should be a minimum of ½”.
Backwash flow rates in excess of 7 gpm (26.5 lpm) or length in
excess of 20’ (6.1m) require ¾” drain line.
• Do not support the weight of the system on the control valve
fittings, plumbing, or the bypass.
Environmental:
• Use only regenerants designed for water conditioning. Do not
use ice melting salt, block salt or rock salt.
During cold weather it is recommended that the installer warm
the valve to room temperature before operating.
Teflon
®
is a trademark of E.I. duPont de Nemours.
• Do not use petroleum-based lubricants such as Vaseline, oils
or hydrocarbon-based lubricants. Use only 100% silicone
lubricants.
• Do not allow this water conditioning system to freeze. Damage
from freezing will void this water conditioning system’s
warranty.
• HYDROCARBONS SUCH AS KEROSENE, BENZENE,
GASOLINE, ETC., MAY DAMAGE PRODUCTS THAT
CONTAIN O-RINGS OR PLASTIC COMPONENTS.
EXPOSURE TO SUCH HYDROCARBONS MAY
CAUSE THE PRODUCTS TO LEAK. DO NOT USE THE
PRODUCT(S) CONTAINED IN THIS DOCUMENT ON
WATER SUPPLIES THAT CONTAIN HYDROCARBONS
SUCH AS KEROSENE, BENZENE, GASOLINE, ETC.
• THIS WATER METER SHOULD NOT BE USED AS THE
PRIMARY MONITORING DEVICE FOR CRITICAL OR
HEALTH EFFECT APPLICATIONS.
• Do not use Vaseline, oils, other hydrocarbon lubricants or spray
silicone anywhere. A silicone lubricant may be used on black
o-rings but is not necessary.
General Installation Guidelines
Electrical:
• Use only the power transformer supplied with this water
conditioning system.
• All electrical connections must be completed according to local
codes.
• The power outlet must be grounded.
• All electrical connections must be connected according to local
codes. (Be certain the outlet is uninterrupted.)
• Install grounding strap on metal pipes.
• The power adapter comes with a 15 foot power cord and is
designed for use with the control valve. The power adapter is for
dry location use only. The control valve remembers all settings
until the battery power is depleted if the power goes out.
• After the battery power is depleted, the only item that needs to
be reset is the time of day; other values are permanently stored
in the nonvolatile memory. The control valve battery is not
rechargeable but is replaceable.
• No user serviceable parts are on the PC board, the motor or
the power adapter. The means of disconnection from the main
power supply is by unplugging the power adapter from the
wall.
• Install an appropriate grounding strap across the inlet and
outlet piping of the water conditioning system to ensure that a
proper ground is maintained.
• To disconnect power, unplug the AC adapter from its power
source.
Soldering:
• Use only lead-free solder and flux, as required by federal and
state codes, when installing soldered copper plumbing.
• Use caution when installing soldered metal piping near the
water conditioning system. Heat can adversely affect the
plastic control valve and bypass valve.
• Solder joints near the drain must be done prior to connecting
the drain line flow control fitting. Leave at least 6” between the
drain line control fitting and solder joints when soldering pipes
that are connected on the drain line control fitting. Failure to do
this could cause interior damage to the drain line flow control
fitting.
• When assembling the installation fitting package (inlet and
outlet), connect the fitting to the plumbing system first and
then attach the nut, split ring and o-ring. Heat from soldering
or solvent cements may damage the nut, split ring or o-ring.
Solder joints should be cool and solvent cements should be
set before installing the nut, split ring and o-ring. Avoid getting
primer and solvent cement on any part of the o-rings, split
rings, bypass valve or control valve.
Control Valve:
• This glass filled Noryl
1
(or equivalent) fully automatic control
valve is designed as the primary control center to direct and
regulate all cycles of a water softener or filter.
• The control valve, fittings and/or bypass are designed to
accommodate minor plumbing misalignments but are not
designed to support the weight of a system or the plumbing.
• The nuts and caps are designed to be unscrewed or tightened
by hand or with the special plastic wrench. If necessary a
pliers can be used to unscrew the nut or cap. Do not use a
pipe wrench to tighten or loosen nuts or caps. Do not place a
screwdriver in the slots on caps and/or tap with a hammer.
• After completing any valve maintenance involving the drive
assembly or the drive cap assembly and pistons unplug power
source jack from the printed circuit board (black wire) and plug
back in or press and hold NEXT and REGEN buttons for 3