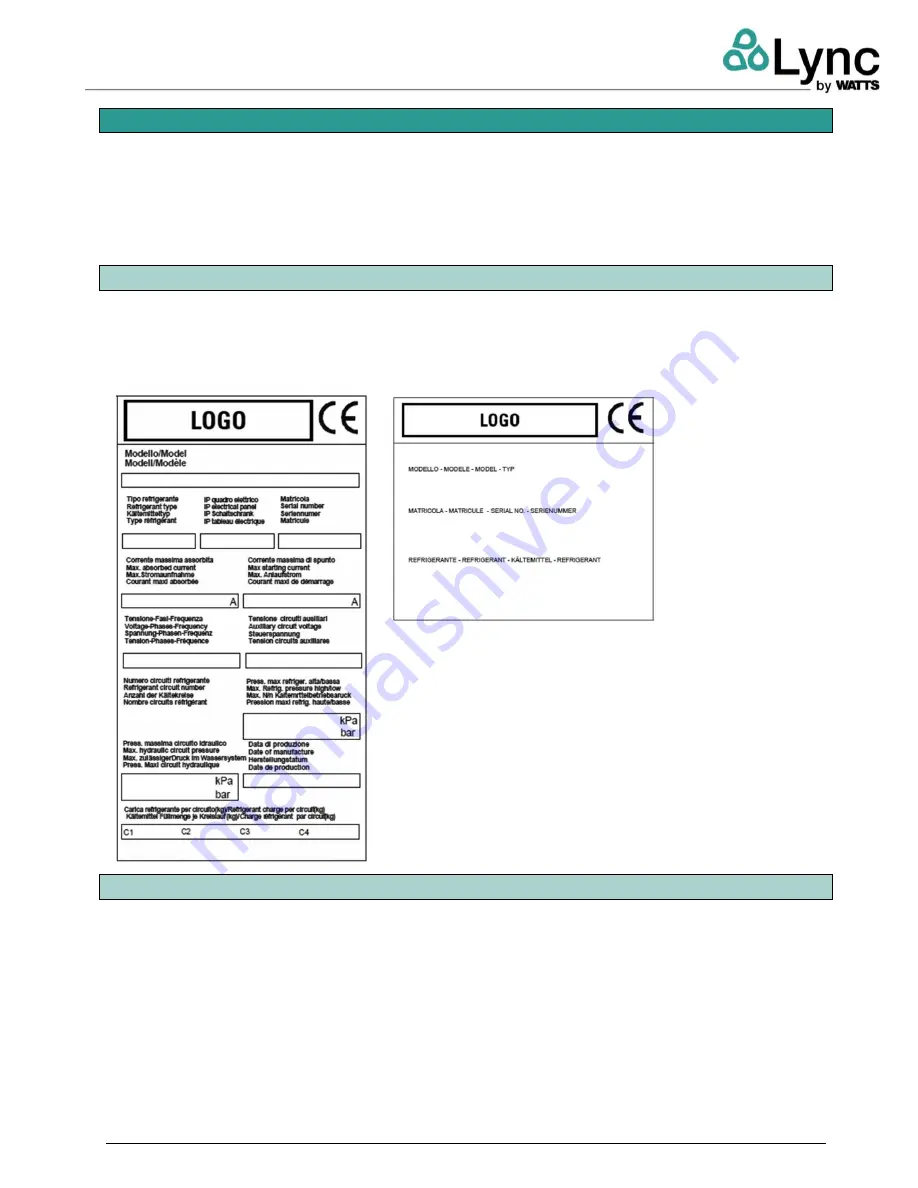
Lync AEGIS
2: INTRODUCTION
L-OMM-012_A
•
4/20/2022
Technical Support • (800) 433-5654 • Mon-Fri, 8 am - 5 pm EST
6
of
37
2.
INTRODUCTION
Aegis is a highly efficient, commercial heat pump solution that uses electricity and natural
refrigerant-grade CO2 to produce domestic hot water up to 185°F all year round.
Using electricity and the superior qualities of R744, a natural refrigerant-grade CO2, the Aegis
heat pump water heaters are one of the cleanest, most efficient and environmentally friendly ways
to heat domestic water.
2.1. Aegis Models
Aegis comes in two versions: Aegis A and Aegis W. Aegis A absorbs and moves heat from the
surrounding air at temperatures as low as -4°F to produce hot water. Aegis W produces hot water
by absorbing and moving heat from a connected water source at temperatures as low as 14°F.
The model, serial number, power voltage, etc. are shown on labels affixed to the machine.
2.2. Unit Control
The unit control software is responsible for regulating the outlet water temperature from
the appliance. The parameter displayed as " ST01 Set Hot Water" is user adjustable.
Additionally, the unit control manages the circulation of water in order to ensure that the
correct temperature rise in the system is maintained and will determine the need for hot
water recovery by monitoring the water temperature in the storage tanks.
Please note that the delivery temperature is regulated by modulating the pump, therefore the flow
of hot water at the outlet is not constant.