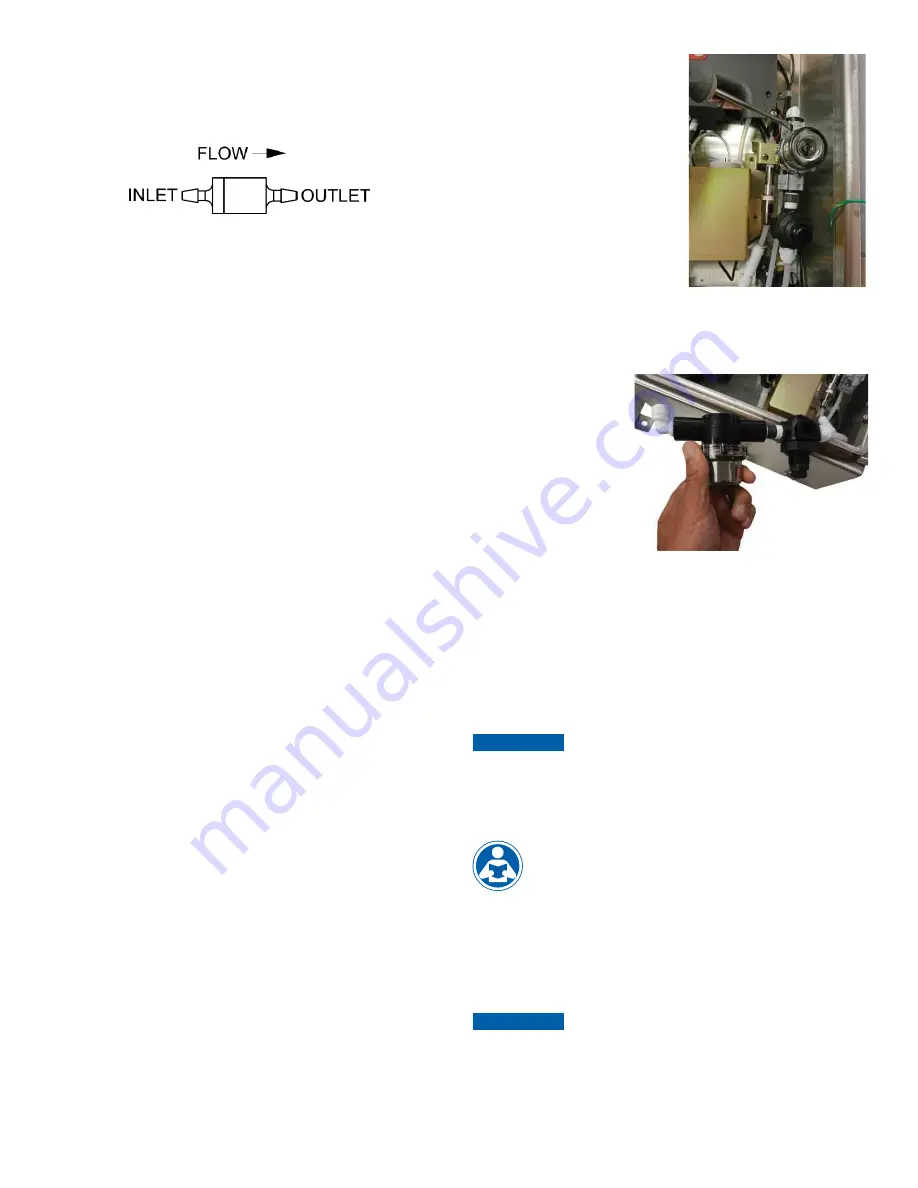
19
Pump Tubing Replacement
The black pump tubes may need replacement more often due to the
fact that they are subject to wear. The inline check valves should not
need to be replaced and should be saved. Please note that the check
valves are directional as shown below.
Figure 5: Inline check valve
Steps:
1. Flush the system as described above to reduce personal contact
with the reagents.
2. Press SERVICE to stop the flow of sample water and drain the
cuvette.
3. Remove and retain the thumb screw on top of the pump; pull the
pump hammer and spring up and out of the way. There is no need
to completely remove the hammer and spring.
4. Working on one reagent side at a time. Replace the black tubing
between optics inlet and the check valve OUTLET. Discard the old tubing.
5. Ensure the check valve is placed into its seat.
6. Repeat steps 4 and 5 for the other reagent.
7. Replace the hammer and spring back into place and secure with the
thumb screw.
8. Check the drawing on the following page to ensure correct installation.
9. Return to operation as described.
Cap Assembly Replacement
When the Cap Assemblies needs to be changed follow the procedure
shown below. It is recommended that both assemblies are changed at
the same time.
Steps:
1. Flush the system as described above to reduce personal contact
with the reagents.
2. Press SERVICE to stop the flow of sample water and drain the
cuvette.
3. Replace the buffer cap (blue or black cap) assembly.
4. Repeat step 3 above, for the indicator side (white cap).
5. Replace reagents, prime and return to service.
Cuvette Replacement
Check the condition of cuvette and change if it appears badly soiled or
discolored. Follow the steps below.
Steps:
1. Replace the two Cap Assemblies.
2. Turn the knurled top on the optics system counterclockwise (as
viewed for the top) until the cuvette just “pops” out, but do not
remove the top.
3. When the cuvette “pops” out, move the retaining O-ring and remove
the cuvette. You may need a stiff wire such as a bent paper clip
to grasp the cuvette. Retain this cuvette for future use if it can be
cleaned.
4. Install the new cuvette by pushing it firmly in place and turning the
knurled top clockwise until the cuvette is held securely.
5. Check the drawing on the following page to ensure correct installation.
6. Return to operation as described.
T-Strainer Cleaning
The T-strainer is integral to the
instrument and must be checked
occasionally. When necessary it
must be removed and cleaned.
The strainer screen may require
replacement after a period of time.
Steps:
1. Press SERVICE to stop the flow
of sample water and drain the
cuvette.
2. Ensure the source water is
turned off.
3. The T-strainer is clamped to the
intake regulator. The removal
requires the use of a flat blade screwdriver as shown in the photo.
Once the two clamps are opened the T-strainer can be removed.
4. Disconnect the top of the T-strainer and regulator from the tubing
and clear of the enclosure.
5. Remove and clean
the screen and then
reassemble.
6. Be sure to tighten the
bowl of the strainer.
7. Be certain the clamps
are tightened fully and
the tubing connections
are complete. You may
require pliers to close
the clamps.
8. Turn source water back on.
9. Return to normal operation.
10. Check for any leaks.
Return to Normal Operation
Press the SERVICE button to return sample flow to the system.
Check for leaks. If a leak occurs press SERVICE again, repair leak and
try again. Once the system is operating correctly, return or replace
reagents and press PRIME and then
one time to restart reagent flow.
The system will automatically return to normal operation.
NOTICE
Tubes may darken due to contact with the reagent. This condition
does not affect the performance of these parts.
11.2 Replacing or Installing the Reagents
Reagent kits are available from HF scientific for Total
Chlorine Refer to section 12.0
Replacement Parts and
Accessories
for the appropriate Catalog number. There are
two reagents required, for the instrument to operate; the
buffer and the indicator.
The reagents are provided “wet” and the buffer is ready to use and will
last up to one year.
The smaller indicator reagent does require the addition of the DPD
power to activate it. Once activated it starts to oxidize. This process is
slowed by keeping it in the cooling chamber.
NOTICE
When commissioning the CLX-Ex2 it is recommended to follow
the procedure in section 11.4. This procedure only needs to be
done once when the instrument first commissioned.