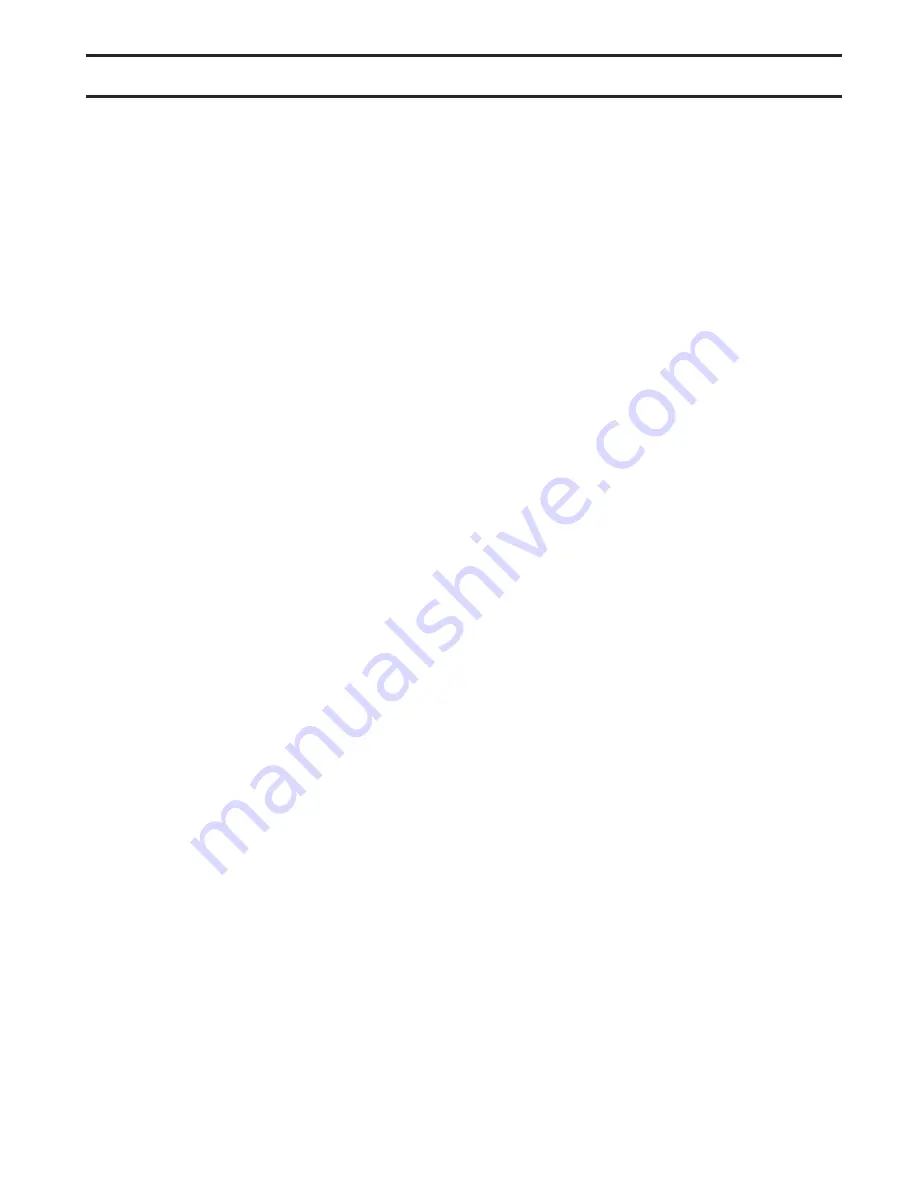
CONTENTS
The plug and/or injector can be pried out with a small
screwdriver. The plug can be wiped clean. If the plug leaks
replace the entire plug. The injector consists of a throat and a
nozzle. Chemically clean the injector with vinegar or sodium
bisulfite. The holes can be blown out with air. Both pieces have
small diameter holes that control the flow rates of water to insure
that the proper concentration of regenerant is used. Sharp
objects, which can score the plastic, should not be used to clean
the injector. Scoring the injector or increasing the diameter of the
hole could change the operating parameters of the injector.
Two holes are labeled DN and UP. Check for compliance with
one of the following:
a.
For downflow systems, the appropriate size injector is
located in the “DN” hole, a plug is in the “UP” hole and
the piston is a combination of the downflow main piston and
the regenerant piston;
b.
For upflow systems, the appropriate size injector is located
in the “UP” hole, a plug is in the “DN” hole and the piston
is a combination of the upflow main piston and the regenerant
piston; or
c.
For backwash only systems, a plug is in the “DN” hole and
in the “UP” hole, and the piston only has a downflow
main piston (the regenerant piston must be removed) and a
plug is in the refill flow control position.
Push the plug(s) and/or injectors firmly in place, replace the
screen and hand tighten the injector cap.
REFILL FLOW CONTROL ASSEMBLY
OR REFILL PORT PLUG
To clean or replace the refill flow control, pull out the elbow-
locking clip and then pull straight up on the elbow. Replace the
elbow-locking clip in the slot so that it is not misplaced. Twist to
remove the white flow control retainer. The flow control can be
removed by prying upward through the side slots of the retainer
with a small blade flat screwdriver.
Chemically clean the flow control or the white flow control
retainer using dilute sodium bisulfite or vinegar. Do not use a
wire brush. If necessary, replace the flow control o-ring on
the flow control retainer, or the o-ring on the elbow.
Reseat the flow control so the rounded end is visible in the flow
control. Reseat the white flow control retainer by pushing the
retainer into the elbow until the o-ring seats. Remove locking clip,
push down on elbow to reseat and insert locking clip.
Do not use Vaseline, oils
,
o
r other unacceptable lubricants on
o-rings. A silicon lubricant may be used on the o-ring on elbow or
the white retainer.
WATER METER OR METER PLUG
The water meter assembly is connected to t
he
PC board by a
wire. If the entire water meter assembly is to be replaced, remove
the control valve cover and remove the power source and water
meter plugs from the PC board. Unlatch the drive assembly and
lean it forward. Unthread the water meter wire from the side of the
drive assembly and through the drive back plate. To reinstall,
rethread the water meter wire through the drive back plate and
the side of the drive assembly. Reattach the drive assembly
and the water meter and power plugs.
If no water meter wire is visible, then a plug is installed not a
water meter.
The water meter wire does not need to be removed from the PC
board if the water meter is only being inspected and cleaned.
To remove the water meter assembly, unscrew the meter cap on
the left side of the control valve. Pliers may be used to unscrew
the nut if necessary.
With the nut removed, a slot at the top of the water meter is
visible. Twist a flat blade screwdriver in the slot between the
control valve body and the meter. When the meter is part way
out it is easy to remove the water meter from the housing.
Once the water meter is removed from the control valve body,
use your fingers to gently pull forward on the turbine to remove
it from the shaft.
Do not use a wire brush to clean. Wipe with a clean cloth or
chemically clean in dilute sodium bisulfite or vinegar. The turbine
can be immersed in the chemical. Do not immerse electronics. If
the turbine is scored or damaged or the bearings on the turbine
are worn replace the turbine.
Do not lubricate the turbine shaft. The turbine shaft bearings are
pre-lubricated. Do not use Vaseline, oils or other unacceptable
lubricants on the o-ring. A silicon lubricant may be used on the
black o-ring.
Snap the turbine on the shaft and reinsert the water meter into
the side slot. Hand tighten the nut. Do not use a pipe wrench to
tighten nut.
BYPASS VALVE
The working parts of the bypass valve are the rotor assemblies
that are contained under the bypass valve caps. Before working
on the rotors, make sure the system is depressurized. Turn the
red arrow shaped handles towards the center of the bypass valve
and back to the arrow direction several times to ensure rotor is
turning freely.
The nuts and caps are designed to be unscrewed or tightened
by hand. If necessary a pair of pliers can be used to unscrew the
nut or cap. Do not use a pipe wrench to tighten or loosen nuts or
caps. Do not place screwdriver in slots on caps and/or tap with a
hammer. To access the rotor, unscrew the cap and lift the cap,
rotor and handle out as one unit. Twisting the unit as you pull it
out will help to remove it more easily. There are three o-rings: one
under the rotor cap, one on the rotor stem and the rotor seal.
Replace worn o-rings. Clean rotor. Reinstall rotor.
When reinstalling the red arrow handles be sure that:
1.
O-rings on both rotors face to the right when being viewed
from the front of the control valve when the handle pointers
are lined up with the control valve body arrows; or
2.
Arrows point toward each other in the bypass position.
Since the handles can be pulled off, they could be accidentally
reinstalled 180° from their correct orientation. To install the red
arrow handles correctly, keep the handles pointed in the same
direction as the arrows engraved on the control valve body while
tightening the bypass valve caps.
After completing, any valve maintenance, press and hold NEXT
and REGEN buttons for 3 seconds or unplug power source jack
(black wire) and plug back in. This resets the electronics and
establishes the service piston position. The display should flash
all wording then flash the software version (e.g. 154) and then
reset the valve to the service position.
17