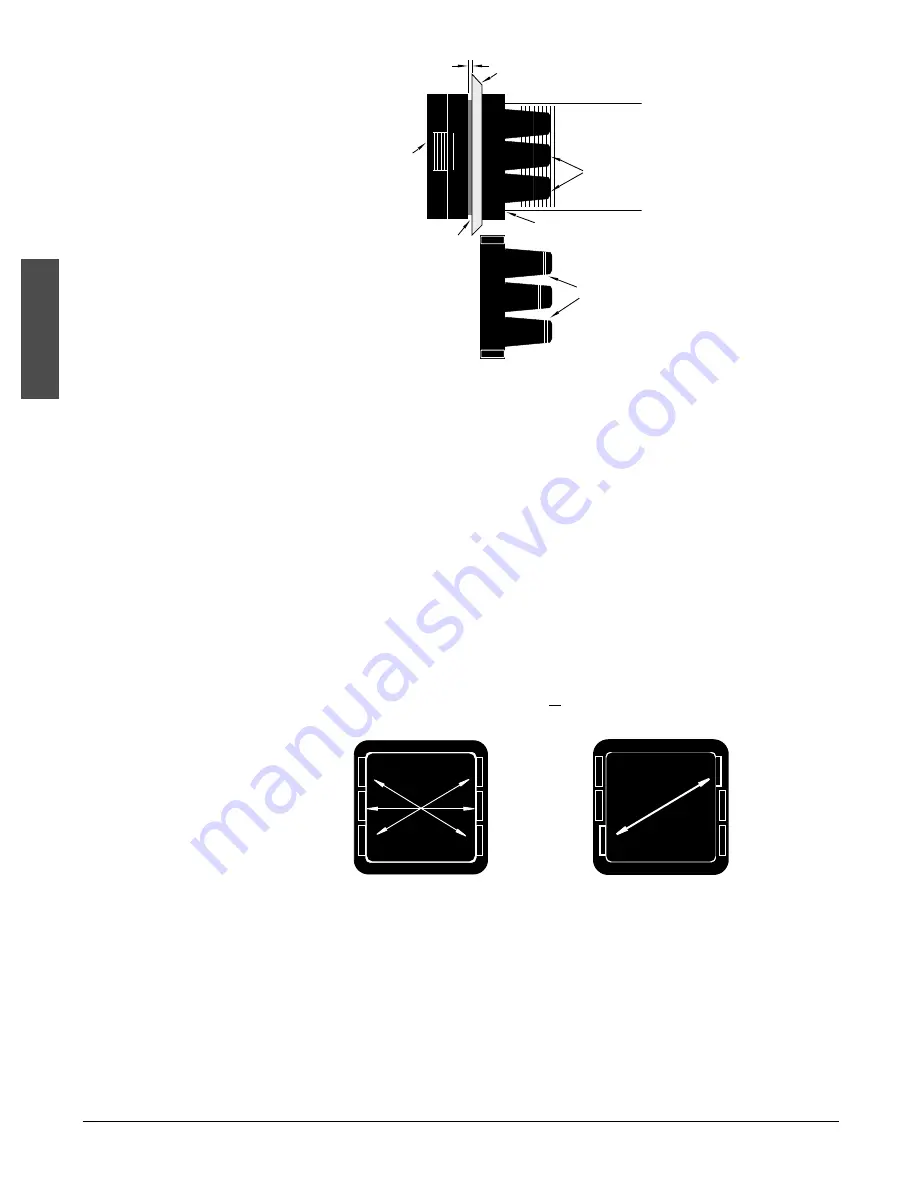
3.
While pressing the front of the case firmly against the panel, slide the
mounting collar over the back of the control. The tabs on the collar must line
up with the mounting ridges on the case for secure installation. See Figure 2
a. Slide the collar firmly against the back of the panel getting it as tight as
possible.
To ensure a tight seal, use your thumb to lock the tabs into place while press-
ing the case from side to side. Don’t be afraid to apply enough pressure to
install the control. The tabs on each side of the collar have teeth which latch
into the ridges. See Figure 2b. Each tooth is staggered at a different height,
so only one of the tabs on each side are ever locked into the ridges at any
time.
As depicted in Figure 2.2c, confirm that the tabs on one side of the collar cor-
respond with those on the opposite side. Make sure the two corresponding
tabs are the only ones locked in the ridges at the same time.
If the corresponding tabs are not supporting the case at the same
time and the space between the panel and the case bezel is greater
than .019", you will will not have a NEMA 4X seal. This applies to
units with models designated 94B.
However, all units should be mounted
in this fashion to guarantee integrity of the mounting system.
2 . 2
■
I n s t a l l a n d W i r e
W a t l o w S e r i e s 9 4
Install and Wire
Figure 2.2a -
Mounting Case Side
View.
Figure 2.2b -
Mounting Collar
Cross Section with
offset teeth.
Figure 2.2c -
Case Rear View and
NEMA 4X Seal
Example.
0 to 0.019 space
(0 to 0.483 mm)
Bezel
Panel
External Gasket
Mounting Collar
Ridges
Teeth
Tabs
4.
Insert the control chassis into its case and press the bezel to seat it. Make
sure the inside gasket is also seated properly and not twisted. The hardware
installation is complete. Proceed to the wiring section from here.
Removing the Series 94 Controller
When removing the mounting collar, we suggest using a thin tool such as a
putty knife or screwdriver to pry gently under each of the six tabs to disen-
gage the teeth. Then rock the collar back and forth until it can be easily
pulled off the case.
NEMA 4X Seal Example.
Make sure that the two corresponding tabs
are locked in the ridges at the same time
.
ç
CAUTION: Follow the
installation procedure
exactly to guarantee a
proper NEMA 4X seal.
Make sure the gasket
between the panel
and the rim of the
case is not twisted
and is seated proper-
ly. Failure to do so
could result in dam-
age to equipment.