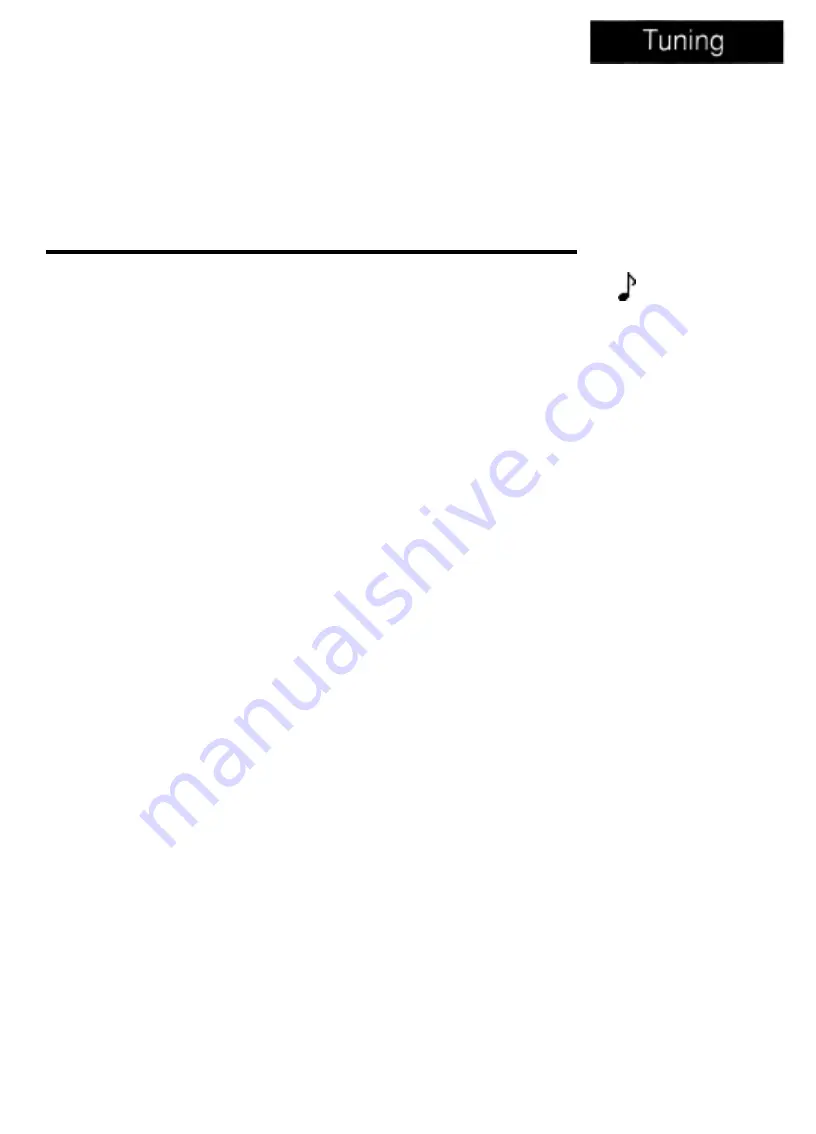
Chapter 5
How to Tune and Operate
Tuning - Automatic
Auto-tuning: The Series 9801985
gives you the capability to automatically tune
the PlD parameters to fit the characteristics of your particular thermal system.
The
auto-tuning procedure operates on a thermal response value - slow,
medium, or fast. A slow thermal response is used when the process tempera-
ture is not met too rapidly, or greatly exceeds the set point value. A fast thermal
response produces a rapid temperature change over a short period of time.
NOTE:
Auto-tuning is only
possible in
the heat
mode. The cool
output remains off.
Once the auto-tune sequence has begun, all PID values for both heat and cool
are set to 0 and the control goes into an ON/OFF mode of control at 90% of the
established set point. The displayed set point remains unchanged.
The cool output remains off for the duration of the tuning. Once the control has
finished “learning” the system, it returns to standard PID control with the heat
PID values being automatically established as a result of the auto-tuning. The
operator must then establish the cool PID values manually. Tuning is complete
within 40 minutes. Any change of the set point, while in auto-tune, re-initiates
the auto-tune procedure.
To start auto-tuning:
1.
2.
3.
4.
Press the MODE key
until the
AUt
prompt appears in the data display.
Select a thermal response value,
1=slow, 2=medium, and 3=fast, using
the UP/DOWN keys. A thermal response value of 2 will satisfactorily tune
most thermal systems.
Press the MODE key.
While the control is in the tuning mode, the lower
display alternately displays the normal information and the prompt
At.
The
time between alternations is 1 second.
When the process is complete,
the displays return to their previous state
and
AUt
reverts to 0. The appropriate PID tuning parameters are now
installed, and retained in the non-volatile memory.
To abort auto-tuning,
the operator must reset the
AUt
parameter to 0. This
leaves the unit in an ON/OFF heat control state in Auto operation at the dis-
played set point. The auto-tuning process may also be aborted by pressing the
AUTO/MANUAL key twice. In both cases, all PID values are set to 0.
Tuning and Operating, Chapter 5
WATLOW Series 980/985 User's Manual
29