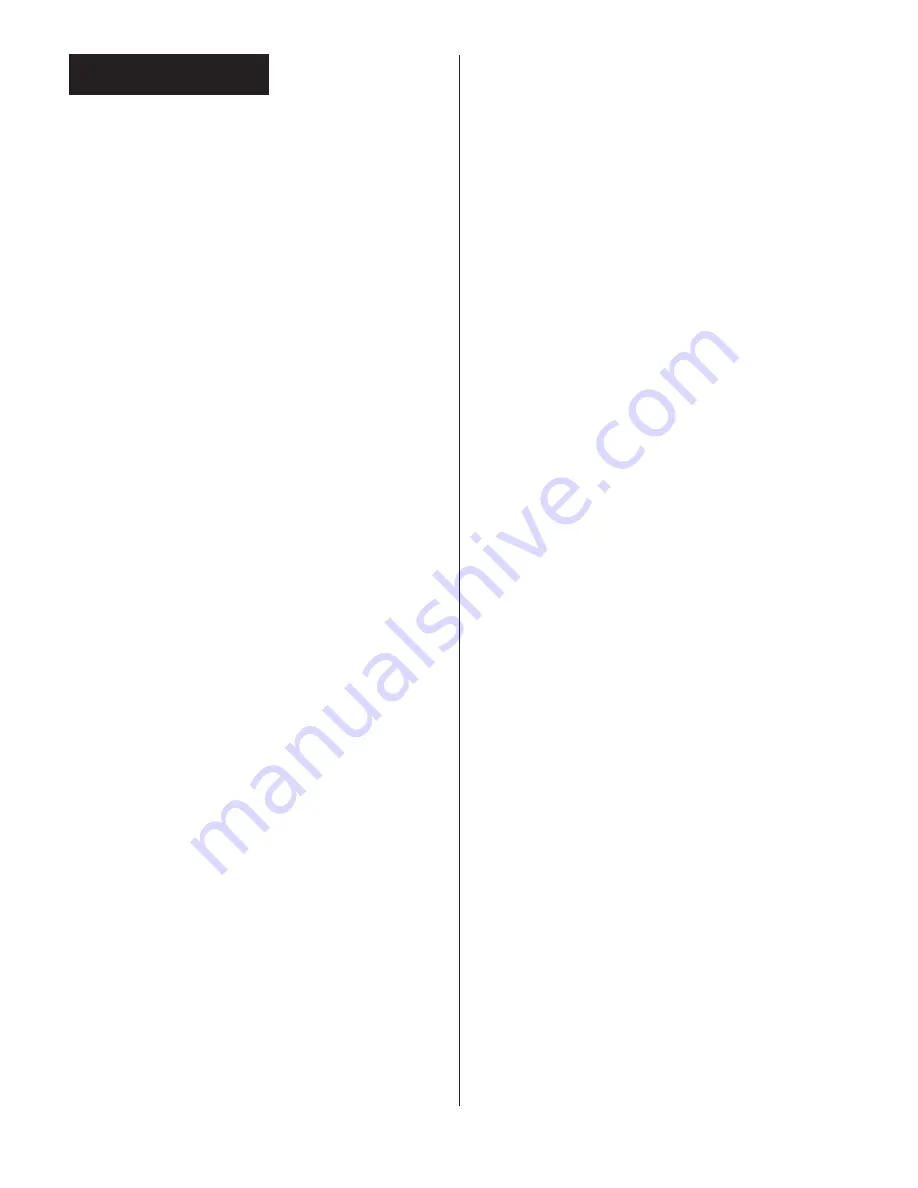
38
WATLOW Series 965 User's Manual
Appendix
Specifications—(1460)
Control Mode
• Microprocessor-based, user selectable control modes
• Single input, dual output
• 2.5Hz Input Sampling Rate
• 1Hz Display Update Rate
• Ramp to set point: 0 to 9999 degrees or units per hour
• Heat and cool auto-tune
Agency Approvals
• UL and C-UL recognized, File #E43684, UL873
• CE approved
89/336/EEC Electromagnetic Compatibility Directive
EN 50081-2: 1994 Emissions
EN 50082-2: 1995 Immunity
73/23/EEC Low -Voltage Directive
EN 61010-1: 1993 Safety
• NEMA 4X
2
, I.P. 65 rating
Operator Interface
• Sealed membrane front panel
• Dual, four-digit red or green displays
• MODE, Up-arrow, Down-arrow, and AUTO/ MANUAL keys
• User selectable screen display
Accuracy
• Calibration accuracy and sensor conformity:
±
0.1% of span,
±
1 LSD @ 77
°
F
±
5
°
F (25
°
C
±
3
°
C) ambient and rated line
voltage
• Accuracy span: 1000
°
F (540
°
C) minimum
• Temperature stability:
±
0.2
°
F/
°
F (
±
0.2
°
C/
°
C) rise in ambient
maximum
• Voltage stability:
±
0.01% of span per percent of rated line
voltage
Sensors/Inputs
• Thermocouple, grounded or ungrounded sensors
• RTD 2- or 3-wire, platinum, 100
Ω
@ 0
°
C calibration to DIN
curve (0.00385
Ω
/
Ω
/
°
C) or JIS curve (0.003916
Ω
/
Ω
/
°
C); user
selectable
• Process, 4-20mA @ 5
Ω
, or 0-5V
Î
(dc) @ 10k
Ω
input
impedance
• Sensor break protection de-energizes control output to
protect system or selectable bumpless transfer to manual
operation
•
°
F or
°
C or process units display, user selectable
Input Range
Specified temperature ranges represent the controller’s
operational span.
• Thermocouple
Type J
32
to
1382
°
F
(0
to
750
°
C)
Type K
-328
to
2282
°
F
(-200
to
1250
°
C)
Type N
32
to
2282
°
F
(0
to
1250
°
C)
Type S
32
to
2642
°
F
(0
to
1450
°
C)
Type T
-328
to
662
°
F
(-200
to
350
°
C)
• RTD Resolution (DIN or JIS)
1
°
-328
to
1292
°
F
(-200
to
700
°
C)
0.1
°
-199.9
to
999.9
°
F
(-128.8
to
537.7
°
C)
• Process
4-20mA @ 5
Ω
, or -999 to 9999 units
0-5V
Î
(dc) @ 10k
Ω
, or -999 to 9999 units
Output 1 (Heating or Cooling)
• Electromechanical relay
1
, Form C, 5A @ 120/240V~ (ac)
maximum, without contact suppression, rated resistive load,
5A @ 30V
Î
(dc)
3
.
• Switched dc signal provides a non-isolated minimum turn on
voltage of 3V
Î
(dc) into a minimum 500
Ω
load; maximum on
voltage not greater than 12V
Î
(dc) into an infinite load.
• 4-20mA reverse or direct acting, non-isolated 0 to 800
Ω
load.
• Solid-state relay
3
, Form A, 0.5A @ 24V~ (ac) min., 264V~
(ac) max., opto-isolated burst fire switched, without contact
suppression. Off-state output impedance is 31M
Ω
.
Output 2 (Heat, Cool or Alarm)
• Electromechanical relay
1
, Form C, 5A @ 120/240V~ (ac)
maximum, without contact suppression, rated resistive load,
5A @ 30V
Î
(dc)
3
.
• Switched dc signal provides a non-isolated minimum turn on
voltage of 3V
Î
(dc) into a minimum 500
Ω
load; maximum
on voltage not greater than 12V
Î
(dc) into an infinite load.
• Solid-state relay
3
, Form A, 0.5A @ 24V~ (ac) min., 264V~
(ac) max., opto-isolated burst fire switched, without contact
suppression. Off-state output impedance is 31M
Ω
.
• Alarm output can be latching or non-latching, and process or
deviation with separate high and low values. Alarm silencing
(inhibit) on power up.
Output Configurations
• Output 1
User selectable as: on/off: P, PI, PD, PID, heat or cool action
• Adjustable switching differential: 1 to 99
°
F (1 to 55
°
C)
• Proportional band: 0 (off) or 1 to 999
°
F (0 to 555
°
C) or 0.0 to
999.9 units
Integral: 0 (off) or 0.1 to 99.9 minutes per repeat
Reset: 0 (off) or 0.01 to 9.99 repeats per minute
Rate/derivative: 0 (off) or 0.01 to 9.99 minutes
Cycle time: 0.1 to 999.9 seconds
• Output 2
User selectable as: Control with action opposite that of Output
1 (heating or cooling)
• Process or deviation alarm with flashing alarm message
• Process or deviation alarm without alarm message
• Alarm with separate high and low set points
• Hysteresis: 1 to 9999
°
or units switching differential
Line Voltage/Power
• 100-240V~ (ac), +10%, -15%; (85-264V~ [ac]) 50/60Hz,
±
5%
•12-24V
ı
(ac/dc), +10%, -15%; (10-26V
ı
[ac/dc]) 50/60Hz,
±
5%
• Fused internally (factory replaceable only) Slo-Blo® type
(time-lag):
1A, 250V for high voltage versions
2A, 250V for low voltage versions
• Power consumption 5VA maximum
• Data retention upon power failure via non-volatile memory
Operating Environment
• 32 to 149
°
F (0 to 65
°
C)
• 0 to 90% RH, non-condensing
Storage Temperature
• -40
°
to 185
°
F (-40
°
to 85
°
C)
Terminals
• #6 compression universal head screw terminals, accepts 20-
14 gauge wire
Controller Weight
• 0.4 lb
(0.2 kg)
Shipping Weight
• 0.75 lb (0.34 kg)
Dimensions
• Compact 1⁄16 DIN size and NEMA 4X
2
, (I.P. 65) front panel
make the Series 965 easy to apply and maintain in a wide
variety of applications. Unique mounting bezel, gasket and
collar make installation a snap.
Overall
Height:
2.1 inches
(55 mm)
Width:
2.1 inches
(55 mm)
Depth:
4.7 inches
(120 mm)
Bezel
Height:
2.1 inches
(55 mm)
Width:
2.1 inches
(55 mm)
Depth:
0.6 inches
(15 mm)
Chassis Height:
1.8 inches
(45 mm)
Width:
1.8 inches
(45 mm)
Depth:
4.1 inches
(105 mm)
1
Electromechanical relays warranted for 100,000 closures
only. Solid-state switching devices recommended for
applications requiring fast cycle times or extended service
life.
2
To effect NEMA 4X (I.P. 65) rating requires a minimum
mounting panel thickness of 0.06inch (1.5 mm) and surface
finish not rougher than 0.000032 inch (0.000812 mm).
3
Switching inductive loads (relay coils, etc.) requires using an
RC suppressor.
Specifications