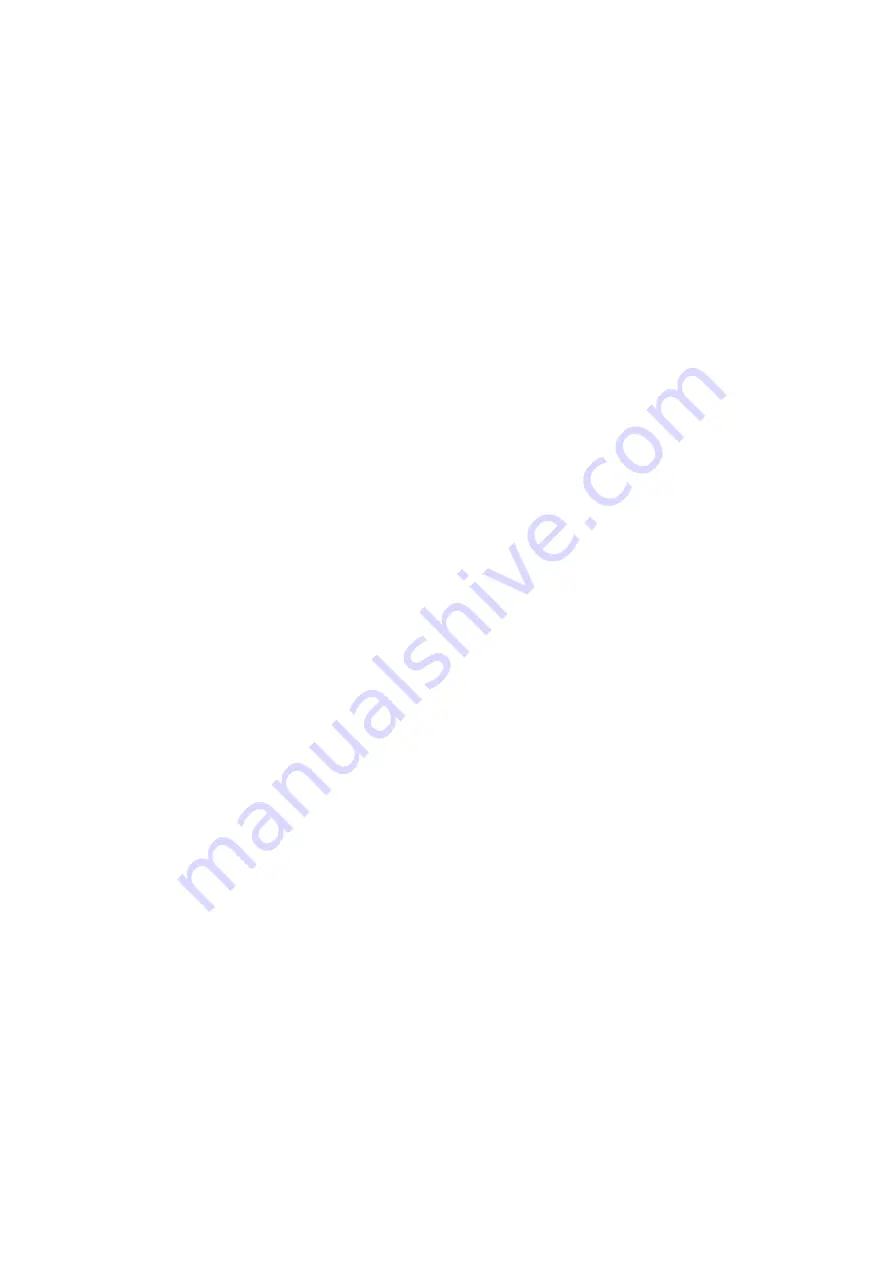
5
4. User Safety
Element cover
Do not remove the element cover as this will expose 230 V wiring and must only be removed by a suitably qualified
tradesperson.
Thermostat Setting
Must only be adjusted by an electrician or other suitably qualified tradesperson.
Damaged Components
If any component is damaged, it must be replaced by a suitably qualified tradesperson using Protank replacement
parts only.
Hot Pipe Work
Care should be taken not to touch the pipe work around the cylinder as it could cause scalding.
Turning the Cylinder Off and On
If you plan to be away for an extended period it makes sense to switch the power supply off. When switching back
on, remember that the cylinder will take a few hours to re-heat.
Draining and Filling the Cylinder
This should only be performed by a qualified tradesperson.
5. Pipe Work
It is the installer’s responsibility to adequately size the distribution pipe work to ensure sufficient performance
from all outlet fittings. Water pipe sizing should be performed in accordance with AS/NZS 3500.4 and/or G12 AS1.
Contact Waterware for advice on system sizing and design.
6. Maintenance and Servicing
Hot water systems require regular maintenance and servicing to ensure longevity and trouble free operation. We
recommend the following procedures be followed;
Every 6 Months:
Operate and vent water from the temperature & pressure relief* valve.
Every 5 Years Thereafter:
Inspect all connections and the heating element** if installed in hard water areas.
*TPR Valve
This valve is the highest mounted valve on the side of the cylinder and is an essential safety valve. It works by
automatically venting hot water if the temperature or pressure of the water in the cylinder exceeds its presetting.
Rotate the red knob approximately ¼ of a turn and hold in that position for 5 seconds while hot water is vented
into the drain. This helps clear any naturally occurring lime deposits that may cause it to malfunction. If it fails to
vent any water or continues to vent water when released, immediately switch off the power and call a qualified
tradesperson to arrange an inspection.
**Heating Element
In hard water areas the element(s) may need to be periodically descaled by a suitably qualified tradesperson. To do
this the unit must be drained and the element(s) removed.
7. Troubleshooting
Do not attempt to carry out any work other than that mentioned in this troubleshooting section. If you have any
other faults or problems, please contact qualified tradesperson or Waterware.
No hot water
• Is there an electricity supply to the cylinder?
• Check that the isolating switch marked ‘hot water’ or ‘water heater’, at the meter box, is switched on. Also
check any isolating switches near the water heater are switched on.
• Check the fuse or circuit breaker marked ‘hot water’ or ‘water heater’ at the meter box. Repeated failure