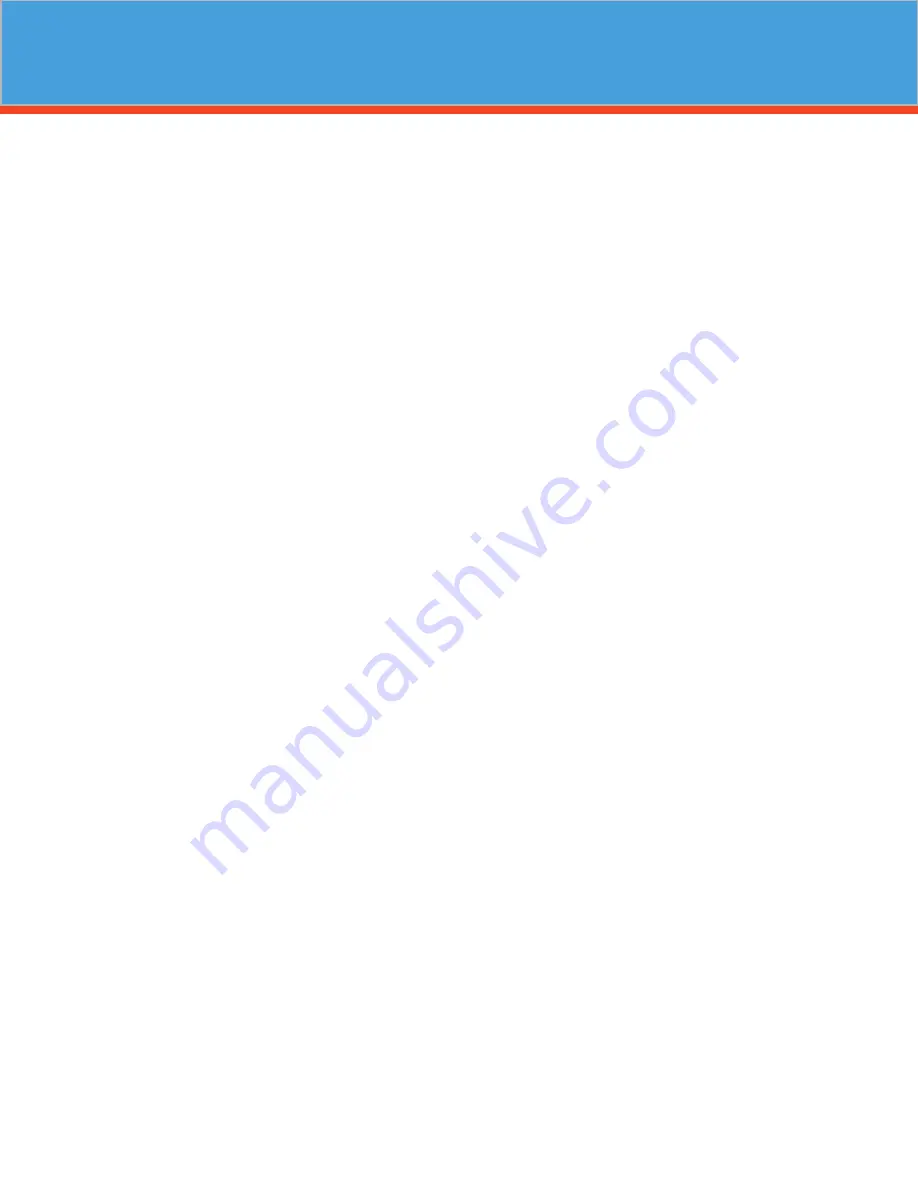
25
Error Codes
Control Valve Error Code Diagnosis
Under normal operating conditions, when your control valve is in the “in service” position, the display
should alternate between the current time of day and the number of days remaining (for filters and time
clock softeners) or gallons remaining (for metered softeners) until the next regeneration. This is the “home
display.” If the valve is currently going through a regeneration cycle, the display will show the cycle step
on the left side of the display and the number of minutes remaining in that step on the right side of the
display. If any other information is being displayed, then the valve is
informing you of an issue. There are five error codes which could indicate an issue with the control valve.
When an error is being displayed, the valve will be in a stopped position, and the buttons will not respond
to being pressed. Even if the cause of the error code is corrected, the error code will not clear until the
power supply has been disconnected and reconnected (this will be referred to as “cycling” the power). All
error codes are displayed as the letters “Err” followed by a flashing number 2-6:
Error 2
- Valve is searching for homing slot.
Allow valve to continue running. If the homing slot is found, the valve will return to the home display, oth
-
erwise, another error code will appear.
Error 3
- No encoder slots are being seen.
This occurs when the motor is running, but the encoder is not seeing any of the slots in the encoder wheel.
This can happen if the encoder has been disconnected, but most commonly occurs when debris in the
valve body has stopped the piston, causing the encoder wheel to be unable to turn.
1. Check encoder connection. If the encoder is plugged in and snapped into place, skip to step #2
below. If encoder is disconnected, reconnect it and cycle power to clear the error.
2. Disconnect powerhead from valve body, cycle power to clear the error code. Manually cycle the
powerhead through the regeneration cycle steps to verify that the motor can cycle properly while
the powerhead is disconnected from the valve body. If the error 3 does not reappear, skip to step
#3 below. If the error 3 does reappear, order a board & motor kit to replace the circuit board &
motor.
3. Remove piston and seals from the valve body and inspect valve body for debris. Replace the seal
& spacer kit. Inspect piston and replace piston if Teflon coating is worn
Error 4
- Unable to find homing slot.
1. Check encoder wheel for debris.
2. Cycle power. Valve should either find home or go to a different error code. If error 4 returns,
replace powerhead assembly.
Error 5
- Motor overload.
This occurs when the motor current is too high. This could be caused by an issue with the motor itself, but
is typically caused by friction in the valve body
1. Disconnect powerhead from valve body and cycle power to clear the error code.
2. If the error 5 returns, replace the motor. Otherwise, manually cycle the powerhead through the
regeneration cycle steps to verify that the motor can cycle properly while the powerhead is
disconnected from the valve body. Either way, proceed to the next step.
3. Remove piston and seals from the valve body and inspect valve body for debris. Replace the seal
& spacer kit. Inspect piston and replace piston if Teflon coating is worn.
Error 6
- No motor current.
This typically occurs if the motor cable has come unplugged from the circuit board. Check that the motor
cable is plugged into the circuit board and attached to the motor. If this is not the issue, the motor or cir
-
cuit board may need to be replaced.