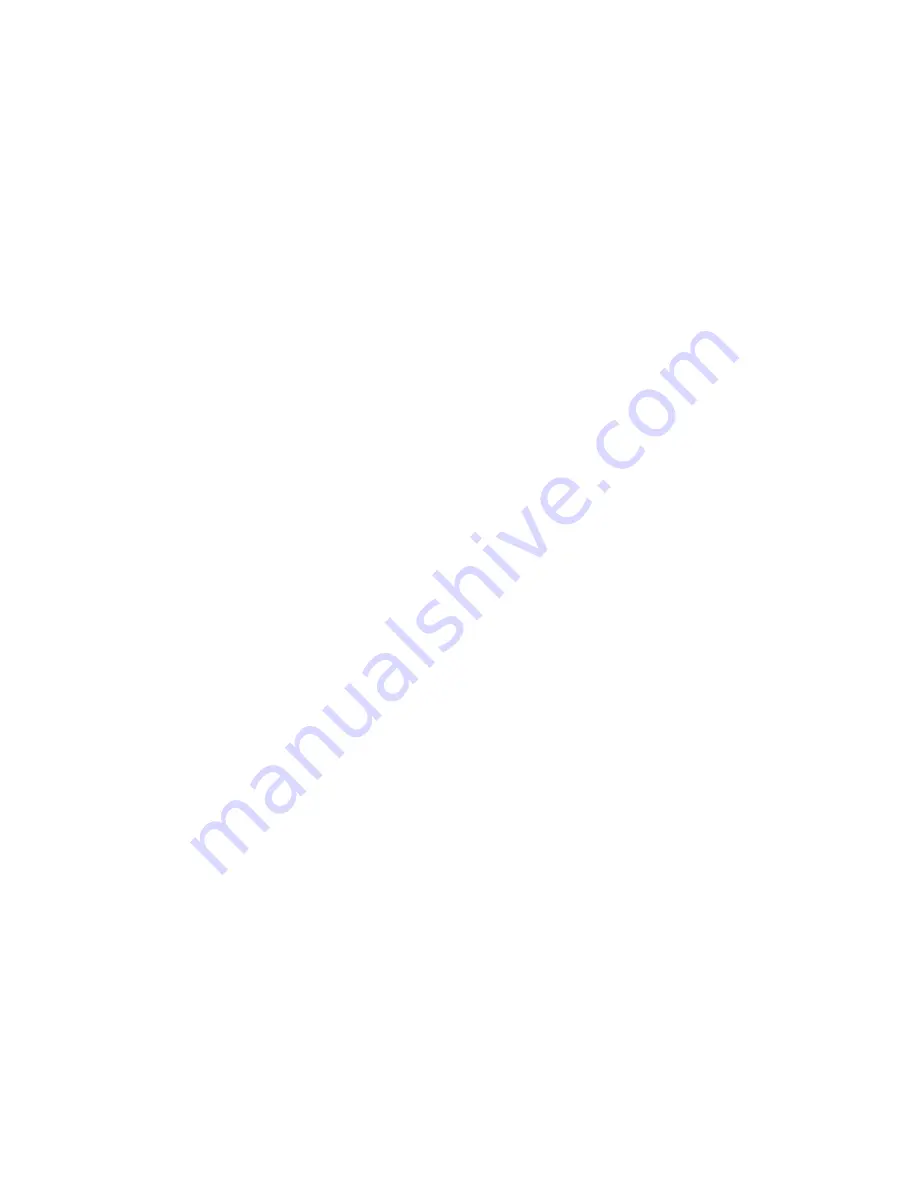
Page 3 of 15
F-1031, Section 2115
Introduction
This instruction contains the information needed for operation and maintenance of CS Series centrifugal pumps. Since there
are several types of transmissions available for these pumps, they are covered in separate instructions.
General Description
The CS Series pumps are single stage centrifugal fire
pumps. They are designed for midship mounting and are
available in capacities ranging from 750 to 2250 gpm
(2850 to 8500 l/m).
A variation of the basic pump is the CSH pump. This two
stage pump has an extra pressure stage designed for
high pressure operation. It is identical to the CS except for
the added stage and piping.
Components
Body Assembly
This assembly includes the body, cover, intake adapters
and related parts. The body, cover and adapters are either
cast iron or bronze.
Impeller Shaft Assembly
This assembly consists of the bronze impeller mounted on
a stainless steel shaft with wear rings, packing or me‐
chanical seal and related parts. The impeller is balanced
and the impeller shaft is supported by ball bearings.
Options
Mechanical Seals
A mechanical seal consists of a flat, highly polished
(lapped), spring-fed carbon ring that is sealed to and ro‐
tates with the impeller shaft. It presses against a highly
polished (lapped), silicone carbide, stationary ring that is
sealed in the pump body. This seals the shaft and pre‐
vents air from entering and water from leaving. A mechan‐
ical seal does not leak or drip water, even when pumping.
Flame-Plated Impellers
Approximately 75% of the pump wear due to pumping
sand, occurs on the impeller hubs. For this reason, the
Waterous Company adopted the policy of offering a flame
plated impeller as an option (standard on CSU pumps).
The flame-plating process consists of adding tungsten
carbide to the surfaces to be protected from wear. This
unique process produces extremely hard, well bonded,
wear-resistant coatings which consistently outwear hard
chrome plating, tool steel and solid tungsten carbide.
Monarch Intake Valve
The Monarch intake valve is a package including an extra
short intake fitting, an intake butterfly valve and an intake
nipple with integral relief valve mounting pad, all designed
to fit behind the pump panel. The Monarch intake valve
also features a provision for a pre-valve relief valve and
choice of manual worm gear, pneumatic or 12 or 24 volt
electric actuator. For operation and maintenance instruc‐
tions for the Monarch intake valve, see the following in‐
structions:
•
F-1031, Section 2318
, Operation, Maintenance and
Installation Instructions for Butterfly Valves
•
F-1031, Section 2319
, Operation, Maintenance and
Installation Instructions for Butterfly Valve Pneumatic
Actuator
Extra Pressure Stage
The extra pressure stage provides extra pressure without
the need of a separate PTO driven pump. When the extra
pressure stage control valve is opened, water enters the
extra pressure stage intake from the main pump dis‐
charge, and is discharged at a higher pressure. With the
extra pressure stage in operation, the CSH pump devel‐
ops pressure up to 500 psi (1900 l/m) for two or more
booster lines. The extra pressure body mounts on the
main body opposite the pump drive end. The impeller is
mounted on the same shaft as the other impeller and ro‐
tates whenever the pump is in operation. When the extra
pressure stage is not in use, water from the first stage
lubricates and cools the extra pressure stage stuffing box.
Intake Screens
Zinc die cast screens are normally used in the intake fit‐
tings, with brass screens available optionally. Although the
screens are chemically treated (coated) to inhibit corro‐
sion, the water being pumped may still corrode the
screens. Such corrosion is ``sacrificial”; that is, it will help
prevent corrosion in the rest of the pump the same way
the magnesium anodes protect the metal parts of a water
heater.
Anodes
As additional corrosion protection for iron body pumps,
Waterous has available zinc anodes to fit any unused
intake pad, 2-1/2 inch or 3 inch pipe tap in the intake
fittings. Anodes provide additional zinc surface to the wa‐
ter to supplement the zinc intake screens.