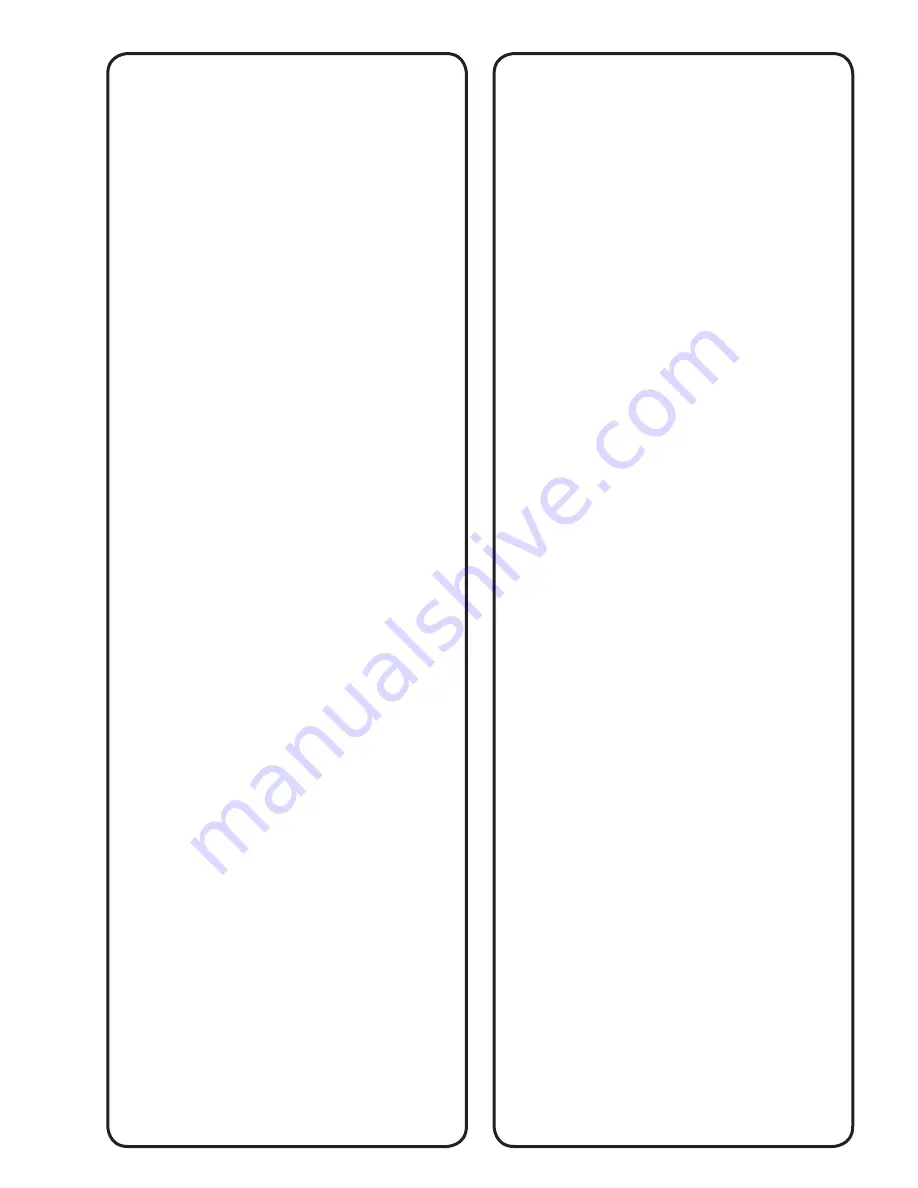
30119-16 Rev. 4.9/07-09
3
ELECTRONIC LOW PRESSURE METER
INDEX
I.
UNCRATING
II.
INSTALLATION
1.
Flanged Tube Meters
2.
Plain End Tube Meters
3.
Strap-On Saddle Meters
A.
Align
B.
Scribe
C.
Cut Out
D.
Straightening Vanes
E.
Meter Assembly
III. OPERATION AND MAINTENANCE MANUAL
IV. METER SADDLE ASSEMBLY
V.
WORKING
AREA
VI. DISASSEMBLY & INSPECTION
1.
Propeller Removal
2.
Reverse Thrust Bearing Cartridge
3.
Water Lubrication
4.
Ceramic Bearing Cartridge
5.
Spindle Ceramic Sleeve
6.
Separator/Support Spindle Assembly
VII. REASSEMBLING
METER
1.
Propeller Installation
2.
Thrust Bearing Cartridge Assembly
3.
Propeller Bearing
VIII. SENSOR & FC101 DIGITAL INDICATOR-TOTALIZER
1.
FC101 Digital Indicator
2.
FC101 Removal
3.
Sensor Housing
4.
Replacing Sensor Housing
5.
Inspect O-ring
6.
Lithium Battery
7.
FC101 Digital Indicator-Totalizer
IX. PREPARATION PRIOR TO INSTALLING METER
1
. Propeller Assembly
2.
FC101
3.
Meter Saddle O-ring
X. ORDERING PARTS OR RETURN TO FACTORY
ELECTRONIC LOW PRESSURE METER
INSTALLATION
I.
UNCRATING.
When uncrating the meter, any damage due
to rough or improper handling should be reported to the
transportation firm and McCrometer. If, for any reason,
it is determined that the unit or parts of the unit should
be returned to the factory, please contact McCrometer for
clearance prior to shipment. Each unit must be properly
crated to prevent any further damage. The factory as-
sumes no responsibility for equipment damage in return
shipment due to improper packaging. The shipping crate
contains the following items:
Low Pressure Meter Assembly with FC101 .................1
Mounting Equipment as required ...................................-
Operation and Maintenance Manual .............................1
Tool T-2402X-1 ..........................................................1
II. INSTALLATION
of McCrometer Low Pressure Electronic
Meters varies depending upon the type and model of meter
selected for each application. The meter must have a
full flow of liquid for proper accuracy. Fully opened gate
valves, fittings, or other obstructions that tend to set
up flow disturbances should be a minimum of ten pipe
diameters upstream and two pipe diameters downstream
from the meter. Installations with less than ten pipe
diameters of straight pipe require straightening vanes.
Meters with straightening vanes require at least five pipe
diameters upstream and one pipe diameter downstream
from the meter. The meter installations fall into three
basic categories:
1. FLANGED
TUBE
METERS
can be installed exactly
as you would install any short length of flanged pipe.
Flanged ends are standard pattern and drilling for any
meter size.
2. PLAIN END TUBE METERS
can be installed similar
to replacing a short length of plain end pipe in the line by
either welding or using one of a variety of pipe couplings
available.
Note:
Meter saddle assembly (#26) should be
removed before welding. (See step IV.)
3. STRAP-ON SADDLE METERS
can be installed on
an existing pipeline by cutting a hole of proper size in the
existing pipeline. The installation steps outlined below
should be followed carefully to achieve proper mounting
of the meter:
A. ALIGN
the cutout template in the desired position for
the meter on the pipe. Make certain that the center line
of the pipe and the center line marked on the template
are parallel with each other.
B. SCRIBE
the pipe along the line specified for your
meter size cutout.
C. CUT
OUT
the section of pipe within the scribed line
and remove all burrs, slag, and rough edges from the inside
and outside of the cutout section.