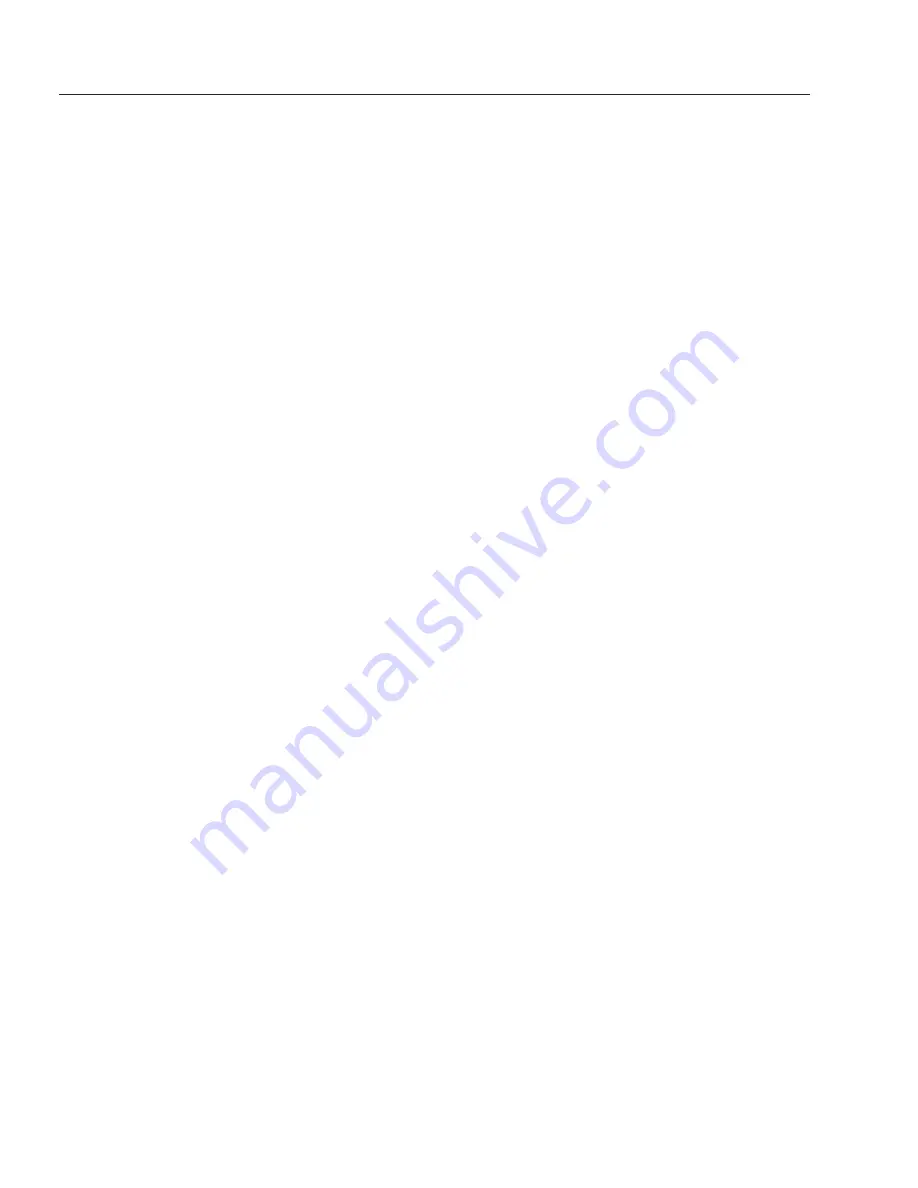
6
HBG EVAPORATOR
OPERATOR’S MANUAL
HBG • 8.913-990.0-K
STANDARD
SAFETY FEATURES
The HBG uses gas and electricity to op er ate. This can
be a fatal com bi na tion if not handled prop er ly. For this
rea son, the HBG has been designed with safe ty in mind.
You will fi nd these standard safe ty features on all HBG
equip ment:
1.
Batch Cycle Controller
This controller counts how many times the ma chine
has evap o rat ed and re fi lled. At a pre de ter mined
num ber of batch cycles, the controller will shut down
the evap o ra tor. Main te nance must be per formed
be fore the batch cy cle controller is re set.
2.
Low Water Float Switch
This fl oat switch insures that there is water cov er-
ing the fl oor of the evaporator. When the water lev el
drops to a certain level, the low water fl oat switch
turns off the burner.
3.
High Water Float Switch
This fl oat will turn off the HBG when the water lev el
be comes too high.
4.
On-Off Switch
The burner on-off switch dis con nects power to the
burn er.
5.
High Tem per a ture Switch with Manual Reset
If the underneath fl oor temperature below the tank
exceeds 500° for the HBG-15 & HBG-30, the manual
reset temperature switch will trip, turning off the
burner. To reset, push the black button on the side
of the electrical box.
6.
High Temperature Alarm
Included with your HBG is a combination strobe
light and horn alarm that will warn of a high tem-
perature condition within the HBG tank. This alarm
is automatically actuated on high temperature by
two thermal switches mounted on the outside wall
of the tank. These thermal switches are factory set
at 300° F and are designed to set off the strobe/horn
alarm as well to shut down the machine. This alarm
unit must be fi eld mounted (see page 26) and wired
(see wiring diagram) to the HBG control panel. The
strobe light has a fl ash rate of 75 fl ashes/minute. The
audio alarm has a sound level of 81 dBA @ 10ft.
INSTALLATION
1.
LOCATION
-Locate the HBG evaporator on a con-
crete surface and level with leveling feet supplied
with the machine.
NOTE
: Leveling feet must be screwed into the bot-
tom of the fl ame box when it is removed from pal-
let. HBG-30's must have fi fth leveling foot screwed
into the burn er support bracket located below the
burner. Burn er sup port bracket is to keep the burn er
level at all times. Pro tect machine from damaging
en vi ron ments such as wind, rain, sun and freezing
tem per a tures.
CAUTION: For natural gas, air ven ti la tion should
be lo cat ed near the ceiling. For liquid pro pane,
air ven ti la tion should be located near the fl oor.
Air ven ti la tion open ings and evaporator stack
should be lo cat ed a safe dis tance from build ing
cli mate con trol air in take ducts.
2.
ELECTRICAL
-The standard HBG requires 120
volts. Re fer to the se ri al plate for proper volt age and
amp re quire ments for your machine. All elec tri cal
lines must be tested with a volt age meter for proper
volt age and polarity be fore con nect ing to the HBG.
CAUTION: All electrical lines must be installed
by qualifi ed personnel only. All installations must
be elec tri cal ly grounded and conform to all local
and Na tion al Electrical codes.
NOTE:
The serial plate lists multiple AMP ratings.
Use the one that matches your purchased unit and
options. The fi rst Amp rating on the serial plate is
the standard unit with no air or electrical-powered
options. The AIR Option Amp rating is for the unit with
any air-powered auto-fi ll and/or chemical defoamer
injection options. The ELEC Option Amp Rating is for
the unit with any electric motor or solenoid-powered
auto-fi ll and/or chemical de-foamer injection options.
Refer to the Amp rating that applies to your unit when
installing.
Use a strain relief at the rear of the control panel
for con nect ing to the main power supply. Elec tri cal
con duit must be run all the way to the con nec tion
point in ac cor dance with local codes. To con nect
the pow er wires inside the elec tri cal box, lo cate the
wir ing ter mi nal strip and follow wiring di a gram to
make sure black wire is connected to the prop er
ter mi nal. Con nect the white neu tral wire to ter mi nal
#N. Then con nect the ground wire to the ground ing
stud on the back of the elec tri cal box. Con fi rm that
volt age is go ing to the cor rect ter mi nals.
3.
AUTO FILL FLOAT
- Remove fl oat wires from pump
switch (black and white wires). With strain relief sup-
plied, attach to waste wa ter tank near bottom and
thread fl oat wires through strain relief and tight en.
Note:
Leave at least a 3 inch tether from the strain
relief for fl oat to work correctly. Re wire fl oat wires
into pump switch.
4.
GAS PIPING
- All piping must comply with local
codes and ordinances or the National Fuel Gas Code
ANSI Z223. 1-1984 and NFPA No. 54. A sed i ment
trap or drip leg must be installed in the sup ply line
to the burn er.