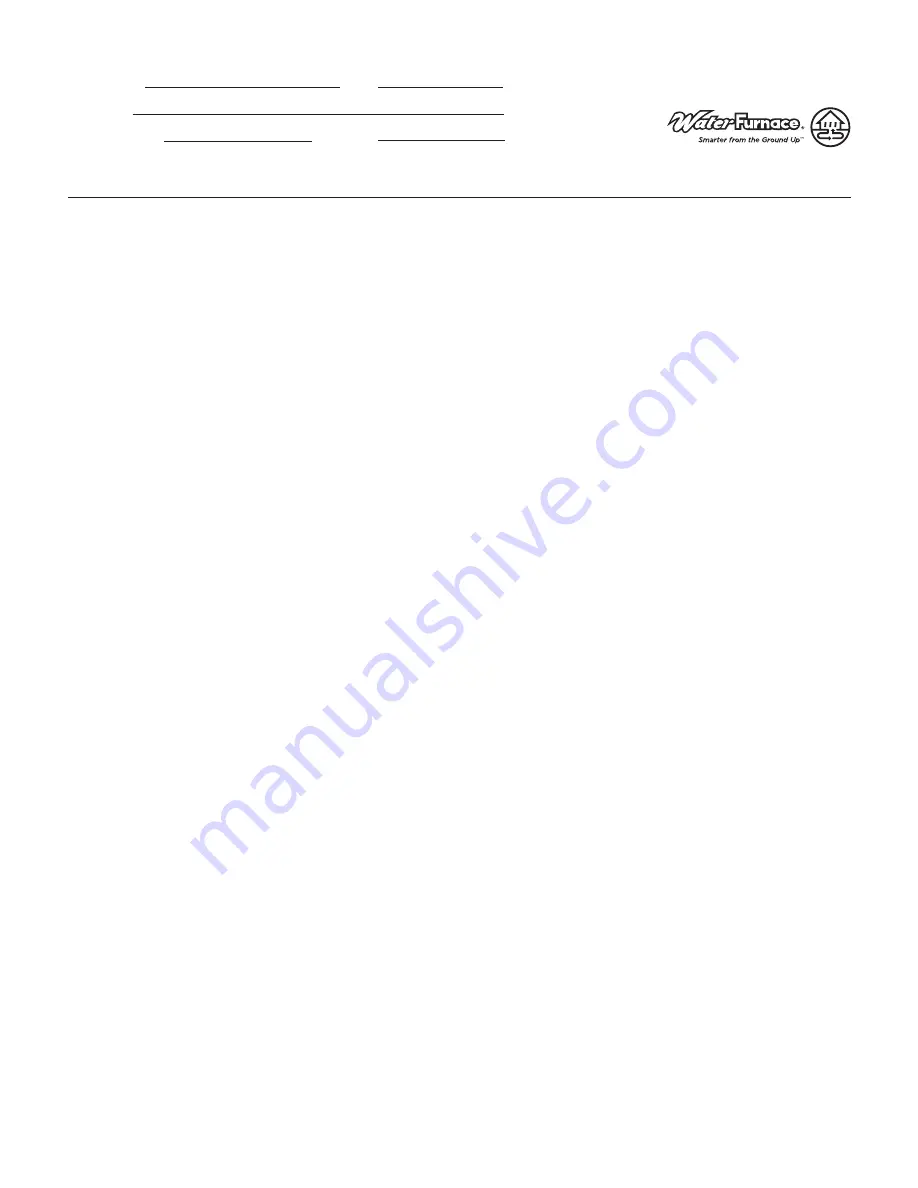
WaterFurnace works continually to improve its products. As a result, the design and specifi cations of each product at the time of order may be changed without notice. Please contact WaterFurnace at 1-888-929-2837 for latest design and
specifi cations. Purchaser’s approval of this data set signifi es that the equipment is acceptable under the provisions of the job specifi cation. Statements and other information contained herein are not express warranties and do not form the
basis of any bargain between the parties, but are merely WaterFurnace’s opinion or commendation of its products. The latest version of this document is available at www.waterfurnace.com.
Contractor: P.O.:
Engineer:
Project Name:
Unit Tag:
SD2552WNB 09/16
29
Page _____ of _____
ENVISION
2
NKW
REVERSIBLE CHILLER - 50Hz
Engineering Guide Specifi cations cont.
Heat Exchangers:
1.
The water to refrigerant heat exchangers shall be
dual circuit, copper-brazed 316 stainless steel channel
plates, capable of withstanding 4.5MPa psig working
pressure on the refrigerant side and 3.1MPa psig on
the water side. Refrigerant circuits are separate with a
common water supply. This provides optimal part load
efficiency compared to using two single circuit heat
exchangers. Heat exchangers are designed to work as
an evaporator and condenser.
2.
Heat exchangers are covered with 19mm closed-cell
insulation on sizes 030-060 and 25mm closed-cell
insulation on sizes 090-150.
3.
Water line connections attached to the heat
exchangers are groove type are factory installed
with groove coupling and steel pipe nipple. Pipe
nipple is insulated and comes with 1/4" NPT pressure/
temperature port.
Refrigerant Components:
1.
Unit shall utilize R-410A refrigerant type. All system
components shall be rated to appropriate UL standards
to handle maximum system pressure.
2.
Factory charged, sealed system contains optimal
refrigerant quantity.
3.
Each refrigerant circuit shall utilize a thermostatic
expansion valve (TXV) with stainless steel sensing bulb
and laser welded diaphragm. TXV will control adequate
superheat over the stated operating range as indicated
in submittal data.
4.
Bidirectional, liquid line filter driers are to be factory
installed to provide additional system cleanliness.
5.
Factory installed service ports for high and low
pressure readings.
6.
Optional factory installed pressure gauges mounted
below control panel aid in field diagnostics and
reduces need for technician applied gauges.
Control Panel
1.
Factory installed, wired, and functionally tested at
factory before shipment.
2.
Single-point power connection to non-fused, or fused
rotary-type disconnect in control panel.
3.
Factory installed, DIN mounted CUBEFuse with Class J
rating wired for protection of each compressor.
4.
Low voltage, emergency stop button factory wired and
mounted to control panel service door.
5.
Factory mounted class 2, control power transformer
provides nominal 24 VAC low voltage power supply.
Primary to transformer is protected by Class CC fuses.
6.
High pressure cut out set at 4.1MPa with manual reset.
7.
Low pressure cut out set at 275kPa with manual reset.
8.
Unit shall have phase loss/reversal for
compressor protection.
Controls:
1.
The unit shall be controlled using a microprocessor
which sequences all functions and modes of operations.
2.
Units shall be capable to communicate thru standard
DDC protocols such as N2, Lon, and BACnet (MS/TP @
19,200 Baud Rate).
3.
Standalone, non-communicating units are also
available that will operate with thermostat, mechanical,
or electronic signals. Temperature set mode is capable
of controlling to leaving/entering load temperature.
4.
The control system shall have the following features:
•
Anti-short cycle time delay of 5 minutes on
compressor operation.
•
Random start on power up mode
•
Low voltage protection
•
High voltage protection
•
Unit shut down on high or low refrigerant pressures
•
Unit shut down for freeze detection
•
Source and Load heat exchanger freeze detection
setpoint selectable for water or antifreeze
•
Automatic intelligent reset
5.
A 4 x 20 digit backlit LCD to display the following:
•
Entering and leaving water temperatures
•
High pressure, low pressure, low voltage, high
voltage, freeze detection setpoint, and control status
•
The low pressure shall not be monitored for
the first 120 seconds after a compressor start
command to prevent nuisance safety trips
•
Remote fault indication on the thermostat
•
An accessory relay output tied to each compressor
selectable for normally open or normally closed
6. Control
Inputs:
• Start/Stop
• Lead/Lag
•
Freeze detection set point for load/source
•
Water temperature set point
• Control
Outputs:
• Status:
Cooling/Heating/On/Off
•
Load Side Supply and Return Temperatures
•
Source Side Supply and Return Temperatures
•
Evaporator Entering Refrigerant Temperatures
•
Condenser Leaving Refrigerant Temperatures
Accessories:
1.
Additional Items Not Listed Previously:
•
Compressor sound blankets to reduce sound
power level of unit.
•
Flow switch to monitor the units presence of flow.
2.
Flow Proving Switch
•
A flow proving switch shall be available utilizing
high reliability flow sensing technology.