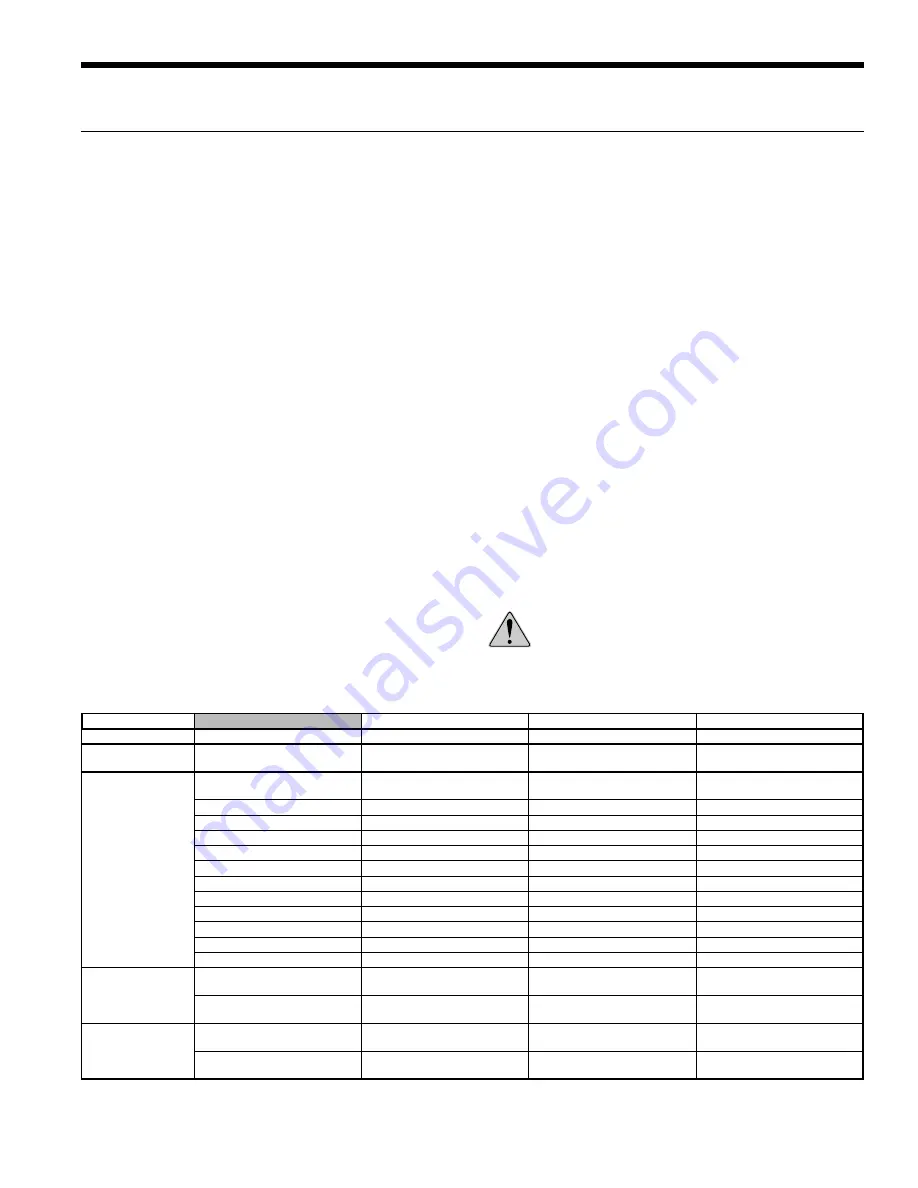
9
5 SERIES 502W12 INSTALLATION MANUAL
The following table outlines the water quality guidelines for unit
heat exchangers. If these conditions are exceeded, a secondary
heat exchanger is required. Failure to supply a secondary heat
exchanger where needed will result in a warranty exclusion for
primary heat exchanger corrosion or failure.
Strainers
These units must have properly sized strainers upstream of
both brazed plate heat exchangers to protect them against
particles in the fluid. Failure to install proper stainers and
perform regular service can result in serious damage to the
unit, and cause degraded performance, reduced operating
life and failed compressors. Improper installation of the unit
(which includes not having proper strainers to protect the
heat exchangers) can also result in voiding the warranty.
Field supplied strainers with 420-840 microns are
recommended, with 500 microns being the optimum choice.
The strainers selected should have a mesh open area of at
least 39 cm
2
for each unit being serviced by the strainer. Using
strainers with a smaller amount of open area will result in the
need for more frequent cleaning.
Strainers should be selected on the basis of acceptable
pressure drop, and not on pipe diameter. The strainers
selected should have a pressure drop at the nominal flow rate
of the units; low enough to be within the pumping capacity of
the pump being used.
WARNING: Must have intermediate heat
exchanger when used in pool applications.
General
Reversible chiller systems may be successfully applied in a
wide range of commercial and industrial applications. It is the
responsibility of the system designer and installing contractor
to ensure that acceptable water quality is present and that all
applicable codes have been met in these installations.
Water Treatment
Do not use untreated or improperly treated water. Equipment
damage may occur. The use of improperly treated or
untreated water in this equipment may result in scaling,
erosion, corrosion, algae or slime. The services of a qualified
water treatment specialist should be engaged to determine
what treatment, if any, is required. The product warranty
specifically excludes liability for corrosion, erosion or
deterioration of equipment.
The heat exchangers in the units are 316 stainless steel plates
with copper brazing. The water piping in the heat exchanger
is steel. There may be other materials in the building’s piping
system that the designer may need to take into consideration
when deciding the parameters of the water quality.
If an antifreeze or water treatment solution is to be used, the
designer should confirm it does not have a detrimental effect
on the materials in the system.
Contaminated Water
In applications where the water quality cannot be held to
prescribed limits, the use of a secondary or intermediate heat
exchanger is recommended to separate the unit from the
contaminated water.
Water Quality
Water Quality Guidelines
Material
Copper
90/10 Cupronickel
316 Stainless Steel
pH
Acidity/Alkalinity
7 - 9
7 - 9
7 - 9
Scaling
Calcium and
Magnesium Carbonate
(Total Hardness)
less than 350 ppm
(Total Hardness)
less than 350 ppm
(Total Hardness)
less than 350 ppm
Corrosion
Hydrogen Sulfide
Less than 0.5 ppm (rotten egg
smell appears at 0.5 ppm)
10 - 50 ppm
Less than 1 ppm
Sulfates
Less than 125 ppm
Less than 125 ppm
Less than 200 ppm
Chlorine
Less than 0.5 ppm
Less than 0.5 ppm
Less than 0.5 ppm
Chlorides
Less than 20 ppm
Less than 125 ppm
Less than 300 ppm
Carbon Dioxide
Less than 50 ppm
10 - 50 ppm
10 - 50 ppm
Ammonia
Less than 2 ppm
Less than 2 ppm
Less than 20 ppm
Ammonia Chloride
Less than 0.5 ppm
Less than 0.5 ppm
Less than 0.5 ppm
Ammonia Nitrate
Less than 0.5 ppm
Less than 0.5 ppm
Less than 0.5 ppm
Ammonia Hydroxide
Less than 0.5 ppm
Less than 0.5 ppm
Less than 0.5 ppm
Ammonia Sulfate
Less than 0.5 ppm
Less than 0.5 ppm
Less than 0.5 ppm
Total Dissolved Solids (TDS)
Less than 1000 ppm
1000 - 1500 ppm
1000 - 1500 ppm
LSI Index
+0.5 to -0.5
+0.5 to -0.5
+0.5 to -0.5
Iron Fouling
(Biological Growth)
Iron, FE
2
+ (Ferrous)
Bacterial Iron Potential
< 0.2 ppm
< 0.2 ppm
< 0.2 ppm
Iron Oxide
Less than 1 ppm, above this
level deposition will occur
Less than 1 ppm, above this
level deposition will occur
Less than 1 ppm, above this
level deposition will occur
Erosion
Suspended Solids
Less than 10 ppm and filtered
for max. of 600 micron size
Less than 10 ppm and filtered
for max. of 600 micron size
Less than 10 ppm and filtered
for max. of 600 micron size
Threshold Velocity
(Fresh Water)
< 1.8 m/sec
< 1.8 m/sec
< 1.8 m/sec
NOTES:
Grains = ppm divided by 17
mg/L is equivalent to ppm
2/22/12
Summary of Contents for 502W12
Page 2: ......