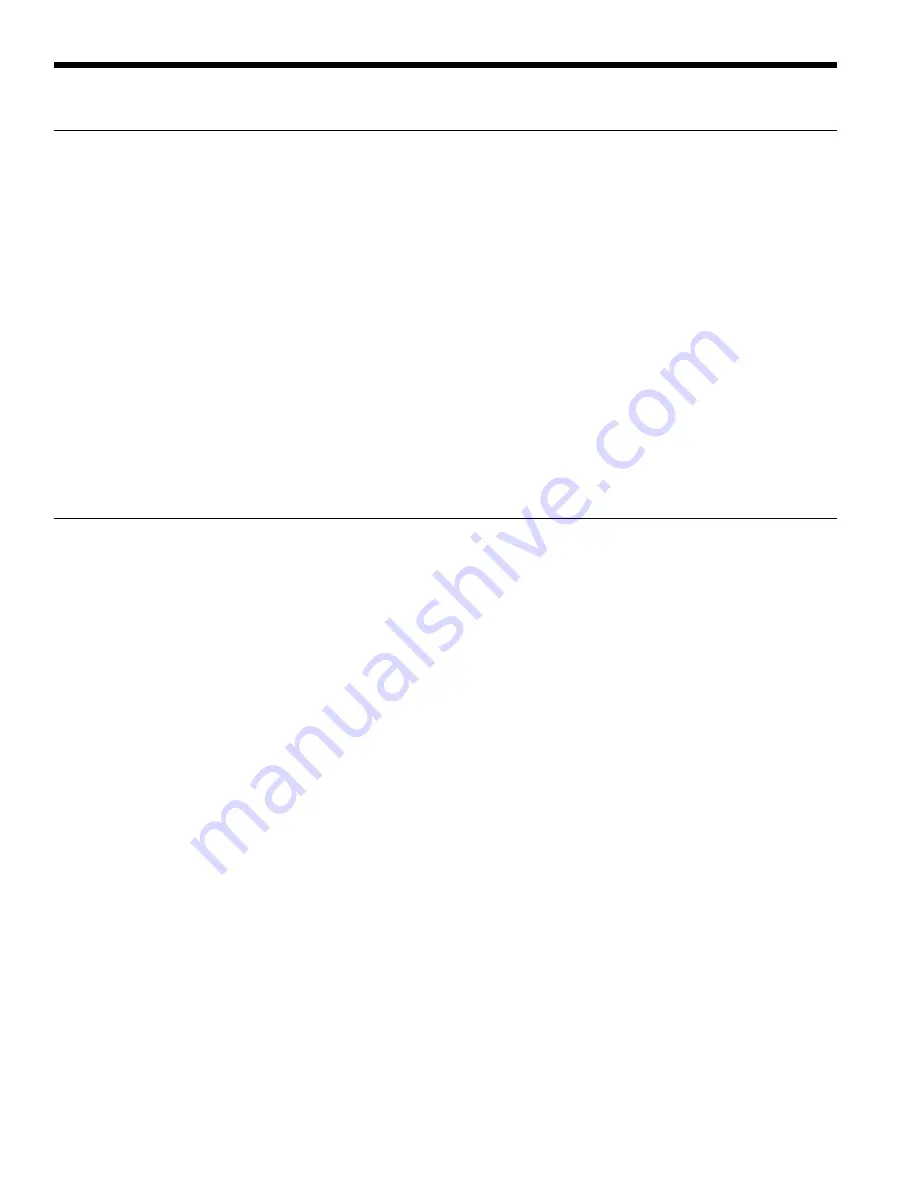
18
5 SERIES 502W12 INSTALLATION MANUAL
Field Wiring and Control Setup cont.
Accessory Relay Setup
The accessory output set to “close” upon Y1 compressor call
(compressor is delayed 90 sec. after Y1) but can be set to
“open” with Y1.
To change ACC1:
• Using up and down keys, scroll to “Acc 1 Sel” hit “ENTER”
and “ON Comp” begins flashing
• Using up and down keys, select “ON Comp” for activation
with Y1 Call or “OFF Comp” for deactivation with Y1
Lead/Lag Selection
Compressor Lead/Lag Selection is factory set to “ON” but
can be set to “OFF”.
To change Lead/Lag On/Off:
• Using up and down keys, scroll to “LEAD/LAG SELECT”
hit “ENTER” and “OFF” begins flashing
• Using up and down keys, select “ON” for activation or “
OFF” for deactivation
°F or °C - Unit of Measure
Degrees Fahrenheit is factory set, however degrees Celsius
can be selected using the following procedure:
To Change Unit of Measure:
• On FX10 control using up and down keys, scroll
to “SETTINGS”
• Using up and down keys, scroll to “UNIT OF MEASURE”
hit “ENTER” and “UNIT OF MEASURE” begins flashing
• Using up and down keys, select “F” for degrees
Fahrenheit or “C” for degrees Celsius
Other Field Options
Other field selectable options are available as shown
in the maintenance menu on page 24 of the FX10
control using a similar procedure as shown in the above
examples. These would include thermostat enabling, and
emergency shutdown.
Anti Short Cycle
High Pressure Protection
Low Pressure Protection
Advanced Freeze Detection Setpoint
Random Start
Display for diagnostics
Reset Lockout at disconnect
Intelligent reset for field installed flow switches
1 Accessory output
Compressor Lead/Lag
Compressor Current Switches
Field Selectable Options
Freeze Detection Sensing Select (DI-4 and DI-5)
The freeze detection temperature sensing selection inputs
allow the user to adjust the setpoints. The source sensors
are wired to inputs AI-3 and AI-4 while the load sensors are
wired to inputs AI-5 and AI-6. The setpoints for both, the
load and source, are factory set for 30°F. In order to change
the setpoint to 15°F on the source, remove the jumper wire
from DI-4 (wire #56). The load setpoint can be changed by
removing the jumper wire from DI-5 (wire #55).
Accessory Output (DO-4)
The accessory output will be energized 90 seconds prior
to the lead compressor output being energized. When the
lead compressor output is turned off the accessory output
will be deactivated immediately. The output is selectable for
normally open or normally closed operation through the unit
mounted user interface or from a building automation system.
Control and Safety Features
Emergency Shutdown
The emergency shutdown mode can be activated by a
command from a facility management system or a closed
contact on DI-2. The default state for the emergency
Control Features
shutdown data point is off. When the emergency shutdown
mode is activated, all outputs will be turned off immediately
and will remain off until the emergency shutdown mode is
deactivated. The first time the compressor starts after the
emergency shutdown mode has been deactivated, there
will be a random start delay present.
Lockout Mode
Lockout mode can be activated by any of the following
fault signals: refrigerant system high pressure, refrigerant
system low pressure, heating freeze detection, cooling
freeze detection, and compressor current sensor. When any
valid fault signal remains continuously active for the length
of its recognition delay, the controller will go into fault
retry mode, which will turn off the compressor. After the
Compressor short cycle delay, the compressor will attempt
to operate once again. If three consecutive faults are
recognized during a single heating or cooling demand, the
unit will go into lockout mode, turning off the compressor
and enabling the alarm output until the controller is reset.
The fault count will automatically reset when the heating or
cooling command becomes satisfied. If a fault occurs on a
dual compressor unit, the other compressor will continue
to operate based on the heating or cooling demand. The
lockout condition can be reset by powering down the
controller by holding both the enter and escape keys on the
optional user interface.
Advanced Freeze Detection System
The source and load heat exchangers are protected by a
multi-sourced temperature logic strategy. The temperature
logic is based upon the refrigerant temperature sensed as
the refrigerant is about to enter the heat exchanger; while
entering and leaving water temperatures are being used as
correlating factors. The detection scheme is shown as basic
and advanced algorithms.
Summary of Contents for 502W12
Page 2: ......