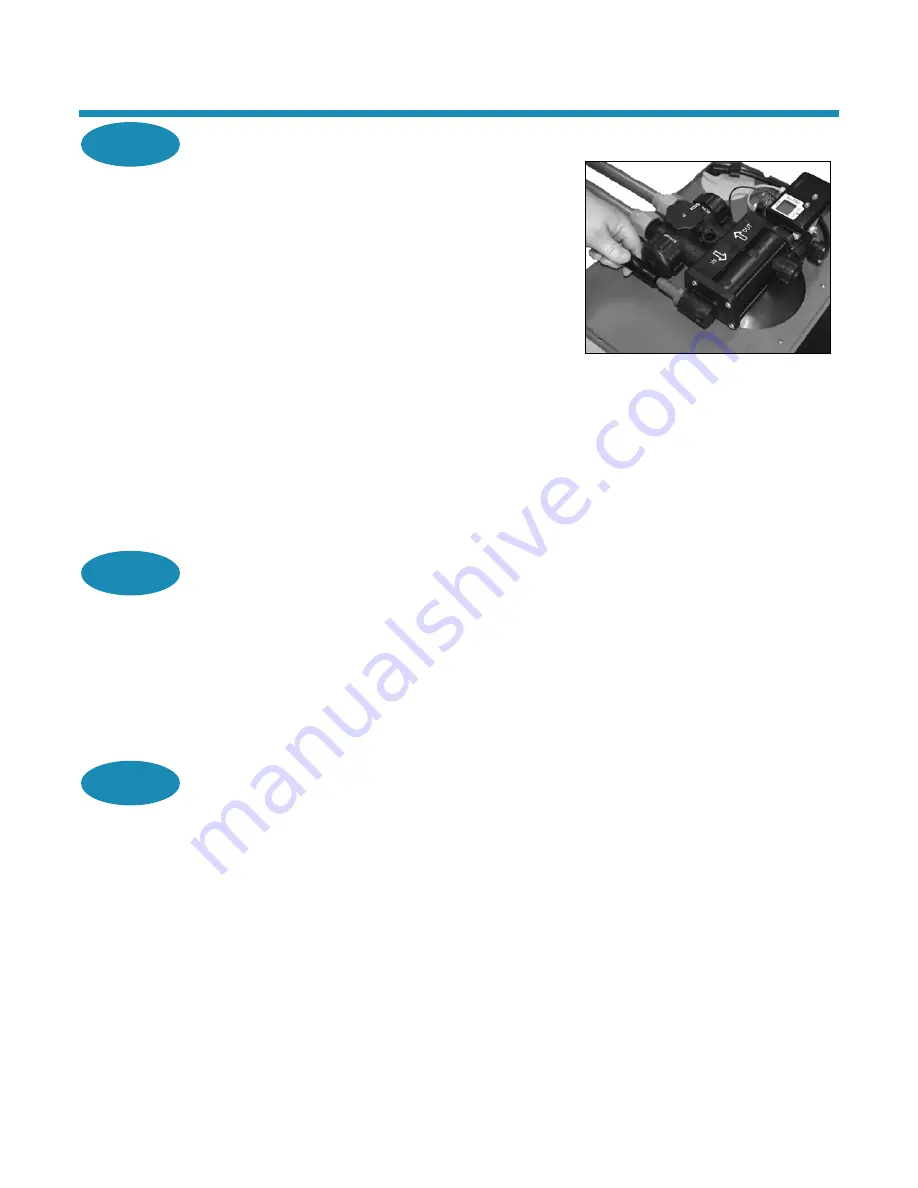
Installation Steps and Start-Up Procedures, Cont.
Step 5
Connect Drain Line
The drain line carries away the backwash water as part of the
regeneration cycle.
A.
Connect the drain line to the drain end cap
(See Figure 5) with a minimum 5/8-inch I.D. tubing
(supplied). The size cannot be reduced.
1.
To prevent leakage, wrap the threads on the drain
fitting three times with 1/2-inch wide Teflon tape, or
use plumber’s putty.
2.
Screw the drain fitting (See Figure 5) into the drain
end cap until fewer than three threads are visible.
Figure 5: Connect Drain Line
B.
Route the drain line to a floor drain, laundry tub, or other suitable waste receptor. Maintain a minimum
2-inch (5-cm) air gap between the drain line and the flood level rim of the waste receptor to prevent
back-siphoning. This drain line should make the shortest run to the suitable drain.
C.
The drain line may be elevated up to 8 feet (2.4 m) from the discharge on the appliance as long as
the water pressure in your system is 40 psi (2.8 bar) or more.
D.
If the drain line is 25 feet (7.6 m) or longer, increase the drain line and adapter to 3/4-inch I.D. The
end of the drain line must be equal to or lower in height than the control valve.
Caution: The drain line must not be kinked, crimped, or restricted in any way.
Step 6
Flush Lines
A.
Place the appliance in the Bypass position. (See Figure 6.)
B.
Turn on the main water supply.
C.
Open the nearest cold water faucet to flush the plumbing of any excess soldering flux, air, or any
other foreign material.
D.
Return the appliance to Normal Operation.
Note:
To prevent untreated water from entering your home, remember to not use water inside your
home when the appliance is in Bypass mode. Remember to return the appliance to Normal Operation
when you have finished using untreated water.
Step 7
Check for Leaks
A.
Close all faucets.
B.
Check all lines and connections for leaks. If leaks are found:
1.
Turn off the main water supply.
2.
Open a cold water faucet to depressurize the lines.
3.
Close the faucet to eliminate any siphoning action.
4.
Repair all leaks.
5.
Turn on the water supply.
6.
Place the appliance in the Service position to slowly fill the media tank. (See Figure 6.)
7.
Open a cold water faucet to purge air out of the media tank.
8.
Close the faucet and recheck for leaks.
WaterBoss Softener Two-Button Owner’s Manual
5/12/2011
9
Summary of Contents for PRO180
Page 22: ...Notes ...
Page 23: ...Notes ...