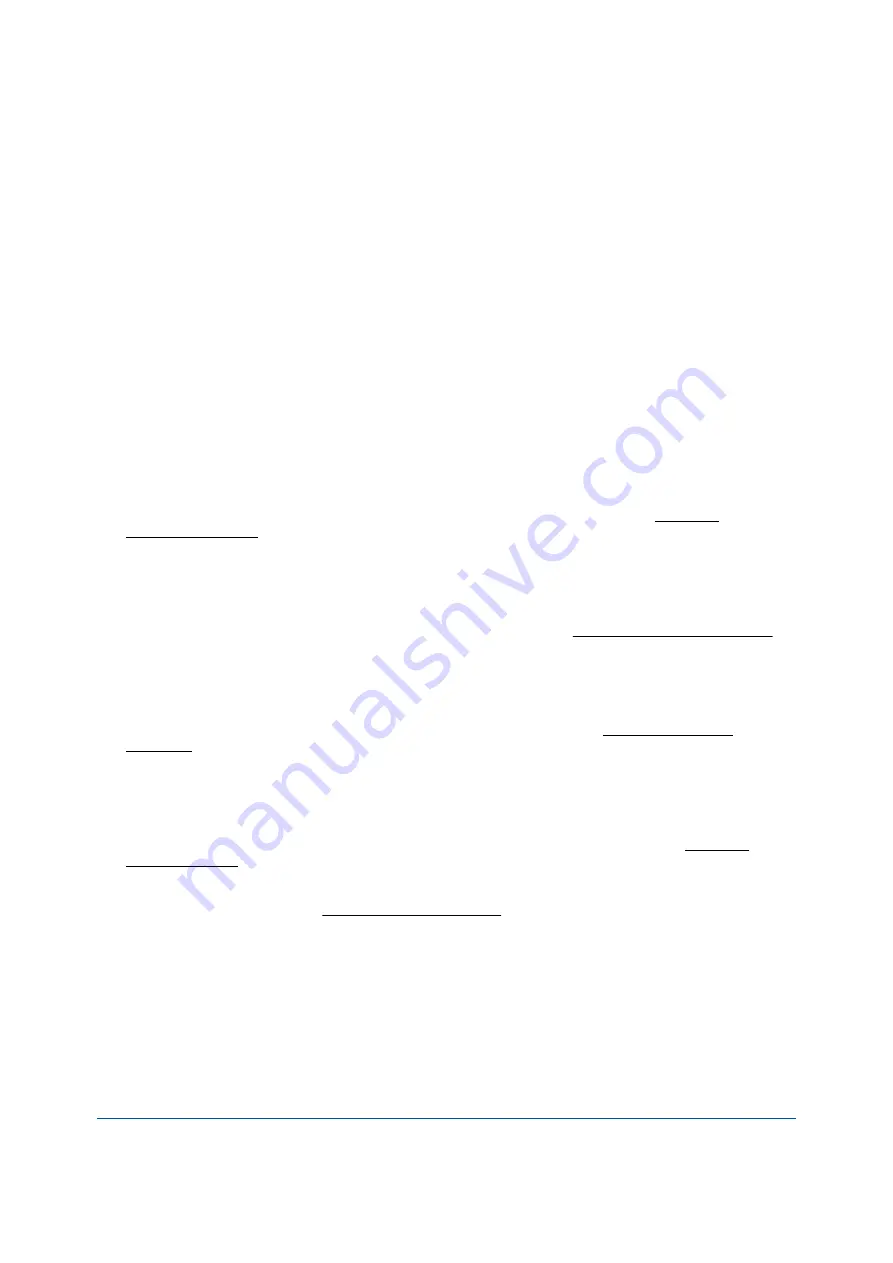
Installation Troubleshooting
Door not closing properly
•
Level the dishwasher.
Machine not starting or filling
•
Ensure water supply to machine is turned on.
•
Ensure power supply to machine is turned on.
•
Check that the water inlet hose isn’t twisted or kinked.
Cycle taking too long
•
This machine ships with Thermostop enabled, which allows a cycle to be started at any time,
even if the rinse water is not up to required temperature. To ensure a hygienic result, the
wash cycle continues to run until the rinse temperature reaches the required 83˚C. At this
stage washing will stop and the machine will begin rinsing to complete the cycle.
•
Check inlet water temperature is not too low as per our specifications.
Poor wash results
•
Check that there are adequate pre-rinse processes in place and staff use longer cycle options
for more heavily soiled items.
•
Ensure high quality non-foaming commercial dishwasher detergent has been connected at
the correct dosage for your site, water quality and application. If uncertain, consult a
chemical specialist.
•
Check that the wash arm is spinning freely and is not being obstructed.
•
Ensure that the wash temperature is between 60°C and 65°C.
Chemical residue on items after the cycle
•
Check that nothing is obstructing the wash and rinse arms from rotating.
•
Check the rinse fluid dosage is not too high. If uncertain, please consult a chemical specialist.
•
Check detergent dosage is within the requirements.
Dishwasher is foaming
•
Ensure there is no other soap being transferred into the machine from the sink.
•
Ensure high quality non-foaming commercial dishwasher detergent has been connected at
the correct dosage for your site and application. If uncertain, please consult a chemical
specialist.
•
Allow wash water to heat to at least 60˚C prior to starting the first cycle as some commercial
dishwasher chemical will foam at low temperatures.
Other equipment in the kitchen has needed filters or has scale
•
Due to the high temperatures in dishwashers, scale will build up in the wash tank, on the arms
and in the rinse tank. The incoming water should be treated. If uncertain, please consult a
water specialist.
•
As with combi-ovens, high chloride levels will do irreversible damage to a number of the
components inside a commercial dishwasher. The incoming water should be appropriately
treated. If uncertain, please consult a water specialist.
Cycle times not suitable for items being washed
•
Some sites may require longer or shorter cycles depending on the items being washed and
the soil levels. Cycle lengths can be adjusted by a qualified service agent accessing the WI-
200 Electronic timer. For adjustment instructions refer to the adjustment section of the
service manual for this model or the WI-200 Timer service manual.
Service Manual XP3
11
Revision 1F
Summary of Contents for XP Series
Page 1: ...XP PASSTHROUGH DISHWASHER SERVICE MANUAL...
Page 2: ...Service Manual XP3 2 Revision 1F...
Page 4: ...Service Manual XP3 4 Revision 1F...
Page 9: ...Service Manual XP3 9 Revision 1F...
Page 10: ...Service Manual XP3 10 Revision 1F...
Page 21: ...Service Manual XP3 21 Revision 1F...
Page 22: ...Service Manual XP3 22 Revision 1F...
Page 35: ...XP3 W WIRING DIAGRAM IMPORTANT Service Manual XP3 35 Revision 1F...
Page 39: ...RINSE PUMP KIT0440021 Service Manual XP3 39 Revision 1F...
Page 42: ...NOTES Service Manual XP3 42 Revision 1F...