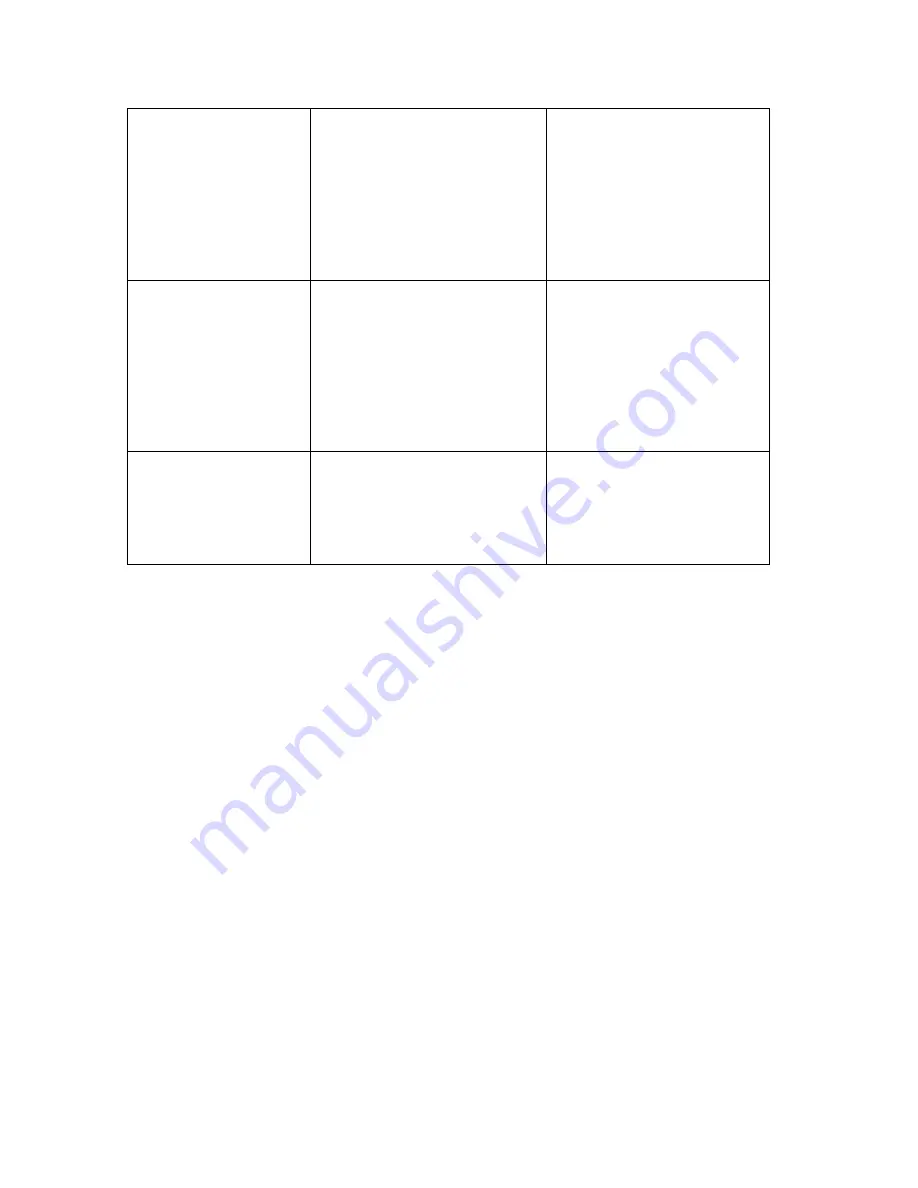
the equipment give
minimum current but
the current doesn’t
increases
i) Current regulator burnt OR
not working.
ii) Control transformer is
dead.
iii) Control rectifier is failed.
iv) Control fuse is blown.
i) Check & Replace
ii) Check & Replace
iii) Check & Replace
iv) Check & Replace
Welding arc is not
smooth and spatter is
more
i) Current setting is too high.
ii) DC polarity used for that
particular electrode is not
right.
iii) Diodes have failed.
i) Reduce the current.
ii) Use proper polarity
(Interchange the polarity
and check).
iii) Replace the diode OR
Diodes.
Mains fuse blows
i) Short circuit in the primary
of the main transformer.
ii) Short circuit in main diodes
i) Remove the short circuit.
ii) Replace the diodes.