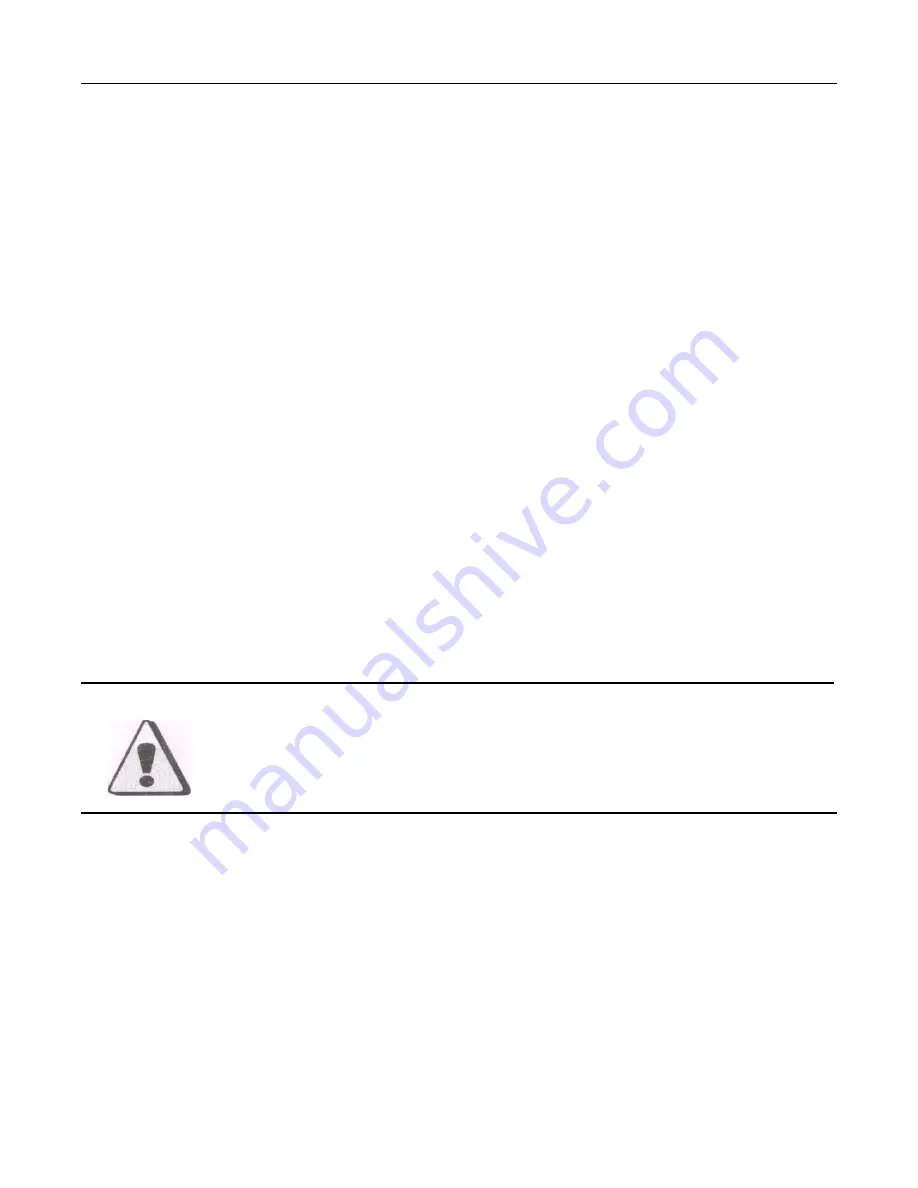
TIG WELDING DESCRIPTION
1.
Turn on the power switch at the Front panel digital current meter is normal, fan will start.
Make sure that the function switch on the front panel is in TIG Mode.
2.
Open the valve of argon cylinder, adjust the volume of flow meter and make it is adequate to
welding.
3. Press switch of torch, electromagnetic valve is started. Sound of HP arc striking can be heard, at the
same time argon is flowing from torch. NOTES: When welding is first operated, user must press switch
of torch several seconds and begin to weld until all of air is be drained out. When welding is over,
argon will still flow out for some seconds in order to protect welding spot before cooled down .So torch
must be kept in welding place some time after arc has been extinguished.
4. Set suitable welding current and make sure welding current is adequate to thickness of work piece
and process demand.
5. It is 2-4 mm from welding tungsten electrode to work piece, press control knob of torch, burn
and strike arc, sound of HF arc-striking will be diminished .The welding machine can be operated now.
STICKING DESCRIPTION
1. Open power switch of front panel, fan is beginning to work.
2. Make sure function switch of front panel is on MMA Mode.
3. Make sure welding current is adequate to thickness of work piece.
warning:
During welding, it is forbidden to pull off any plug or cable in use,
or it will lead to life-threatening danger and sever damage of the
machine.
OPERATION
Summary of Contents for INTIG 250
Page 6: ...IN TIG 250 ...