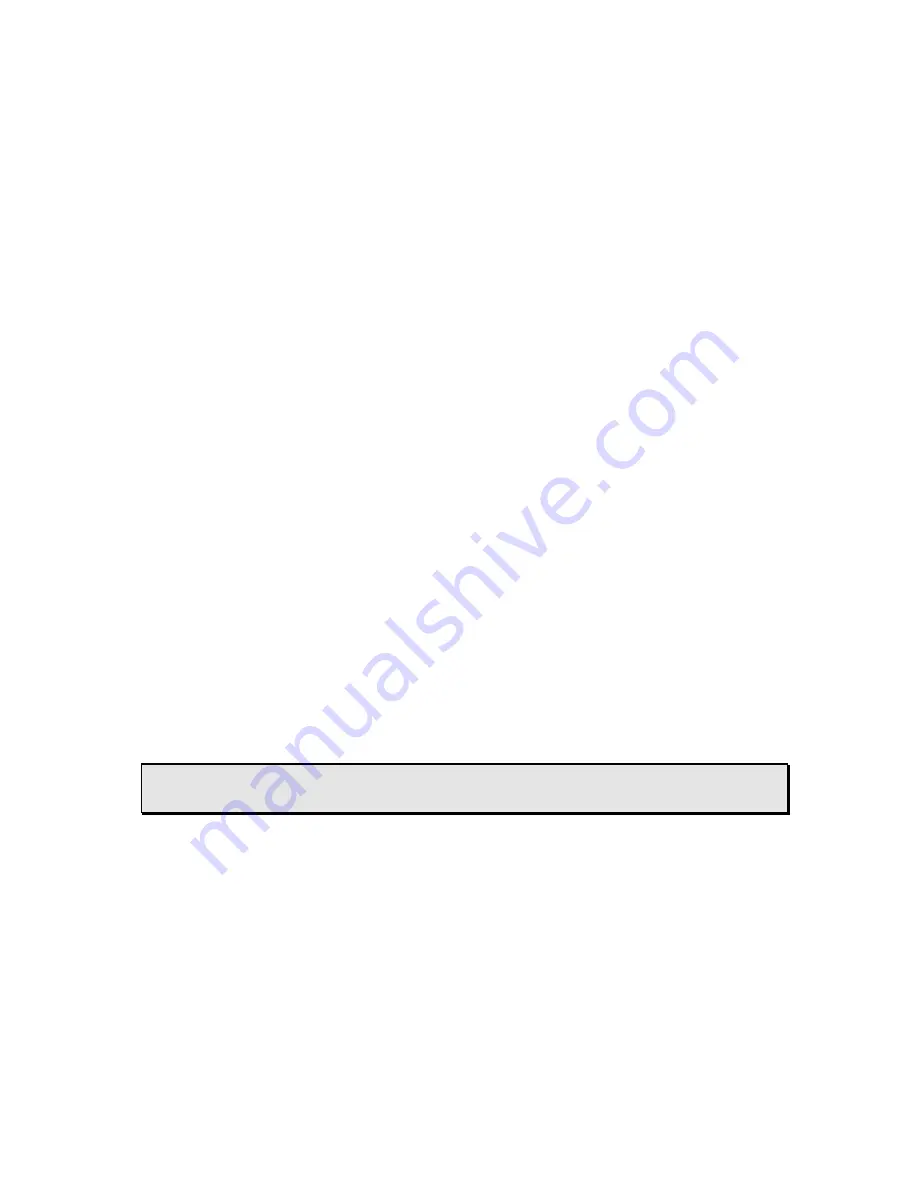
11
2.1.1 Shift between two working styles:
(1)
Shift from down-slope to non-down-slope
Switch to “TIG” mode, pull TIG torch trigger, then loose it, open load voltage of
power source will disappear to indicate working style being shifted to
non-down-slope.
(2)
Shift from non-down-slope to down-slope
Switch to “SMAW” mode from “TIG”, then back to “TIG” to complete shift.
2.1.2 Scratch arc-start with down-slope working style
Reference to 2.2.2 operation procedure
2.1.3 Scratch arc-start with non-down-slope working style
Reference to 2.2.3 operation procedure
2.2
Working styles on TIG mode of type STG series
Can be divided into 2 working styles: scratch arc-start and high frequency arc-start.
2.2.1 Shift between two working styles:
Shift scratch arc-start to high frequency arc-start
(1)Switch to “TIG” mode, then pull TIG torch trigger, then loose it, open load
voltage of power source will disappear to indicate working style is shifted to HF
arc-start.
(2)Shift HF arc-start to scratch arc-start
Switch to “SMAW” mode from “TIG”, then back to “TIG” to complete shift.
2.2.2 High frequency arc-start
Procedure flow sheet shows below :( Next page)
Repair and Maintenance
In principle, welders’ maintenance and repair should be completed by us or our authorized
distributors. Customers can also solve the problems instructed by us or our authorized
distributors.
1. Attention:
(1)
Rivet equipment name tag on the specified area of the case, otherwise the inside
parts will be damaged.
(2)
Connect welding cable to terminal lug firmly, otherwise the terminal lug will be
burn out which will lead to welding process instability.
(3)
Prevent jointer of welding cable and terminal lug from contacting with other
metals on the ground to avoid short circuit.
(4)
Operating carefully not to make welding and control cable to be worn out or