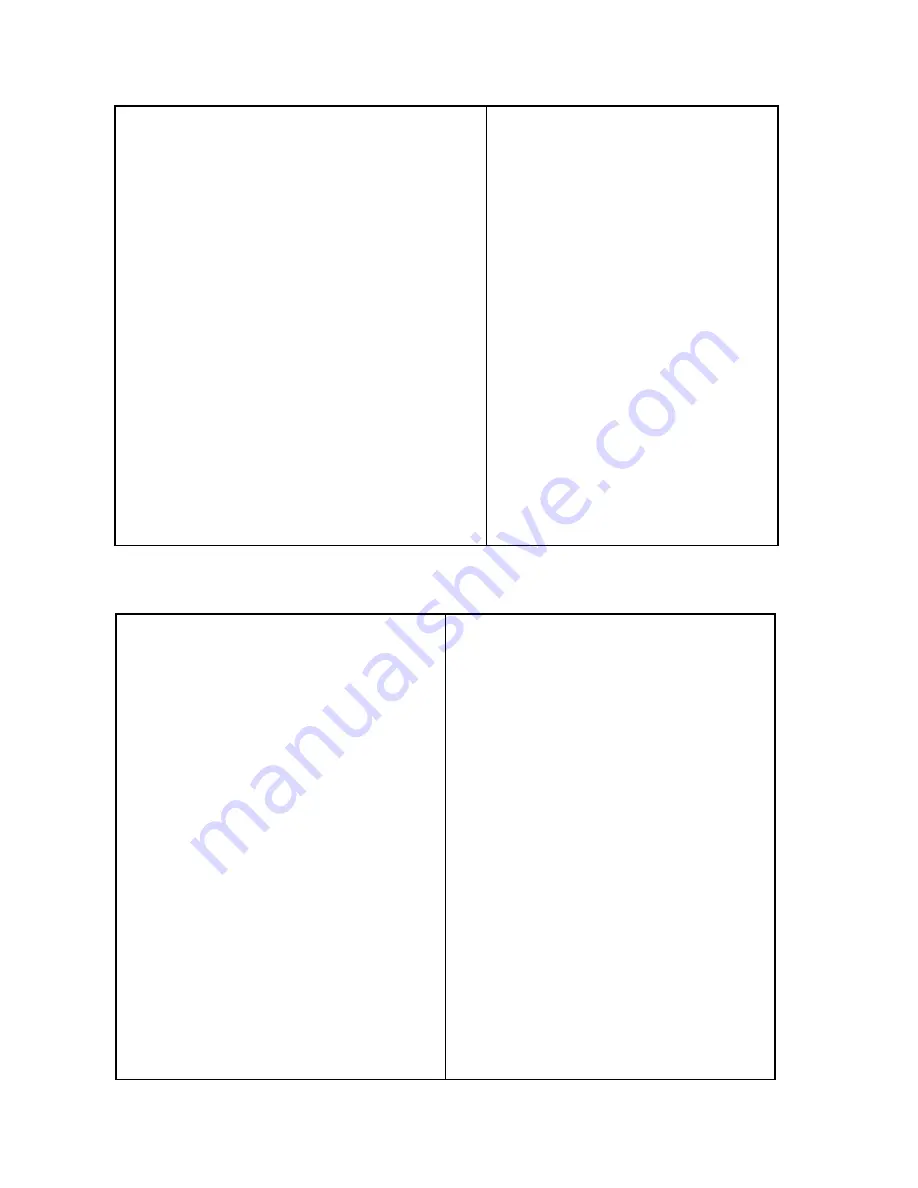
CHATTER
Snipe
De
fi
ni on
Cha er
marks
are
irregulari es
in
the
fi
nish
quality
of
the
surface
of
the
wood.
They
can
be
evenly
spaced
or
ran
‐
domly
distributed.
Simply
put,
they
may
be
described
as
“hills
and
valleys”
in
the
wood
surface.
Cause
These
marks
are
caused
by
either
loosely
held
stock
or
by
an
imbalance
in
the
machine’s
mechanical
quali es
Solu ons
The
most
common
cause
of
poor
stock
fi
nish
quality
is
a
rough
running
belt.
Replace
the
belt.
Make
sure
you
are
cu ng
with
the
head
set
at
the
appropriate
height.
Keep
your
knives
sharp.
Dull
knives
cause
intermi ent
feeding.
Check
the
pulleys
for
damage
or
imbalance.
Check
to
see
that
both
knives
and
all
a ach
‐
ing
bolts
are
of
the
same
weight.
De
fi
ni on
Snipe
is
generally
an
unwanted
undercut
in
the
stock.
It
occurs
in
the
fi
rst
and
last
few
inches
of
the
stock
length.
It
causes
a
di
ff
erent
height
di
‐
mension
than
what
was
selected
for
the
stock.
Causes
The
stock
may
be
cupped,
warped
or
twisted.
The
stock
experiences
a
change
in
down
pressure
as
the
out
feed
roller
engages
the
stock,
and
when
the
stock
disengages
with
the
in
feed
roller.
The
stock
may
enter
or
exit
the
machine
on
an
angle
because
it
is
either
being
fed
from
a
higher
or
lower
plane
than
the
bed,
or
it
is
exi ng
to
a
higher
or
lower
plane.
Solu ons
Use
a
jointer
to
fl
a en
cupped,
warped,
or
twisted
stock.
Bu
stock
pieces
ght
end
to
end.
Put
a
slight
upward
pressure
on
the
exposed
end
of
the
stock
during
both
the
in
feed
and
out
feed
stroke.
Use
slightly
longer
stock
length
than
needed
and
cut
the
snipe
o
ff
.
Make
sure
the
head
locking
handle
is
ght.
Your
outboard
support
should
be
slightly
higher
than
your
bed.
Summary of Contents for 206
Page 19: ...ARBOR REMOVAL VIEW...
Page 20: ...Stand exploded diagram...
Page 22: ...Notes Maintenance Records...