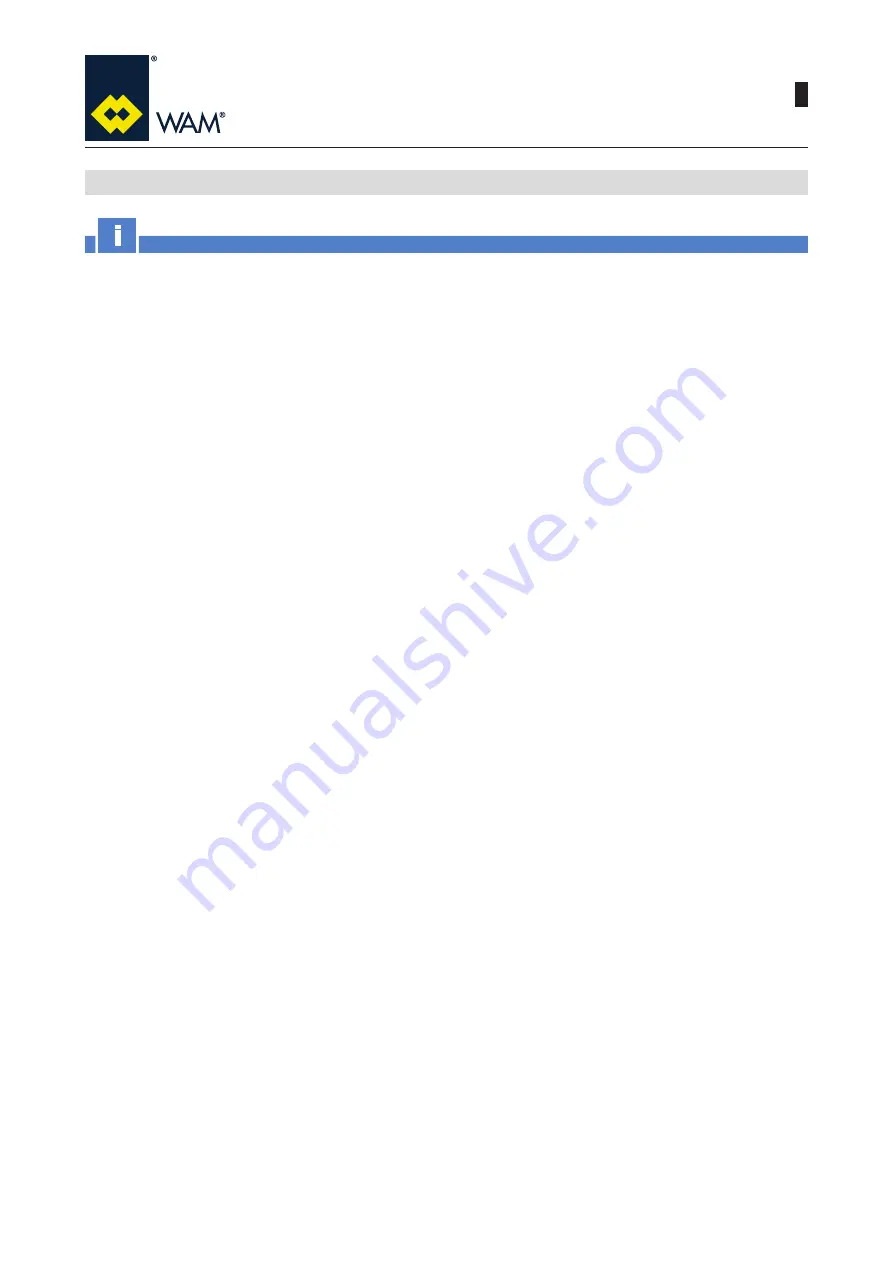
5.0 INSTALLATION AND FIXING
VCP
2
VAL.VCP.--.M.A5.1017.EN Issue: A5
10.17
31
5.10 Inspection
Important
When installation is complete, authorized personnel must carry out a general test to make sure the
safety conditions have been complied with completely.
The authorized personnel must also check:
- That no tools or other material have been left inside the valve;
- That the fixing screws have been tightened using the prescribed torque.
Before starting to operate the valve:
- Ensure that the plant in which the valve is installed complies to the Directive 2006/42/EC and the relevant
directives, the safety standards in force and those specifically applicable.
- Make sure the inlet and outlet spouts of the valve are connected to the final equipment or plant in order to
prevent access to hazardous areas.
- Ensure that the operating conditions are complied with.
- When sizing the valve, check for any chemical incompatibility between the material and the components of
the valve.
- Make sure that the food versions (model GF) were properly cleaned and sanitized.