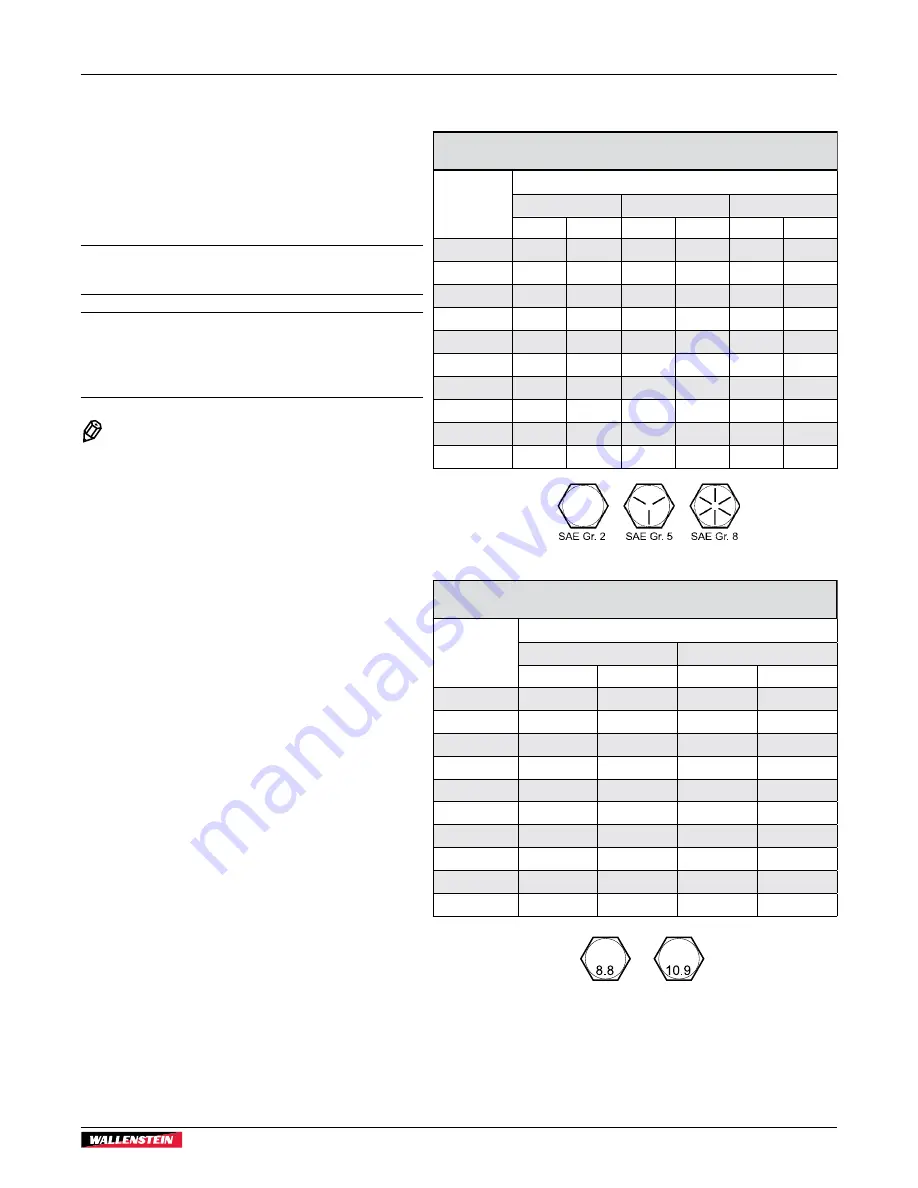
9.3 Common Bolt Torque Values
Checking Bolt Torque
The tables shown give correct torque values for various
bolts and capscrews. Tighten all bolts to the torque
values specified in the table, unless indicated otherwise.
Check tightness of bolts periodically.
IMPORTANT! If replacing hardware, use fasteners of
the same grade.
IMPORTANT! Torque figures indicated in the table are
for non-greased or non-oiled threads. Do not grease or
oil threads unless indicated otherwise. When using a
thread locker, increase torque values by 5%.
NOTE:
Bolt grades are identified by their head
markings.
Imperial Bolt Torque Specifi cations
Bolt
Diameter
Torque Value
SAE Gr� 2
SAE Gr� 5
SAE Gr� 8
lbf•ft
N•m
lbf•ft
N•m
lbf•ft
N•m
1/4"
6
8
9
12
12
17
5/16"
10
13
19
25
27
36
3/8"
20
27
33
45
45
63
7/16"
30
41
53
72
75
100
1/2"
45
61
80
110
115
155
9/16"
60
95
115
155
165
220
5/8"
95
128
160
215
220
305
3/4"
165
225
290
390
400
540
7/8"
170
230
420
570
650
880
1"
225
345
630
850
970
1320
Metric Bolt Torque Specifi cations
Bolt
Diameter
Torque Value
Gr� 8�8
Gr� 10�9
lbf•ft
N•m
lbf•ft
N•m
M3
0�4
0�5
1�3
1�8
M4
2�2
3
3�3
4�5
M6
7
10
11
15
M8
18
25
26
35
M10
37
50
52
70
M12
66
90
92
125
M14
83
112
116
158
M16
166
225
229
310
M20
321
435
450
610
M30
1,103
1 495
1,550
2 100
LXT95 / LXT115
Log Trailer & Grapple
Specifications
59
Summary of Contents for LXT115
Page 64: ...www wallensteinequipment com ...