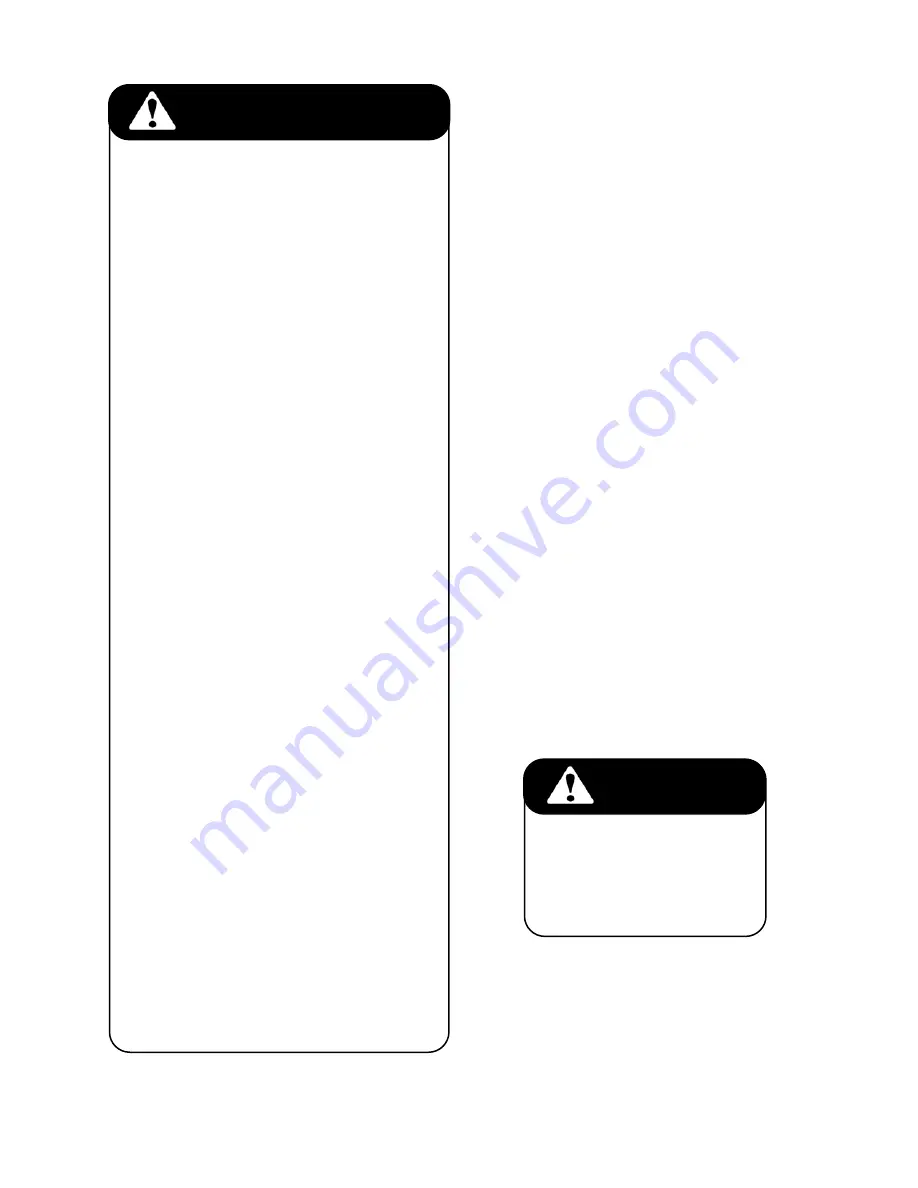
32
MAINTENANCE SAFETY
7 SERVICE AND MAINTENANCE
7�1 SERVICE
By following a careful service and maintenance
program for your machine, you will enjoy many
years or trouble-free operation.
7�1�1 FLUIDS AND LUBRICANTS
1� Grease:
Use an SAE multi-purpose high temperature grease
with extreme pressure (EP) performance. Also
acceptable is an SAE multipurpose lithium base
grease.
2� Storing Lubricants:
Your machine can operate at top efficiency only if
clean lubricants are used. Use clean containers to
handle all lubricants. Store them in an area pro
-
tected from dust, moisture and other contaminants.
7�1�2 GREASING
Use the Maintenance Checklist provided to keep a
record of all scheduled maintenance.
1.
Use a hand-held grease gun for all greasing.
2.
Wipe grease fitting with a clean cloth before
greasing, to avoid injecting dirt and grit.
3.
Replace and repair broken fittings immediately.
4.
If fittings will not take grease, remove and clean
thoroughly. Also clean lubricant passageway.
Replace fittings if necessary.
7�1�3 SERVICING INTERVALS
See service record and service illustration for service
interval information. The period recommended
is based on normal operating conditions. Severe
or unusual conditions may require more frequent
lubrication or oil changes.
IMPORTANT
Do Not over grease.
• Good maintenance is your responsibility.
Poor maintenance is an invitation to trouble.
• Follow good shop practices.
-
Keep service area clean and dry.
-
Be sure electrical outlets and tools are
properly grounded.
-
Use adequate light for the job at hand.
• Make sure there is plenty of ventilation. Never
operate the engine in a closed building. The
exhaust fumes may cause asphyxiation.
• Before working on this machine, place the
machine in safe mode:
• disengage the PTO
•
shut off the engine
• ensure all components have stopped
moving
• remove and pocket the ignition key
• block & chock the tractor wheels
• and set rotor lock if required�
• Never work under equipment unless it is
blocked securely.
• Always use personal protection devices
such as eye, hand and hearing protectors,
when performing any service or maintenance
work. Use heavy gloves when handling sharp
components.
• Where replacement parts are necessary
for periodic maintenance and servicing,
genuine factory replacement parts must be
used to restore your equipment to original
specifications. The manufacturer will not be
responsible for injuries or damages caused by
use of unapproved parts and/or accessories.
• A fire extinguisher and first aid kit should
be kept readily accessible while performing
maintenance on this equipment.
• Periodically tighten all bolts, nuts and
screws and check that all electrical and fuel
connections are properly secured to ensure
unit is in a safe condition.
• When completing a maintenance or service
function, make sure all safety shields and
devices are installed before placing unit in
service.
WARNING
Machine is shown with guard
removed or rotor cover opened
for illustrative purposes only�
Do not operate machine with
guard removed or cover
opened�