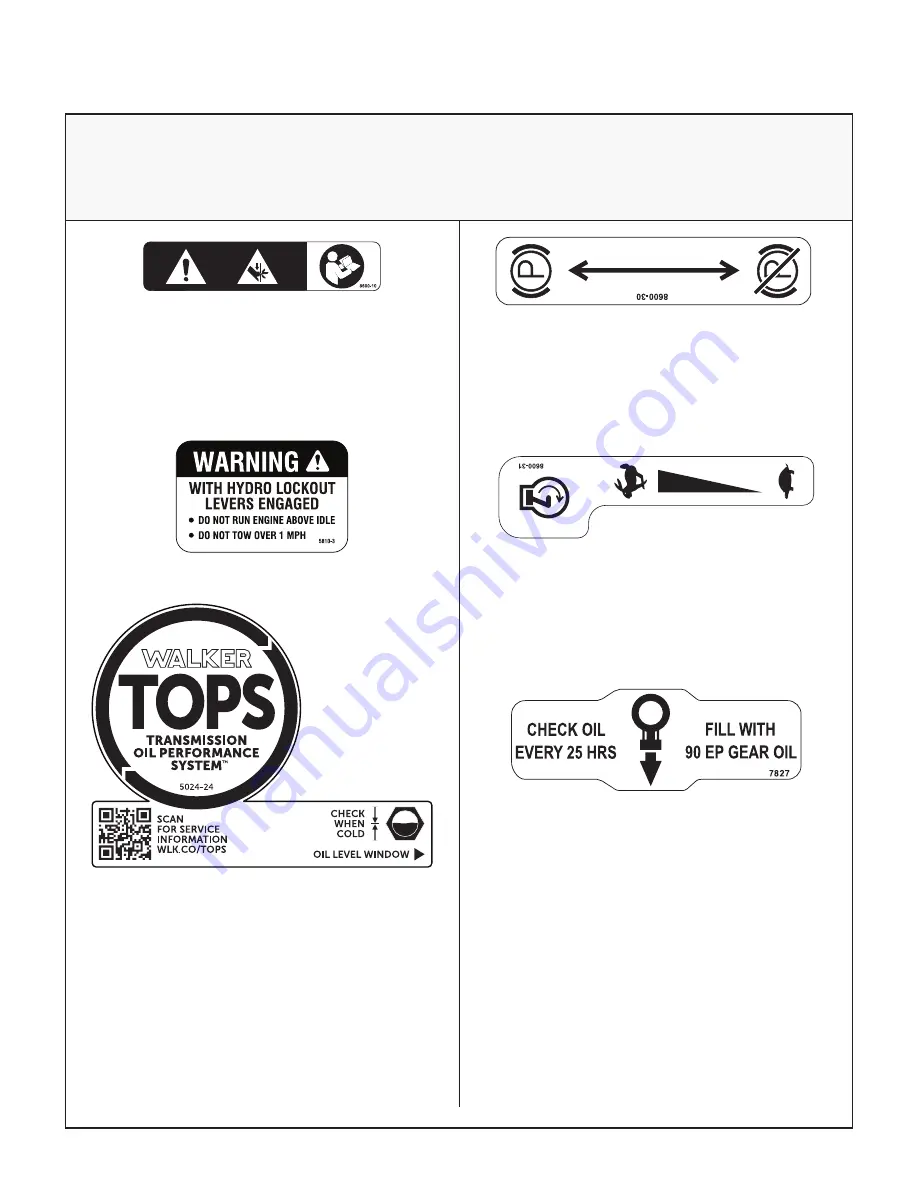
T27i
Safety Instructions
17
SAFETY, CONTROL, AND INSTRUCTION DECALS
Safety, Control, and Instruction Decals are installed on the machine;
if any are missing, illegible, or damaged, a replacement should be ordered and installed before
putting the machine into operation. The Decal Part Number is listed below and in the Parts Manual.
Location: Catcher Door Hinge Bar,
LH and RH Sides
Part Number: 8600-10
Caution - Pinch point.
● Keep all body parts clear when closing grass
catcher door.
Location: LH Gear Axle
Part Number: 5810-3
Location: Oil Reservoir
Part Number: 5024-24
Location: Front Body, RH Side Adjacent to
Operator Seat
Part Number: 8600-30
Parking Brake
● Move lever forward to engage Parking
Brake; back to disengage.
Location: Front Body, LH Side Adjacent to
Operator Seat
Part Number: 8600-31
Throttle
● Move lever forward to increase engine speed;
back to idle.
Location: Jackshaft Support Adjacent
to Dipstick
Part Number: 7827