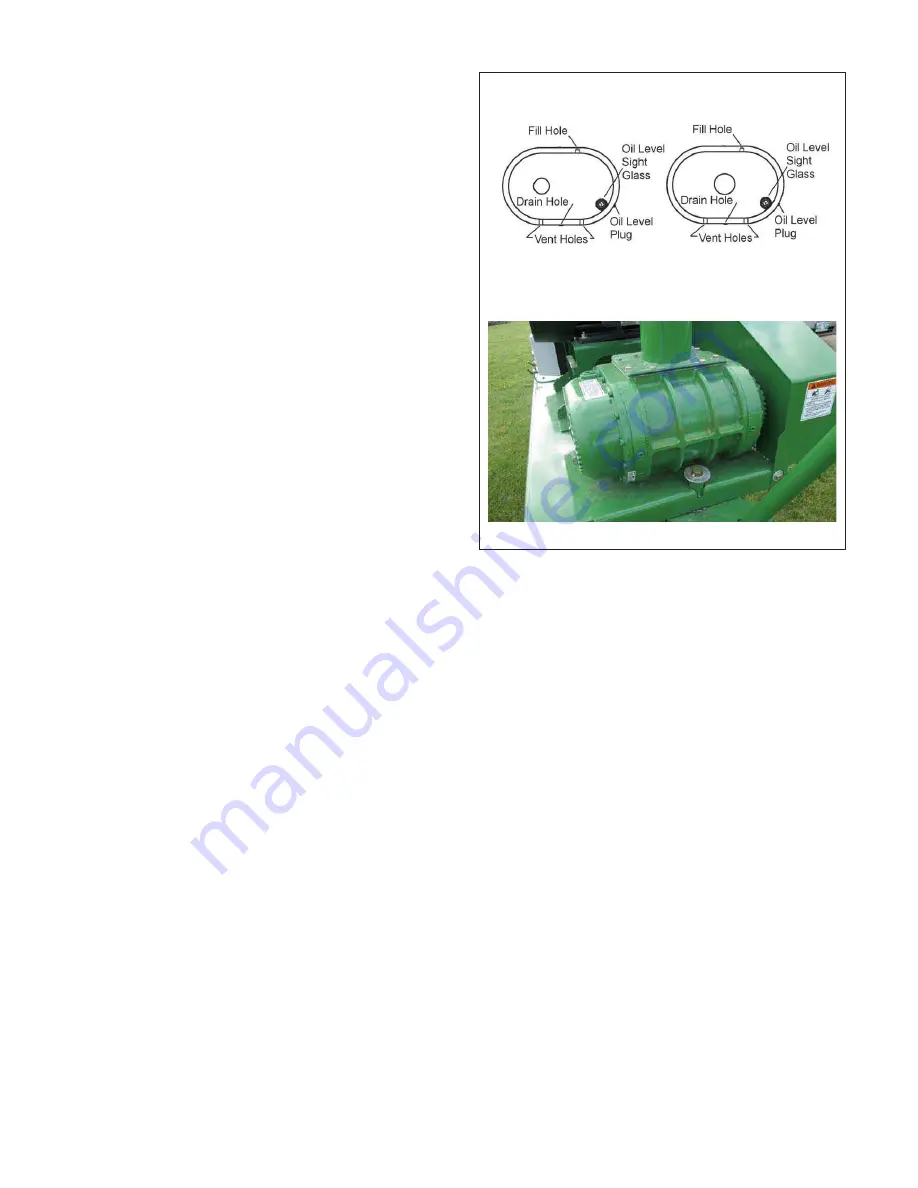
45
FIG. 32 BLOWER
Schematic
Blower (Typical)
5.
Changing Oil:
a.
Place a collection pan or pail under each drain
plug.
b.
Remove each drain plug.
c.
Flush each case and allow several minutes to
drain.
d. Dispose of the oil in an approved manner. Do
not contaminate the worksite with used oil.
e.
Install and tighten the drain plugs.
f.
Remove fill and level plug.
g.
Add Walinga
®
Blower oil or equivalent to each
reservoir until the oil is just starting to come
out of the level plug hole or half way in sight
glass.
IMPORTANT
Condensation forms and collects inside
the reservoirs during machine operation.
Changing oil removes this water and
prevents it from damaging the gears
and bearings.
h. Install and tighten the level and fill plugs.
i.
Install and secure the belt/chain drive covers.
6.
Cleaning Breathers:
a.
Remove breathers and blow out with an air
hose.
b.
If dirt has caked up in the breather, soak in
good solvent and then blow out. It may be
necessary to use a probe to loosen the dirt.
c.
Install and tighten the breather.
e.
Install and secure the belt drive covers.
f.
Clean vents in end plates located under the
blower on either side of the drain plug.
Summary of Contents for Agri-Vac 3510
Page 2: ......
Page 4: ......
Page 9: ...NOTES...
Page 22: ...NOTES...
Page 45: ...35 FIG 22 STEERING WHEEL BUSHING 5 Grease steering wheel bushing...
Page 58: ...NOTES...
Page 62: ...NOTES...
Page 66: ...57 NOTES...
Page 67: ...57 NOTES...
Page 69: ......