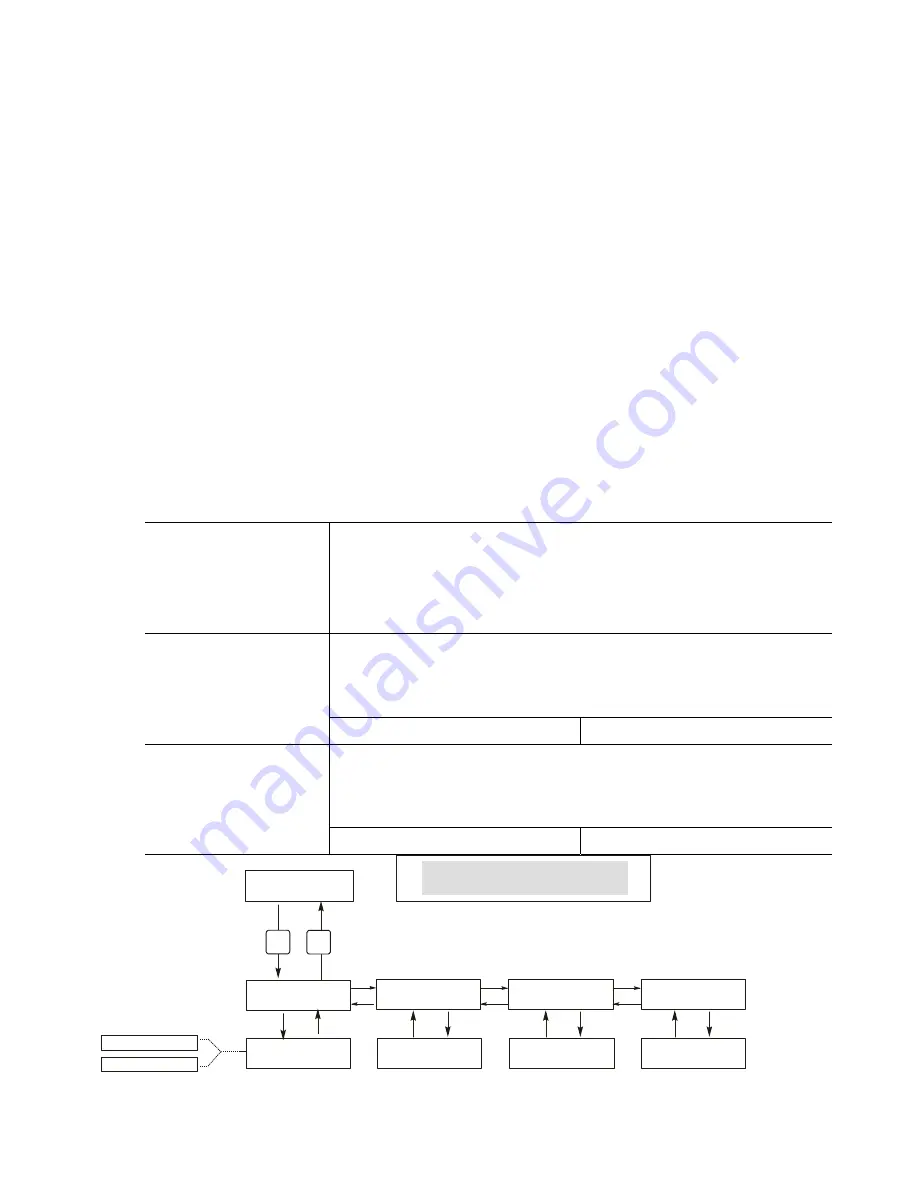
5.11 Datalog
Menu
This menu is available if the data logging option has been purchased. This is indicated in the model
code by the letter U at the end of the model code. This menu allows you to save data from the controller
to a USB flash drive.
The controller has four logs, the Current Datalog, the Backup Datalog, the Event Log, and the Reset
Log. All files are in a CSV format that may be opened in a spreadsheet such as Microsoft Excel.
Current Datalog
Contains the following data taken at 10 minute intervals for each tower:
Conductivity
Temperature
Water
Meter
Total
When the current datalog is downloaded to a USB stick, it is erased and a new log file is started.
If the current datalog is not downloaded before it reaches its maximum size (at least 60 days of
data) the oldest data is overwritten by the newest data.
Backup Datalog
Contains the same data as the current log but it is never erased. When the backup log reaches its
maximum size (at least 60 days of data), the oldest data is overwritten by the newest data.
Event Log
Contains columns for each relay and flow switch input, as well as the date and time. Each time
any of these change state, the date and time is updated and it will show a 1 if the relay is on and 0
if it is off, and a 1 if the flow switch indicates no flow, 0 if there is flow. Tens of thousands of
events will be recorded before the oldest data is overwritten by the newest, the number varying
with the controller’s configuration.
Reset Log
Consists of time stamps of when power was lost, when it was returned, and the cause of the reset.
Current or Backup
Datalog
Place a USB flash drive with at least 10 MB capacity into the USB port on the front panel of the
controller. Press the Enter key to download the file from the controller to the disk. The file name for
the Current Datalog will be Datalog<serial number><date><time>.csv using the date and time it was
downloaded. The file name for the Backup Datalog will be Datalog<serial number><date><time>
.csv using the date and time it was created.
The controller will display the progress of the file download process. If the file was successfully
copied to the USB disk the controller will display Transfer Success.
Copy Event Log
Place a USB flash drive with at least 10 MB capacity into the USB port on the front panel of the
controller. Press the Enter key to download the file from the controller to the stick. The file name
will be Eventlog<serial number><date><time>.csv.
The controller will display the progress of the file download process. If the file was successfully
copied to the USB disk the controller will display Transfer Success, otherwise Transfer Fail 1.
Transfer Success
Transfer Fail 1
Copy Reset Log
Place a USB flash drive with at least 10 MB capacity into the USB port on the front panel of the
controller. Press the Enter key to download the file from the controller to the stick. The file name
will be Resetlog<serial number><date><time>.csv.
The controller will display the progress of the file download process. If the file was successfully
copied to the USB disk the controller will display Transfer Success.
Transfer Success
Transfer Fail 1
Datalog
Current Datalog
Datalog
Copy Event Log
Datalog Menu
ENTER
EXIT
67° F
Datalog
2000 µS
Datalog
Transfer Success
Next
Prev
Datalog
Copy Reset Log
Next
Prev
ENTER
EXIT
ENTER
EXIT
ENTER
EXIT
Datalog
Transfer Success
Datalog
Transfer Success
Possible Status Screens
Transfer Success
Transfer Fail 1
Datalog
Backup DataLog
Next
Prev
ENTER
EXIT
Datalog
Transfer Success
Figure 17 Datalog Menu
25