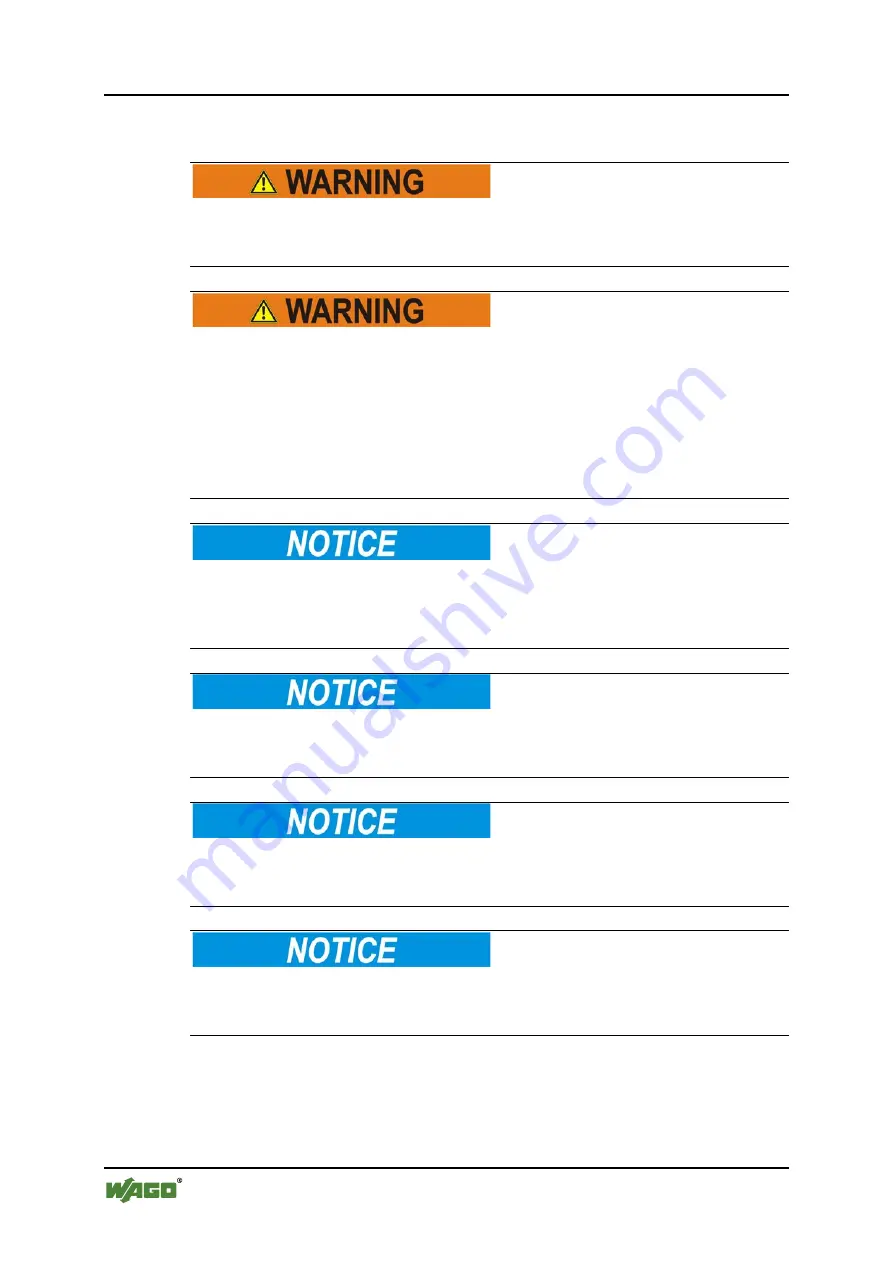
36
Using Interference-Free Variants of I/O Modules in Safety Related ApplicationsWAGO-I/O-SYSTEM 750
753-501 2DO 24V DC 0,5A
Manual
Version 1.2.0
1
Einsatz der rückwir kungsfrei en Digital ausg angskl emme in Sicher heitsanwendungen
7.1
Important Notes
Use PELV supply only!
Only a power supply unit with protective extra-low voltage (PELV) shall be used
for the 24 V power supply.
Note maximum voltage!
Please note that a maximum voltage U
max
only can act on the reaction-free I/O
module in the event of a failure because irreparable damage could occur to the
module otherwise.
For the reaction-free I/O module , the field supply voltage is:
U
max
< 32 V
Note IP54 protection class!
IP54 protection class is absolutely mandatory. This means that the interference-
free digital output module shall only be integrated and operated in switch boxes or
switch cabinets complying with IP54 or higher.
Avoid reverse supply of output!
The 24 V power supply shall never be applied to the output of an interference-free
digital output module. This wiring failure will not be detected by the system.
Avoid reverse supply of module!
A group of interference-free digital output modules shall only be supplied using a
safety switching device. Reverse supply must absolutely be avoided.
Avoid short circuits between outputs!
Short circuits between outputs of different interference-free digital output
modules must absolutely be avoided as they are not detected by the system.
According to EN ISO 13849-2, the following measures are required for an
“external voltage” fault exclusion:
-
Use of cables routed separately and
-
Protection from external damage (e.g., caused by cable duct).