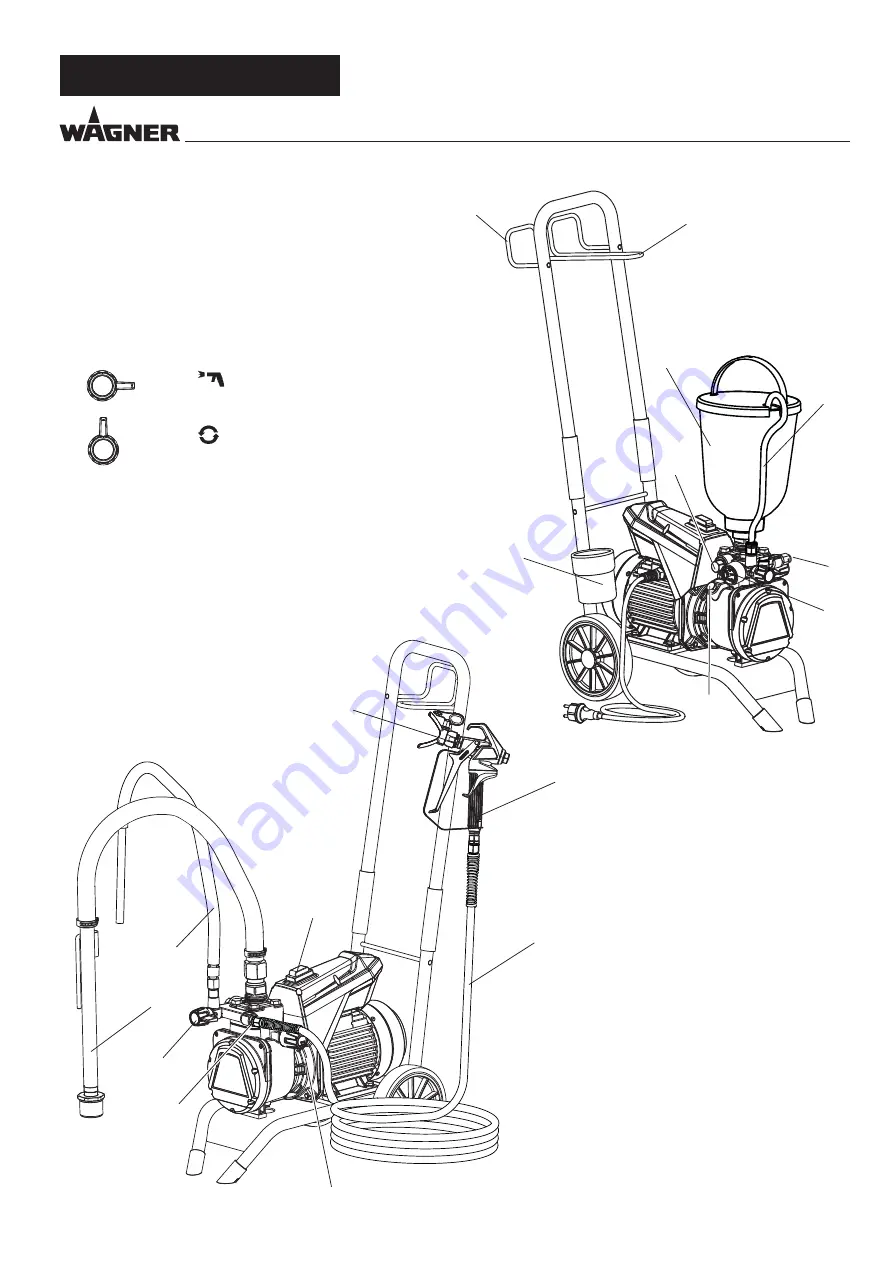
41
Super Finish 23 Pro
6
1
2
3
7
9
10
8
4
5
12
9
14
11
4
15
16
13
GB
DESCRIPTION OF UNIT
3.3
EXPLANATORY DIAGRAM
1 Tip guard with airless tip*
2 Spray gun*
3 High-pressure hose*
4 Connection for high-pressure hose
5 Pressure gauge*
6 Pressure control valve
7 ON / OFF switch
8 Pressure relief valve
=
Spraying
=
Circulation
9 Return hose*
10 Suction hose*
11 Hopper*
12 Outlet valve
13 Oil dipstick
14 Cleaning Container
15 Hose bracket
16 Gun holder
17 Tool bag (no fig.)
*Accessory. The actual scope of the delivery
depends on how the Spray Pack is configured.