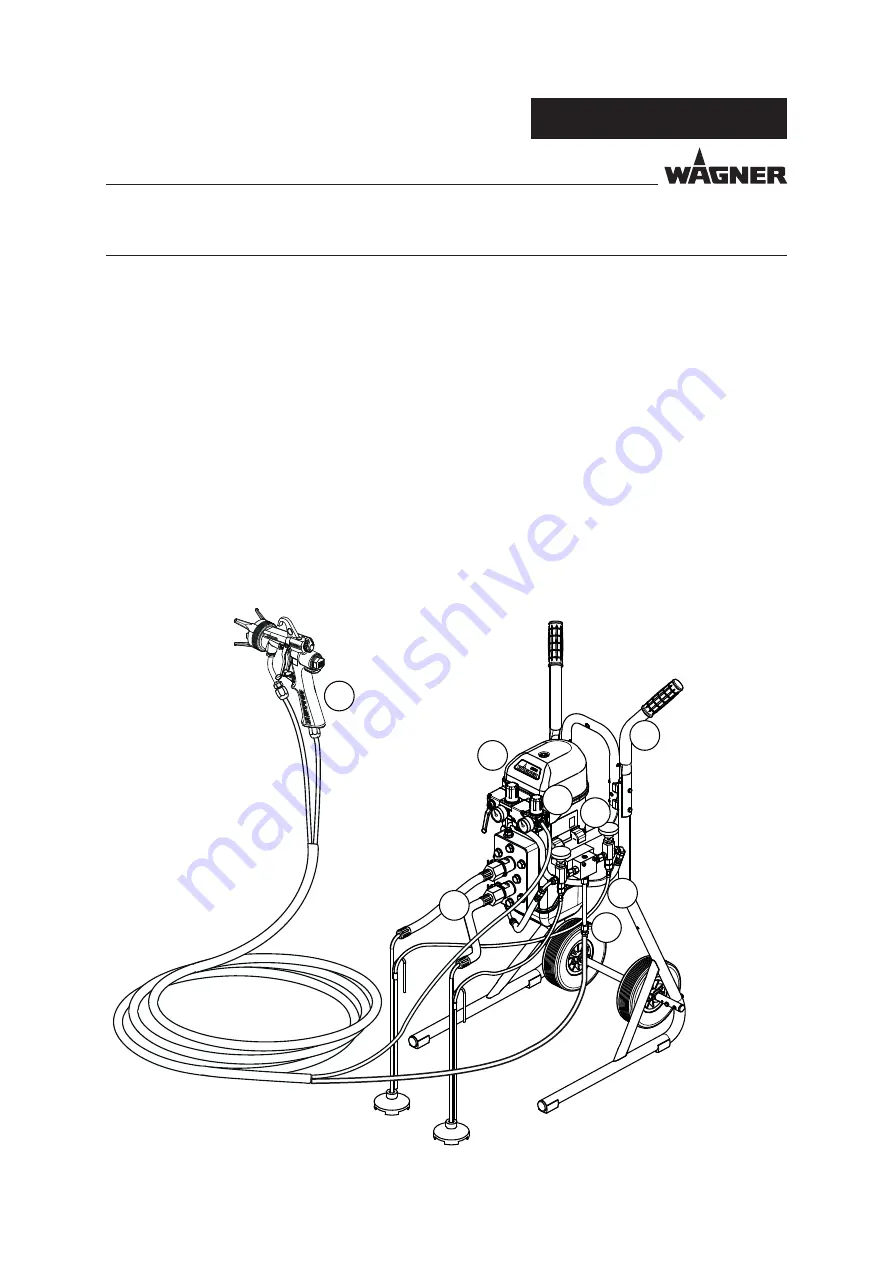
21
Cobra 40-10/2K
.
B_03123
1
2
3
4
5
6
7
8
OPERATING MANUAL
EDITION 10/2010
PART NO. DOC322871
5
STARTING WORK AND HANDLING
5.1
INSTALLATION AND CONNECTION
5.1.1
SETTING UP THE PUMP
Note
This pump can be used as part of a spraying system for Airless or AirCoat applications.
The components can be found in the accessories list, provided that the system was not
obtained as a spraypack.
The nozzles must be selected according to the gun instructions.
Procedure:
1. Install pump (1) on trolley (6) or wall mounting.
2. For AirCoat system (see fi gure below): fi t the additional fi lter pressure regulator (7)
(optional).
3. Mounting suction systems (5).
4. Connect return hoses (4) of the suction system to return valves (3).
5. Connect the high-pressure hose of the gun (2) to statics mixers (8) and when using the
AirCoat process connect air hose to fi lter pressure regulator (7).