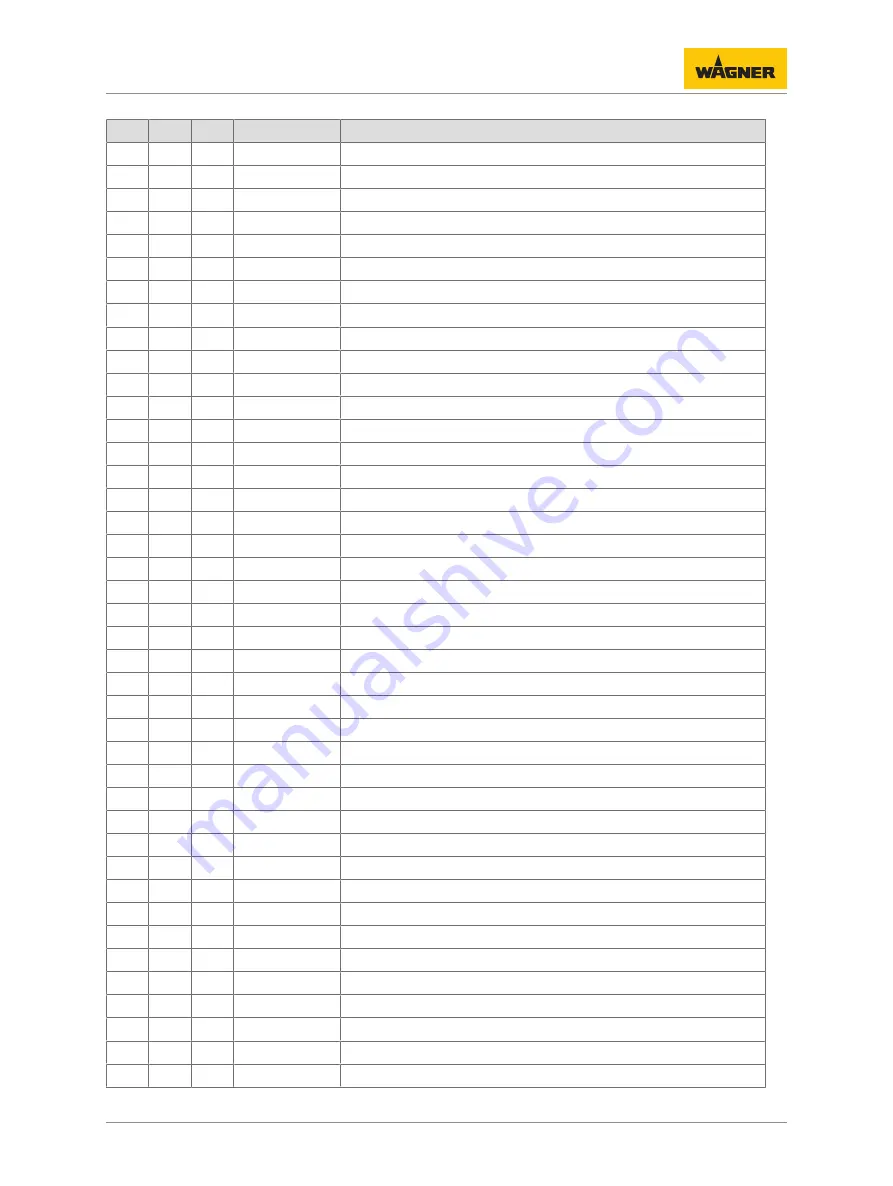
Operating manual High-pressure double diaphragm pumps Cobra 40-10; Cobra 40-25
14 Spare Parts
68
Order number 2340851 | Edition 05/2022
Pos
K
Stk
Order no.
Designation
8
1
367318
Shoulder screw 4
9
1
9925033
Washer
10
1
367310
Silencer 4
11
♦
⋆
1
9974098
O-ring
12
♦
⋆
1
9974097
O-ring
13
3
9900325
Socket cap screw
14
3
9920103
Washer, A6.4
15
1
367309
Connecting part 4
16
2
367320
Cotter pin
17
♦
1
369290
Pilot valve
18
2
9998674
Threaded plug
19
1
9998274
Threaded plug
20
1
2359165
Control housing 4
21
♦
⋆
1
367313
Compressed air filter 4/6
22
1
2328606
Cobra pressure regulator unit, complete
24
1
9990506
Cone plug, GPN 600
25
1
9999228
Fitting L
26
2
367307
Sealing plug 4/6
27
♦
⋆
2
9974085
O-ring
28
1
367324
Filter holder
29
♦
⋆
1
367314
Control air filter
30
♦
⋆
1
322910
Cobra outlet seal set (consisting of 2 seals)
31
♦
⋆
2
9974095
O-ring
32
1
368285
Safety valve 0.63 MPa; 6.3 bar; 91 psi
33
♦
1
9943080
Spool and sleeve assembly, complete
34
♦
1
368038
Detent body, complete, ISO 1/2
35
2
9907126
Screw SFS Plastite 45
36
♦
⋆
2
9974089
O-ring
37
♦
⋆
2
9974115
O-ring
38
1
322432
Control air pipe
39
1
322430
Cylinder pipe
40
1
322431
Compressed air pipe
41
♦
⋆
2
9971448
O-ring
42
♦
1
2360756
Angled ball valve 4, complete
43
♦
⋆
1
9971137
O-ring
44
4
9900316
Hexagon socket head cap screw, M6x50
45
2
9907039
Hexagon socket head cap screw, M6x80
46
♦
⋆
1
9971313
O-ring
47
♦
1
2341175
Pressure gauge with air regulator 0-10 bar, G1/8"
48
♦
1
2309972
Pressure regulator
49
1
2309744
Distributor piece LR-D-I Mini 4