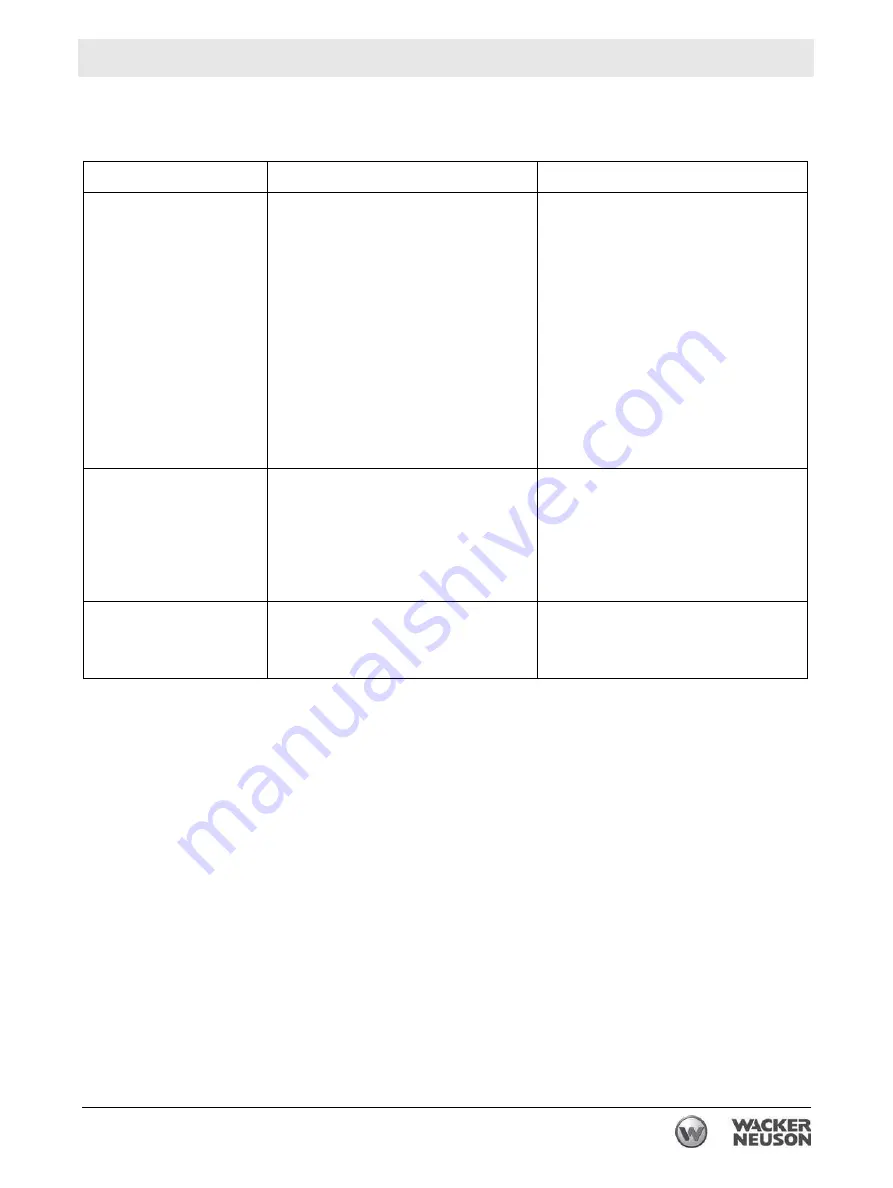
wpm_tx004453gb.fm
32
6
Troubleshooting
Problem
Cause
Remedy
Plate does not
develop full speed.
Poor compaction.
• Engine throttle control not
completely open.
• Throttle control not adjusted
correctly.
• Ground too wet, plate sticking.
• Drive belt loose or worn, slip-
ping on pulleys.
• Exciter bearings binding.
• Air filter clogged with dust,
reducing engine performance.
• Engine speed is too low.
• Allow soil to dry before
compacting.
• Adjust or replace belt.
• Check that engine mounting
bolts are tight.
• Check condition and level of oil
in exciter.
• Check engine speed with
tachometer.
• Adjust or repair engine to run
correctly speed. Refer to
engine manual.
Engine running, no
vibration.
• Engine throttle not open.
• Drive belt loose or broken.
• Clutch damaged.
• Engine speed is too low.
• Too much oil in exciter
• Adjust or replace the drive belt.
• Inspect and replace the clutch.
• Check engine speed.
• Adjust oit to correct level.
Plate jumps or
compacts unevenly.
• Ground surface too hard.
• Shockmounts loose or
damaged
• Inspect and replace the
shockmounts.
VP1030A/AW
Troubleshooting
Summary of Contents for VP1030A-CE
Page 1: ...Operator s Manual Vibroplate VP1030A CE VP1030AW CE EN 5000401966 10 1119 5 0 0 0 4 0 1 9 6 6...
Page 14: ...wpm_si001047_01gb fm 14 2 Labels 2 1 Label Locations wpm_gr013776 VP1030A AW Labels...
Page 35: ...wpm_td000708gb fm 35 8 Dimensions wpm_gr005975 VP1030A AW Dimensions 300 12 914 36 889 35...
Page 36: ......
Page 37: ......
Page 38: ......