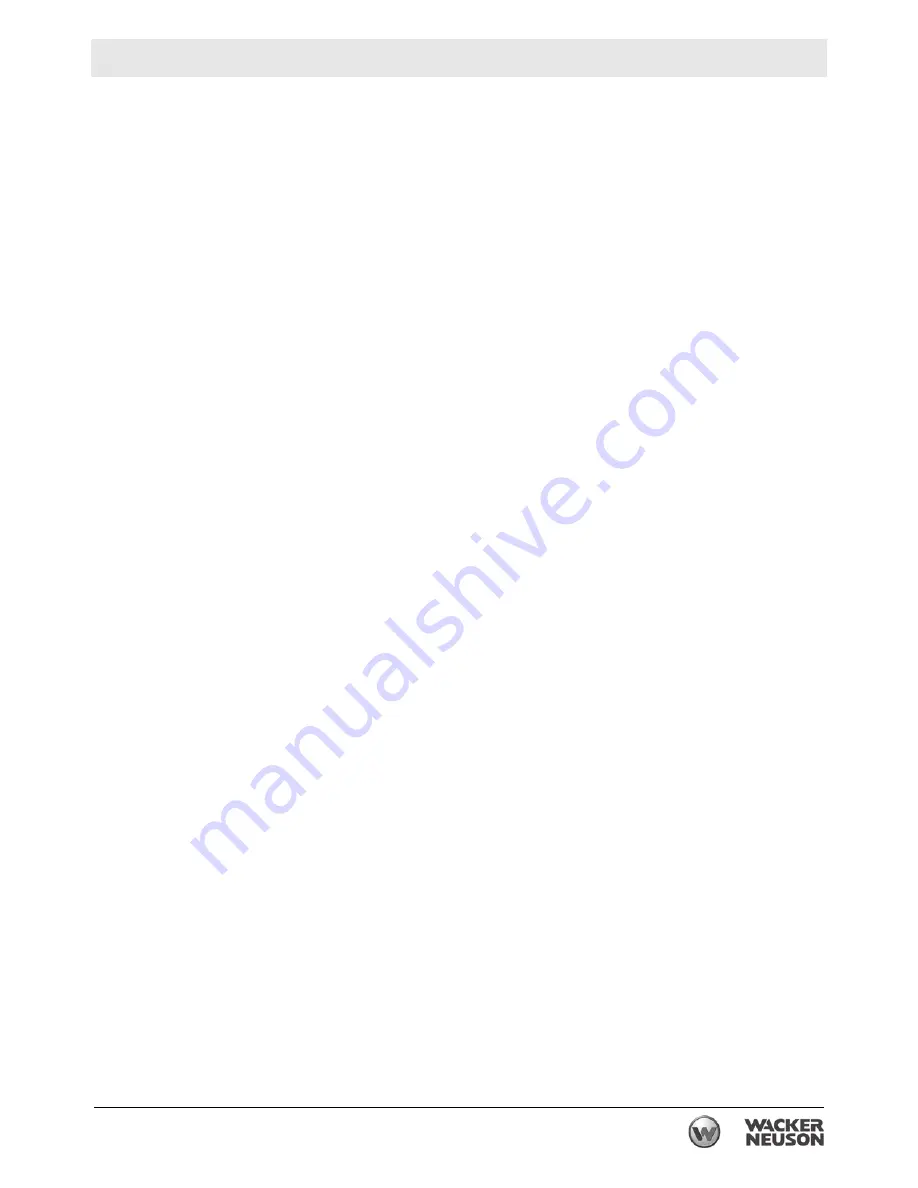
RD 12A
Operation
wc_tx001071gb.fm
43
4.21 Parking Brake
See Graphic: wc_gr002953
To hold the machine in a stopped position (parked), there is a
mechanical parking brake on the rear drive motor. The engine will
automatically shut off when the operator leaves the seat, but the
parking brake must be set manually.
To set the parking brake
(42)
, pull the brake lever up until the brake
pad engages the rear drum. Always set the parking brake before
leaving the machine. To release the parking brake, lower the brake
lever. The forward/reverse control
(15)
should be in the NEUTRAL
position when the parking brake is released.
The parking brake is connected to the brake pads and can be adjusted
by turning the knob on the end of the handle. See section
Parking
Brake Adjustment
.
NOTICE
:
Under normal operating conditions, do not use the parking
brake when the machine is moving. The parking brake should only be
used in cases of
emergency
when the machine is moving, e.g.,
following failure of the main hydraulic braking system (moving the
forward/reverse control to the NEUTRAL position) or in a runaway
condition traveling down a slope. Using the parking brake while the
machine is moving may cause damage to the drive motor.
Summary of Contents for RD 12A
Page 1: ...0182863en 001 0610 0 1 8 2 8 6 3 E N Operator s Manual Roller RD 12A...
Page 8: ...Table of Contents RD 12A 8 wc_bo0182863en_001TOC fm...
Page 16: ...Labels RD 12A 16 wc_si000302gb fm 2 Labels 2 1 Label Locations X FF GG GG...
Page 23: ...RD 12A Lifting and Transporting wc_tx001556gb fm 23 Notes...
Page 40: ...Operation RD 12A 40 wc_tx001071gb fm wc_gr002951 N F R 55 42 44 54 10 15...
Page 74: ...Schematics RD 12A 74 Notes...
Page 104: ...KE40246P1 6 9 05 3 14 PM Page 1...
Page 105: ......