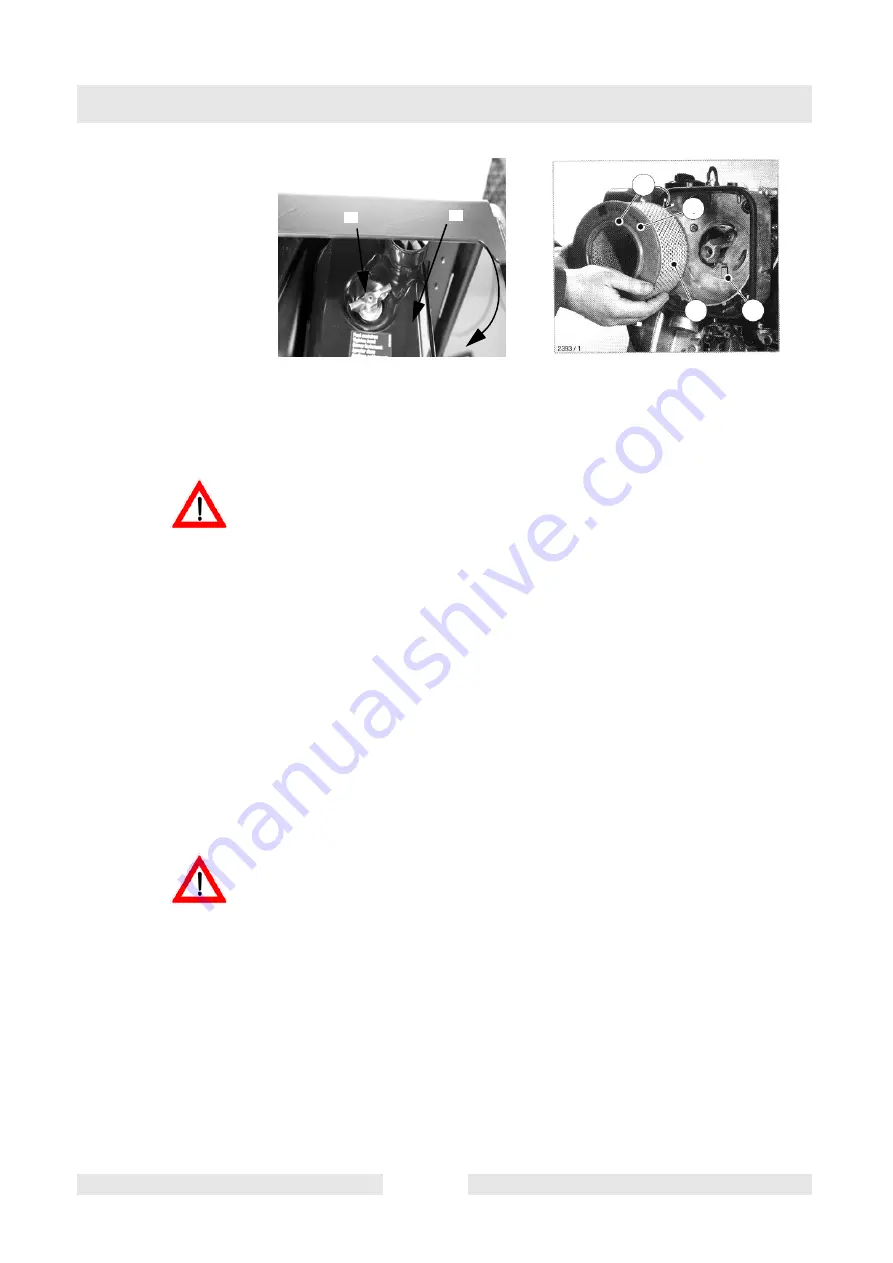
Maintenance
T01007GB.fm
44
4. Knock the dry dirt out of the filter element.
Do not clean the filter element with compressed air to avoid causing
damages.
Note: Check the filter insert for cracks or other damages while
holding it against a light or when illuminating it with a lamp.
Do not reuse the filter element if you have determine any kind of
damages in the area of the filtering paper (s) or, as the case may
be, in the area of the sealing lip (t).
5. Replace the filter element if the maintenance plan requires it.
6. Follow the disassembly procedure in reverse order to refit the filter.
Caution
Operating the engine without air cleaner can cause rapid engine wear.
∗
Do not run the engine without an air cleaner.
p
o
r
s
t
u
Summary of Contents for DPU 6555He
Page 1: ...Operator s Manual Vibratory plate DPU 6555He 0226268en 002 03 2010...
Page 54: ...Faults T01008GB fm 54...
Page 56: ...3 Disposal 56...
Page 58: ......
Page 59: ......
Page 60: ......