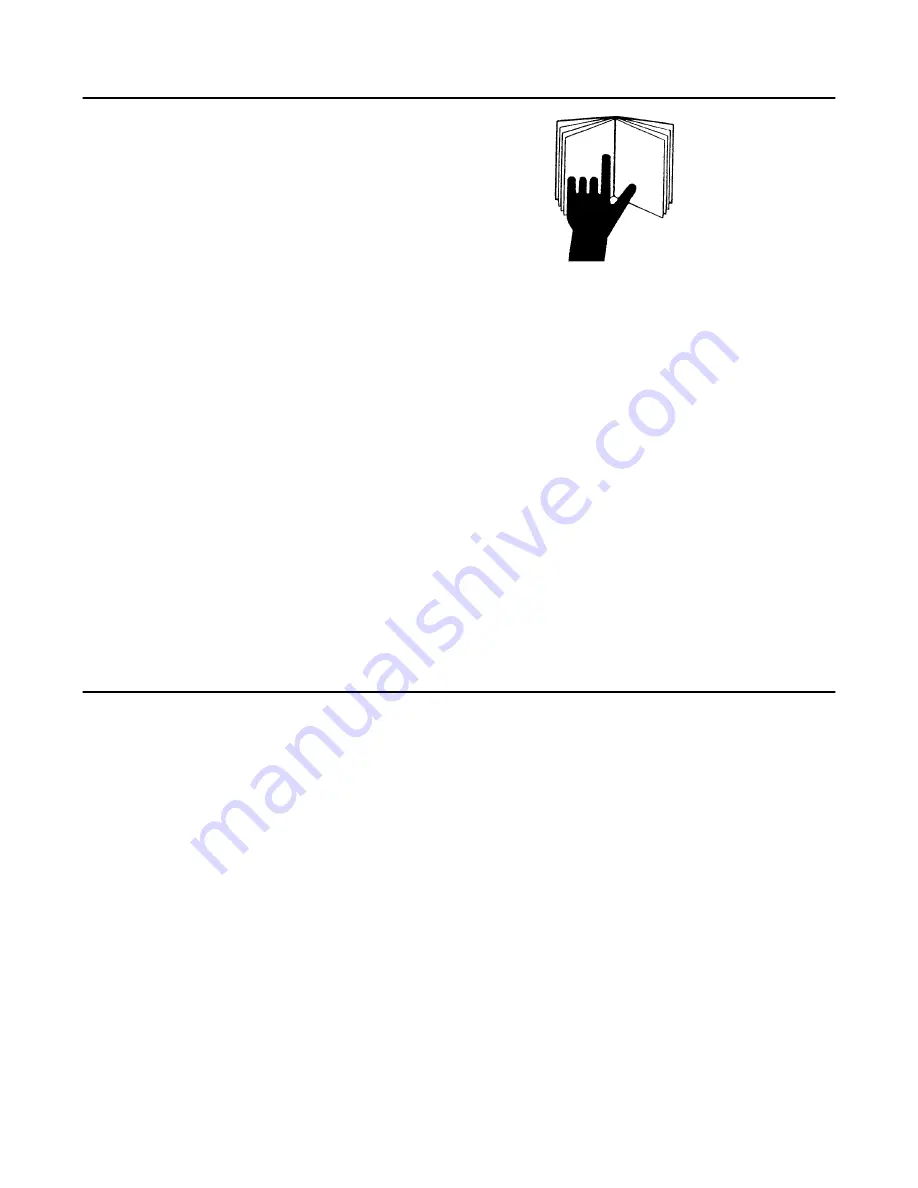
SHUT DOWN PROCEDURES
Never disable or disconnect the safety devices!
Always close fuel valves when the machine is not
being used.
Refer to the manufacturer’s manuals for specific
shut down procedures.
15
SHUT DOWN SAFELY
Trowel.qxd 11/24/04 10:18 AM Page 15
PRECAUTIONS
• Power trowels are heavy and awkward to move
around.
• Do not attempt to lift the ride-on trowel by the
guard rings.
• Use proper heavy lifting procedures.
• Keep all non-essential personnel clear of the
area.
• Never hoist the trowel over areas where people
are standing or working.
• Remove tools and loose items before lifting.
• Make sure the crossbars on the safety catches
are in good condition if so equipped.
• Always consult your operator’s manual for the
best and proper lifting, loading, and unloading
methods.
WALK-BEHIND TROWELS
Some walk-behind trowels can be lifted or moved
by two people utilizing lifting tubes or other special
attachments. Generally however, they must be
lifted using lifting bales (special lifting brackets), or
other specific lifting points provided by the
manufacturer, and cranes, hoists, or forklifts. Be
certain any lifting devices used have adequate
capacity.
RIDE-ON TROWELS
Ride-on trowels are very heavy. They require
heavy-duty lifting devices such as cranes or heavy-
duty hoists to lift them on and off the concrete slab.
Be certain any lifting devices used have adequate
capacity. Some ride-on trowels are equipped with
lifting bosses that are used with specialized
apparatus to assist in moving the trowels around.
Use extreme care when lifting or moving a ride-on
trowel.
STORAGE
Always store equipment properly when it is not
being used. Equipment should be stored in a clean,
dry location out of reach of children.
LOAD AND UNLOAD SAFELY
16
Trowel.qxd 11/24/04 10:18 AM Page 16
Summary of Contents for CRT 36-25
Page 1: ...5200001020 03 0515 5 2 0 0 0 0 1 0 2 0 Operator s Manual Ride On Trowel CRT 36 25 CRT 36 26A...
Page 6: ......
Page 15: ...CRT 36 Labels wc_si000378gb fm 15 2 Labels 2 1 Label Locations C D B J...
Page 16: ...Labels CRT 36 16 wc_si000378gb fm...
Page 21: ...wc_tx000639gb fm 21 CRT 36 Operation 3 Operation 3 1 Features and Controls...
Page 51: ...wc_tx001324gb fm 51 CRT 36 Schematics 7 Schematics...
Page 53: ......
Page 66: ...AEM_ConcretePowerTrowel qxd 7 23 03 6 31 AM Page 1...
Page 67: ......