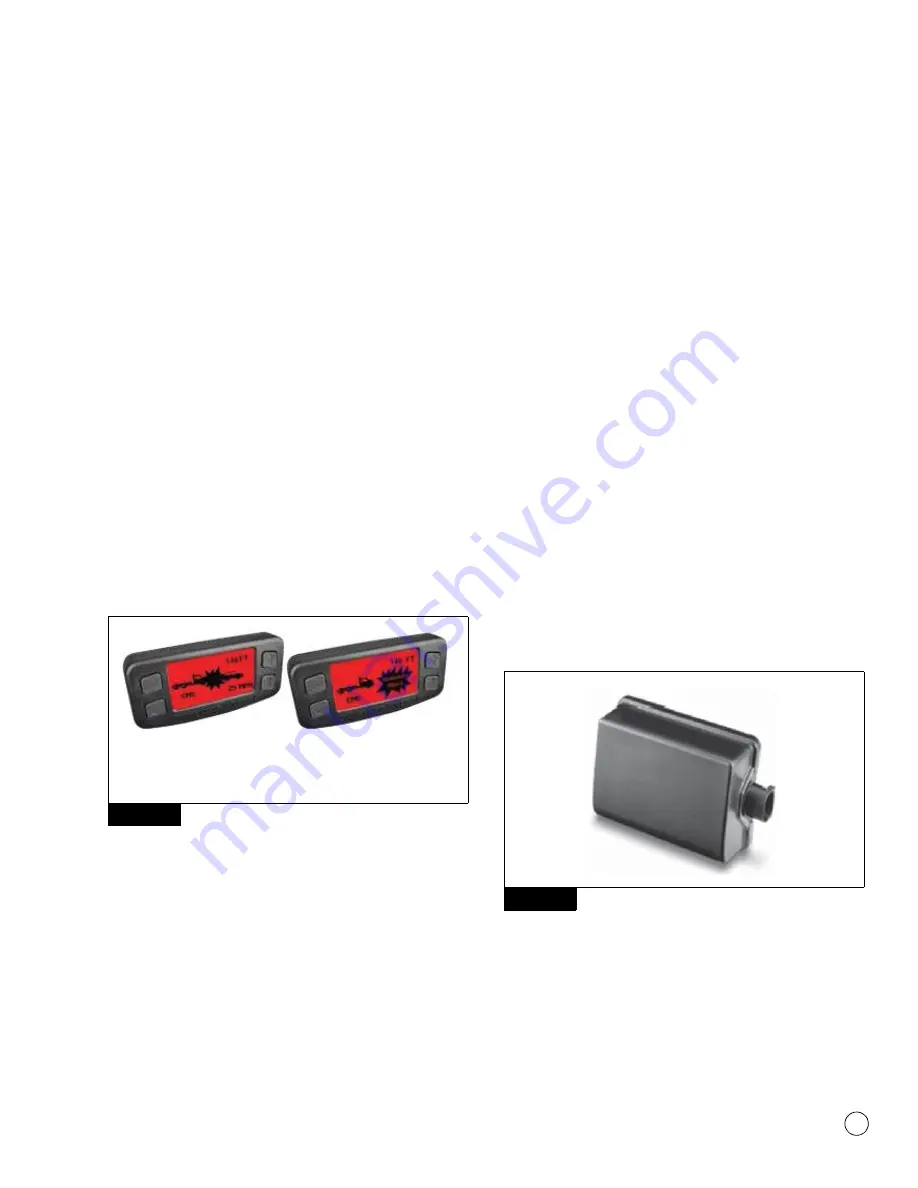
1
Introduction
3
WABCO
Maintenance Manual MM-1306 (Revised 08-18)
Collision Warning and Mitigation
When an unforeseen event occurs, such as another vehicle enters
the vehicle’s lane traveling slower than the vehicle, or the gap
between the vehicles becomes too close, the CMS will provide an
audible alert and the display will turn red with a collision warning
symbol. If the system determines that a rear-end collision is
imminent, it will automatically apply the brakes to reduce the
vehicle’s speed. The driver may also feel a haptic warning (short
brake pulse) to warn of collision danger.
The driver
must also take
the appropriate corrective action to avoid dangerous driving
situations. Figure 1.5.
The OnGuard™ CMS will not be active when the vehicle’s speed is
below 15 mph. If the OnGuard™ CMS detects a stationary object in
the vehicle’s lane (such as a disabled car) it will provide an audible
alert and the display will turn red showing a stationary object
symbol.
The OnGuard™ CMS will not apply the brakes or
reduce the vehicle’s speed when it detects a stationary object.
The OnGuardACTIVE™ CMS will not be active when the vehicle’s
speed is below 15 mph or over 77 mph. If the OnGuardACTIVE™
CMS detects a stationary object (such as a disabled car) it will
provide an audible alert, followed by a haptic warning and then a
brake application to reduce the vehicle’s speed.
Figure 1.5
System Limitations
OnGuard™ and OnGuardACTIVE™ CMS only brake for moving
objects located directly in front of your vehicle. The OnGuard™
CMS does not operate when your speed is below 15 mph. The
OnGuardACTIVE™ CMS does not operate when your speed is below
15 mph or over 77 mph. Accordingly, the CMS:
앫
Will not react and alert the driver to objects crossing in front of
the vehicle or oncoming traffic.
앫
Should not be relied on to track lead vehicles when traveling
through a severe curve in the road. Because of this, ACC is not
recommended for use on winding (curving) roads.
앫
Should not be relied upon to track smaller objects (e.g.
motorcycles, mopeds, bicycles, pedestrians, etc.).
앫
Should not be relied on to alert drivers to vehicles in an adjacent
lane.
앫
Will alert but not actively brake on stationary objects.
System Components
Radar Sensor
The radar sensor is used to detect vehicles and obstacles for the
OnGuard™ Collision Mitigation System. It is mounted in the front of
the vehicle near the center of the bumper and recessed in the
bumper in most applications. Figure 1.6. The sensor has an
electrical connector that provides power, ground and
communication to the SAE J1939 network which is required for
correct operation.
The mounting orientation is determined by the 3 hole bolt pattern of
the bracket. The radar sensor generally is mounted with the
connector on the driver’s side of the vehicle. The sensor connector
is protected by a rubber boot. This boot should fully cover the
connector upon completion of the sensor installation or repair.
Figure 1.6
Fascia
The fascia is a protective cover for the radar sensor and is
assembled to the same bracket on which the radar sensor is
mounted. Some vehicle manufacturer’s use other fascia designs.
Only original equipment fascias supplied by WABCO and the vehicle
manufacturer may be used to protect the radar sensor. Figure 1.7.
Figure 1.5
40118
6
0
a
Object
Collision Warning
Stationary
Collision Warning
Figure 1.6
4010334
a