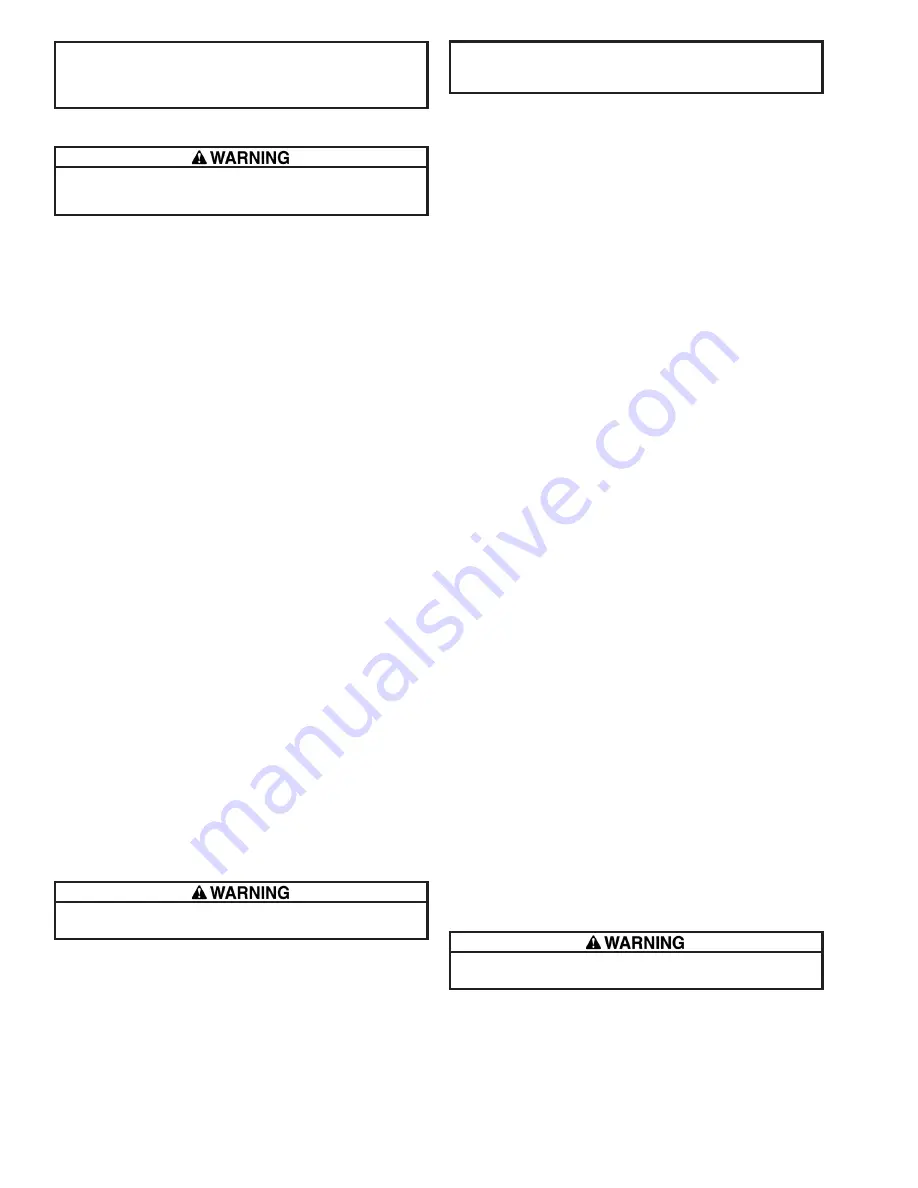
MICO, Inc.
(4)
Form No. 81-463-019 Revised 2017-06-01
SERVICE INSTRUCTIONS
Disassembly
(Refer to Figure 2)
1. Remove plug (7) from housing (15). Remove o-ring (2) from plug
(7).
NOTE: Plug (7) is under spring tension.
2. Remove spring (5) and rod (6) from housing (15).
3. Remove plug (1) from housing (15) and remove o-ring (2) from
plug (1).
4. Remove spool (3) from housing (15) through plug (7) end ONLY.
Remove seal (4) from spool (3).
5.
Some later designs use a directional spring (28). Directional
spring (28) is attached to screw assembly (31) by means of
the small diameter end of spring (28) being snapped into a
groove on the nose end of screw assembly (31). See Figure 2b.
Loosen nut (32) and remove screw assembly (31) from housing
(15). Remove o-ring (30) from screw assembly (31). Remove shim
(29), spring (28), steel ball (27), seat (26), o-ring (9), washer (25),
and two washers (24) from housing (15).
6. Remove plug (8) from housing (15) and remove o-ring (9) from
plug (8).
7. BEFORE moving screw (10), ACCURATELY MEASURE ITS
DEPTH from the end of housing (15) and record for reassembly
purposes. Remove screw (10) from housing (15).
8. Remove spring (12), retainer (13), and ball (14). Be sure to keep
ball (14) separate from ball (20) for reassembling.
9. Remove pin (11) from screw (10) using a drive pin punch.
NOTE: Be careful not to damage threads.
10. Remove plug (23) from housing (15). Remove o-ring (9) from
plug (23).
11. Remove spring (22), stop (21), and ball (20) from housing (15).
12. Place housing (15) on a bench with plug (23) end down. Spool
(19) may or may not fall out at this point.
13. Using a 6.35-7.87 mm (0.25-0.31 in) diameter wood or plastic
dowel, carefully remove insert (18) and spool (19) from housing
(15). Insert (18) must come out plug (23) end of housing (15).
Be careful not to scratch or mar valve seats on insert (18).
14. Remove spool (19) from insert (18). Remove o-rings (16 & 17)
from insert (18).
15. Remove plug (41) from housing (15). Remove o-ring (40) from
plug (41).
16. Remove spring (39), poppet (38), sleeve (36), poppet (34), and
spring (33) from housing (15).
NOTE: Be careful not to scratch
or mar housing or sleeve bore.
17. Remove o-rings (35 & 37) from sleeve (36).
18. Remove relief valve (44) from housing (15). Remove o-rings
(42 & 30) and back-up ring (43) from relief valve (44).
Assembly
(Refer to Figure 2)
CLEAN ALL PARTS WITH CLEAN SOLVENT AND DRY. LUBRICATE
ALL RUBBER PARTS WITH CLEAN SYSTEM FLUID PRIOR TO
ASSEMBLY. BE SURE ENTIRE ASSEMBLY PROCEDURE IS DONE
USING CONTAMINATION FREE METHODS.
1. Install new o-ring (2) on plug (1). Install plug (1) into housing (15)
and torque 67.8-81.4 N·m (50-60 lb·ft).
2. Install new seal (4) on spool (3). Be sure seal (4) does not twist
in groove.
3. Lubricate spool (3) with clean system fluid and properly install
into housing (15).
4. Install spring (5) and rod (6) into housing (15).
5. Install new o-ring (2) on plug (7). Install plug (7) into housing (15)
and torque 67.8-81.4 N·m (50-60 lb·ft).
6. Install new o-rings (16 & 17) on insert (18) and install insert into
housing (15). Note direction of assembly. Seat insert (18) with a
12.7 mm (0.50 in) diameter wood or plastic dowel.
7. Install spool (19) into insert (18) in housing (15). Note direction of
spool (19), long shoulder end faces end plug (23). See Figure 2a.
8. Install ball (20) on insert (18) in housing (15). Install stop (21)
over ball (20), and spring (22) over stop (21).
9. Install new o-ring (9) on plug (23). Carefully install plug (23) into
housing (15), centering spring (22). Torque plug (23) 47.5-54.2 N·m
(35-40 lb·ft).
10. Turn housing so plug (1) is vertically upward. Install ball (14) in
housing (15). Be sure ball (14) is centered in bottom of hole in
housing (15). Install retainer (13) and spring (12) into housing (15).
11. Insert new pin (11) in screw (10). Be sure pin (11) is aligned
properly and is evenly driven into screw (10).
NOTE: Be careful
not to damage threads.
12. Thread screw (10) into housing (15) to the depth recorded during
disassembly.
13. Install new o-ring (9) on plug (8). Install plug (8) in housing (15)
and torque 47.5-54.2 N·m (35-40 lb·ft).
14. Install new o-ring (30) on screw assembly (31).
15.
Some later designs use a directional spring (28). Directional
spring (28) is attached to screw assembly (31) by means of
the small diameter end of spring (28) being snapped into a
groove on the nose end of screw assembly (31). If necessary,
reattach the small diameter of spring (28) into the groove on
the nose end of screw assembly (31) using a slight twisting
motion. See Figure 2b.
Install two washers (24), washer (25),
new o-ring (9), seat (26), steel ball (27), and spring (28) into
housing (15). Fully lubricate shim (29) with clean system fluid
and install in housing (15) on end of seat (26). Install screw
assembly (31) in housing (15). Torque screw assembly (31)
24.4-29.8 N·m (18-22 lb·ft).
16. Install nut (32) on screw assembly (31) and torque 34.4-51.5 N·m
(32-38 lb·ft).
17. Install new o-rings (35 & 37) on sleeve (36).
18. Install spring (33), new poppet (34), sleeve (36), new poppet (38),
and spring (39) into housing (15).
19. Install new o-ring (40) on plug (41). Install plug (41) in housing (15)
and torque 67.8-81.4 N·m (50-60 lb·ft).
20. Install new back-up ring (43) and new o-rings (30 & 42) on relief
valve (44).
21. Install relief valve (44) in housing (15) and torque 47.5-54.2 N·m
(35-40 lb·ft).
Be sure system energy is relieved from accumulator charging valve
before removing from machine. See machine operating instructions
for procedures to relieve system energy.
NOTE
Locate the model number on the accumulator charging valve and
compare it to the model number in TABLE 2. Be sure you have the
proper service instructions.
Relief valve (44) is preset at the factory. DO NOT READJUST or
system damage or failure may occur.
Relief valve (44) is preset at the factory. DO NOT READJUST or
system damage or failure may occur.
NOTE
Observe torque specifications as indicated in assembly procedures
or system damage or failure may occur.
Summary of Contents for MICO ACV-DMO-RV
Page 7: ...Form No 81 463 019 Revised 2017 06 01 7 MICO Inc NOTES...
Page 8: ......