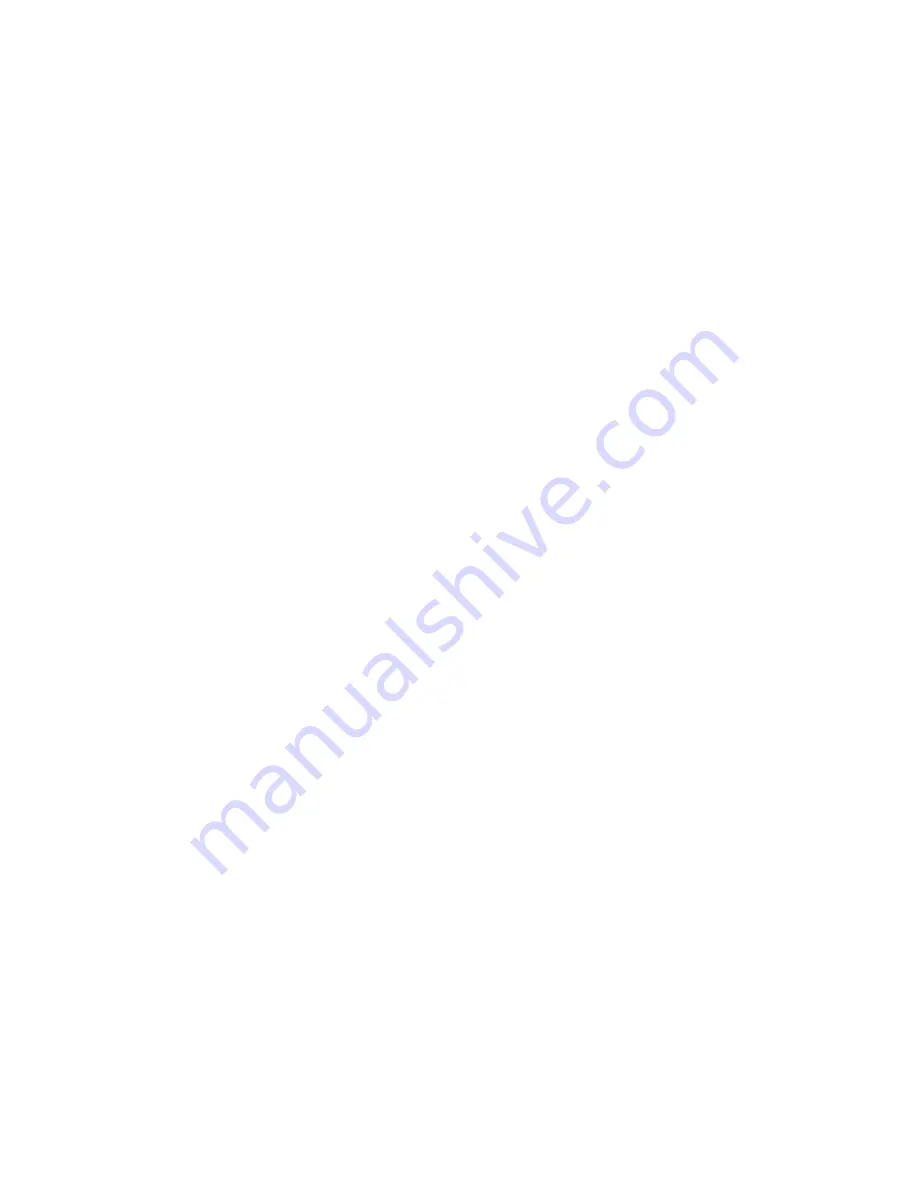
18
b. Horizontal guide adjustment.
It is critical when making this check to align
the vise jaws 90° to the saw bed.
(1) Use a combination square with the
head centered. Place the 90° side of the
head into the vise slide in the saw bed and
bring the face of the stationary vise jaw to
square with the combination blade.
Make the same adjustment on the movable
vise jaw.
(2) With vise jaws aligned square to the
saw bed, move the 90° side of the square
head to the end of the combination blade.
Place the head against the stationary vise
jaw and bring the square blade up against
the saw blade to check for square.
If the blade is square to both vise jaws, go to
step c.
(3) If the saw blade is not 90° to both vise
jaws discover which guide (or both) is out of
alignment. Mount a new blade on the
machine and tension it. On top of the guide
beam, loosen both guide arm clamps. The
tensioned blade will draw the guides into
alignment. Check the blade, square to the
vise jaws. Tighten one guide arm clamp at
a time to see which arm is pulling the
tensioned blade out of square to the vise
jaws.
(4) Determine which guide (or both) to
adjust to align the saw blade to the vise
jaws. Clamp the arm at the guide beam and
see the contents page for the blade guide
print.
(5) Loosen the hex screw at the top of
the plate holding the guide assembly to the
arm and the hex nut immediately under it,
unlocking the assembly plate and cam bolt,
allowing the assembly to rotate into
alignment.
(6) Locate the hex head cam bolt on the
opposite side of the plate from the hex lock
nut and adjust the plate and blade into
alignment with the blade wheels, square to
the vise jaws.
Use the combination square against the
blade and vise jaws to check the alignment.
See step (1).
c. Vertical blade/guide adjustment.
After a vise jaw adjustment to align the blade
square to the vise jaws, rotate the blade
back square with the saw bed.
(1) Place a dial indicator on the saw bed
near the guide, with the indicator contact
point against the saw blade, directly above
the tooth gullet.
(2) Set the dial to "0.
Open the saw head control valve slightly to
bring the blade down across the dial
indicator contact point slowly.
If the dial indicator reads "0" bottom to top of
the blade at both guides, go on to item 8,
metering valve linkage inspection.
(3) If step (2) failed, adjust any difference
in the dial indicator reading, bottom to top of
the blade, to "0." Locate the adjusting screw
above the guide rollers and the lock nut
behind the guide above the blade.
See the blade guide print. Loosen the lock
nut and turn the adjusting screw to tilt the
roller assembly, bringing the blade to vertical
square with the saw bed. Visually check the
alignment with the combination square.
Check the alignment with the dial indicator
for a "0" reading from bottom to top of the
blade as it passes over the indicator tip.
7. Metering valve inspection.
See the contents page for the blade guide
and metering valve prints.
With each blade change, inspect the blade
guides for chips and sludge build up that pre-
vent metering valves and linkage from work-
ing properly.
If the sawing force check failed check the
blade guides and linkage before making this