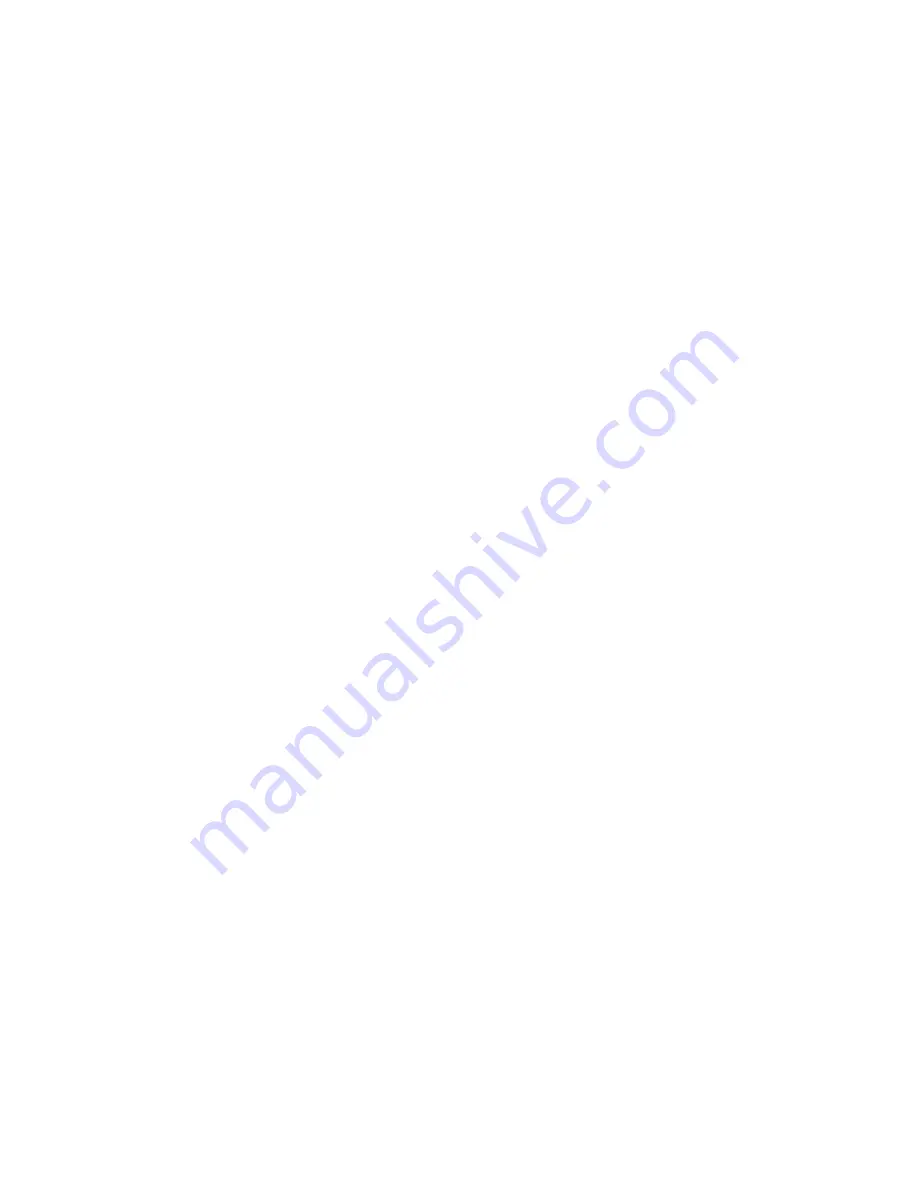
17
added to the linkage, or, guide blocks
binding the blade. Go to the next step for a
blade guide inspection.
6. Blade guide inspection.
NOTE: Consider this and the next two items
on linkage and metering valve inspection
before making adjustments.
Routinely, when changing blades, check the
guide rollers and backup slipper for dirt and
sludge and proper guide roller clearance.
Normally, guides require adjustment only
after years of wearing in.
If stock or material handling equipment near
the machine bumps the guides they will
break or misalign and require adjustment or
replacement.
Following are three preventive maintenance
checks.
a. Clean, inspect and adjust the guide
rollers.
(1) Guides are factory set .001" wider
than the blade thickness.
.042 blade thickness requires .043 guide
roller clearance.
See the contents page for the blade guide
print.
Guide rollers adjusted too tight or too loose
cause erratic sawing rates, inaccurate cuts
and broken blades.
Release blade tension and lock or tag out
the electric disconnect.
(2) Remove the blade and flush out the
guides.
(3) Check roller clearance with feeler
gauges, or, assemble a new blade on the
machine. Tension the blade.
Look for a tight or loose fit.
Force the tensioned blade down out of the
guide. It must only partly return up into the
guide rollers when released.
(4) Look for blade movement in the saw-
ing area between the guides.
Twist the blade back and forth between the
blade wheel and guide.
(5) If feeler gauges read correct, or if the
tensioned blade only partly returns when
pushed down out of the rollers and there is
no blade movement between the guides
when twisted from outside the guides,
problems with the sawing force check are
not with guide roller clearance.
Go to item 8 on metering valve linkage
check.
(6) If step (5) failed, adjust the guide roll-
ers. Raise the saw head.
Release blade tension. Lock or tag out the
electric disconnect switch.
(7) Release the carbide side inserts so
they can float with the blade during adjust-
ment.
(8) One roller on each guide rigidly
mounts to the casting and is not adjust-
able. The companion roller adjusts on a
cam shoulder bolt. Loosen the lock nut on
top of the high side of the roller casting,
unlocking the cam bolt. Turn the cam bolt
at the bottom of the roller.
(9) Use feeler gauges to adjust clearance
between the rollers .001" wider than blade
thickness, or go back to step (3).
Caution: Rollers gripping the blade too tight
prevent the metering valve from controlling
sawing force; the blade will snake through
the rollers, inaccurate sawing and blade
break results.
(10) Install and tension a new blade on
the machine. With rollers adjusted, hold the
floating carbide side inserts snug against the
blade and draw them up to the roller casting
with the hex head screws.
Lock them in place against the blade with the
socket set screws at the side of the guide
casting.