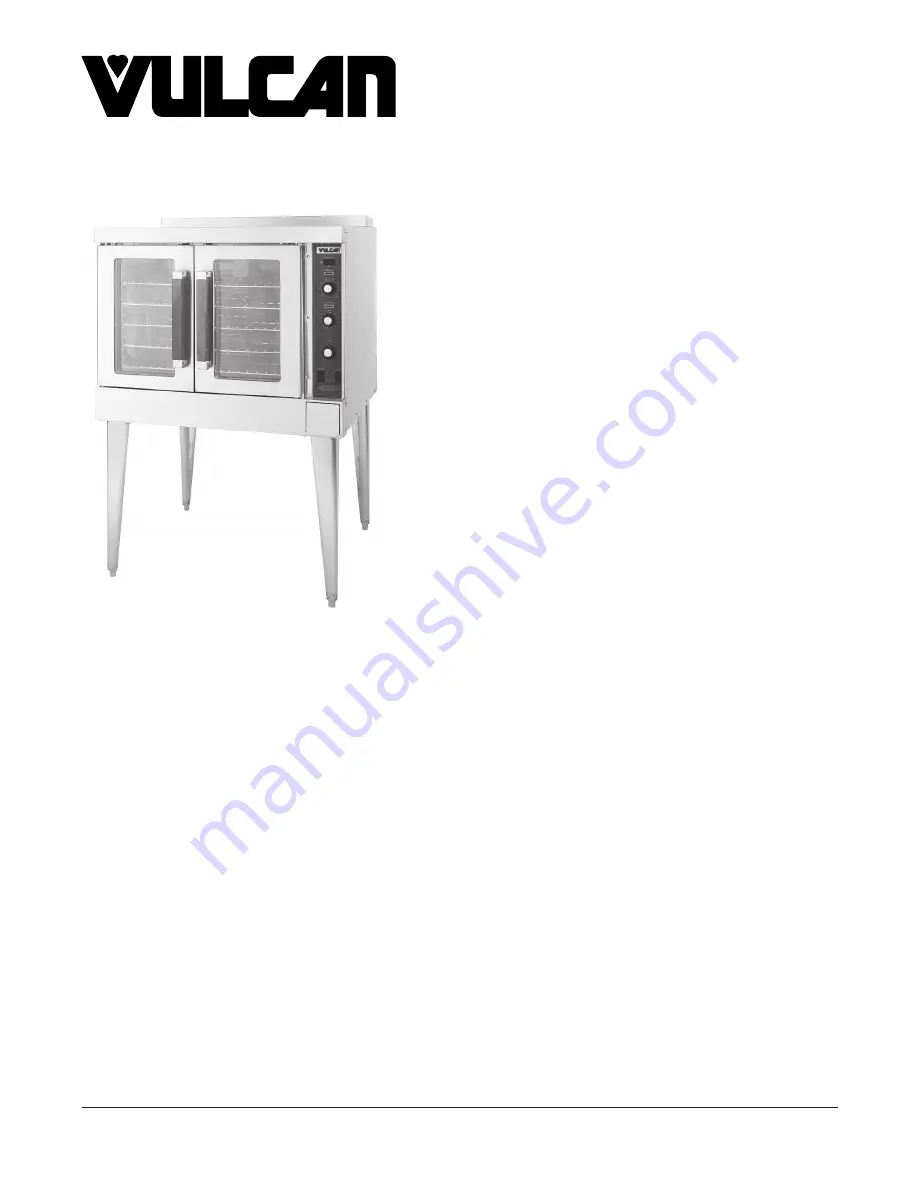
– 1 –
Model SG4D
SERVICE MANUAL
SG4 & SG6 SERIES
FULL SIZE GAS
CONVECTION OVENS
MODELS
SG4D
ML-114875
SG4C
ML-114876
SG6D ML-114877
SG6C
ML-114878
V U L C A N - H A R T C O M P A N Y , P . O . B O X 6 9 6 , L O U I S V I L L E , K Y 4 0 2 0 1 - 0 6 9 6 , T E L . ( 5 0 2 ) 7 7 8 - 2 7 9 1
FORM 31192 (Jan. 2002)
NOTICE
THIS MANUAL IS PREPARED FOR THE USE OF TRAINED VULCAN SERVICE TECHNICIANS
AND SHOULD NOT BE USED BY THOSE NOT PROPERLY QUALIFIED. IF YOU HAVE ATTENDED
A VULCAN SERVICE SCHOOL FOR THIS PRODUCT, YOU MAY BE QUALIFIED TO PERFORM
ALL PROCEDURES DESCRIBED IN THIS MANUAL.
THIS MANUAL IS NOT INTENDED TO BE ALL ENCOMPASSING. IF YOU HAVE NOT ATTENDED
A VULCAN SERVICE SCHOOL FOR THIS PRODUCT, YOU SHOULD READ, IN ITS ENTIRETY,
THE REPAIR PROCEDURE YOU WISH TO PERFORM TO DETERMINE IF YOU HAVE THE
NECESSARY TOOLS, INSTRUMENTS AND SKILLS REQUIRED TO PERFORM THE
PROCEDURE. PROCEDURES FOR WHICH YOU DO NOT HAVE THE NECESSARY TOOLS,
INSTRUMENTS AND SKILLS SHOULD BE PERFORMED BY A TRAINED VULCAN SERVICE
TECHNICIAN.
REPRODUCTION OR OTHER USE OF THIS MANUAL, WITHOUT THE EXPRESS WRITTEN
CONSENT OF VULCAN-HART COMPANY, IS PROHIBITED.
Summary of Contents for SG4C ML-114876
Page 2: ...2 VULCAN HART COMPANY 2002...
Page 38: ...38 WIRING DIAGRAMS WIRING DIAGRAM SG4D SG6D OVENS 120 200 V 424372 Rev F...
Page 39: ...39 WIRING DIAGRAM 734 COMPUTER CONTROL DUAL BURNER CONVECTION OVENS 120 200 V 426574 Rev C...
Page 40: ...40 SCHEMATICS GAS CONVECTION OVEN SG4 WITH STD CONTROL 424373 1 REV C...
Page 41: ...41 GAS CONVECTION OVEN SG4 WITH WATLOW 734 CONTROL 426575 1 REV C...