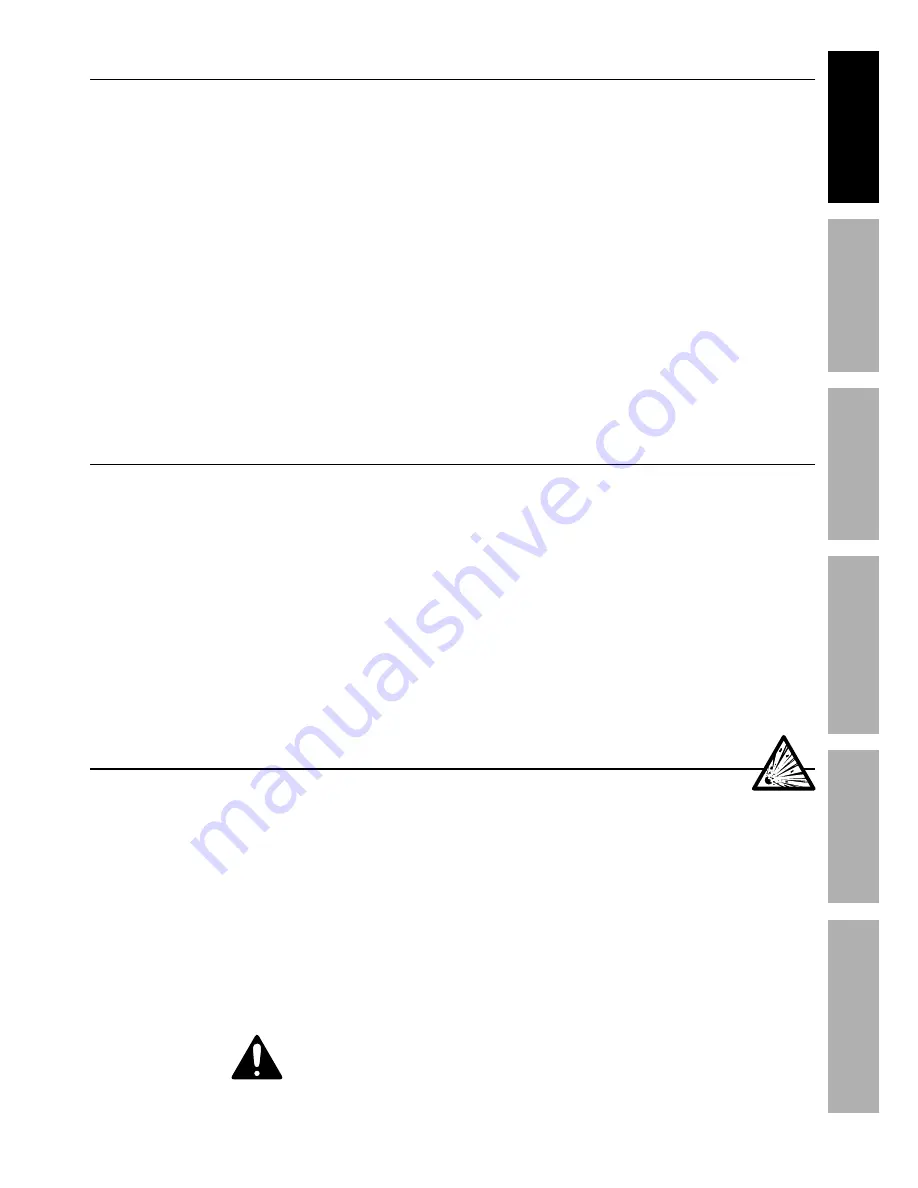
Page 5
For technical questions, please call 1-888-380-0318.
Item 63621
S
AFET
y
W
EL
d
IN
g T
Ip
S
MAINTENAN
c
E
TI
g
/ S
TI
ck
c
ONTROLS
W
IRE
Welder Use and care
1.
do not use the welder if the switch does not turn
it on and off.
Any welder that cannot be controlled
with the switch is dangerous and must be repaired.
2.
disconnect the plug from the power
source before making any adjustments,
changing accessories, or storing welders.
Such preventive Safety measures reduce the
risk of starting the welder accidentally.
3.
prevent unintentional starting.
Ensure the switch is in the off-
position before connecting to power
source or moving the welder.
Carrying
or energizing welders that have the
switch on invites accidents.
4.
Store idle welders out of the reach of
children and do not allow persons unfamiliar
with the welder or these instructions to
operate the welder.
Welders are dangerous
in the hands of untrained users.
5.
Use the welder and accessories in
accordance with these instructions, taking
into account the working conditions and
the work to be performed.
Use of the welder
for operations different from those intended
could result in a hazardous situation.
6.
do not use the welder for pipe thawing.
Maintenance
1.
Maintain welders. check for misalignment or
binding of moving parts, breakage of parts
and any other condition that may affect the
welder’s operation. If damaged, have the
welder repaired before use.
Many accidents
are caused by poorly maintained welders.
2.
Have your welder serviced by a qualified
repair person using only identical
replacement parts.
This will ensure that
the Safety of the welder is maintained.
3.
Maintain labels and nameplates on the Welder.
These carry important information.
If unreadable or missing, contact
Harbor Freight Tools for a replacement.
4.
Unplug before maintenance.
Unplug the Welder
from its electrical outlet before any inspection,
maintenance, or cleaning procedures.
gas Shielded Welding - cylinder Safety
cylinders can explode when damaged.
1.
do not weld on a pressurized or closed cylinder.
2.
do not allow an electrode holder,
electrode, welding torch, or welding
wire to touch the cylinder.
3.
keep cylinders away from any electrical circuits,
including welding circuits.
4.
keep protective cap in place over the valve
except when the cylinder is in use.
5.
Use only correct gas shielding equipment
designed specifically for the type of welding
you will do.
Maintain this equipment properly.
6.
protect gas cylinders from heat, being struck,
physical damage, slag, flames, sparks, and arcs.
7.
Use proper procedures to move cylinders.
SAVE THESE INSTRUcTIONS.