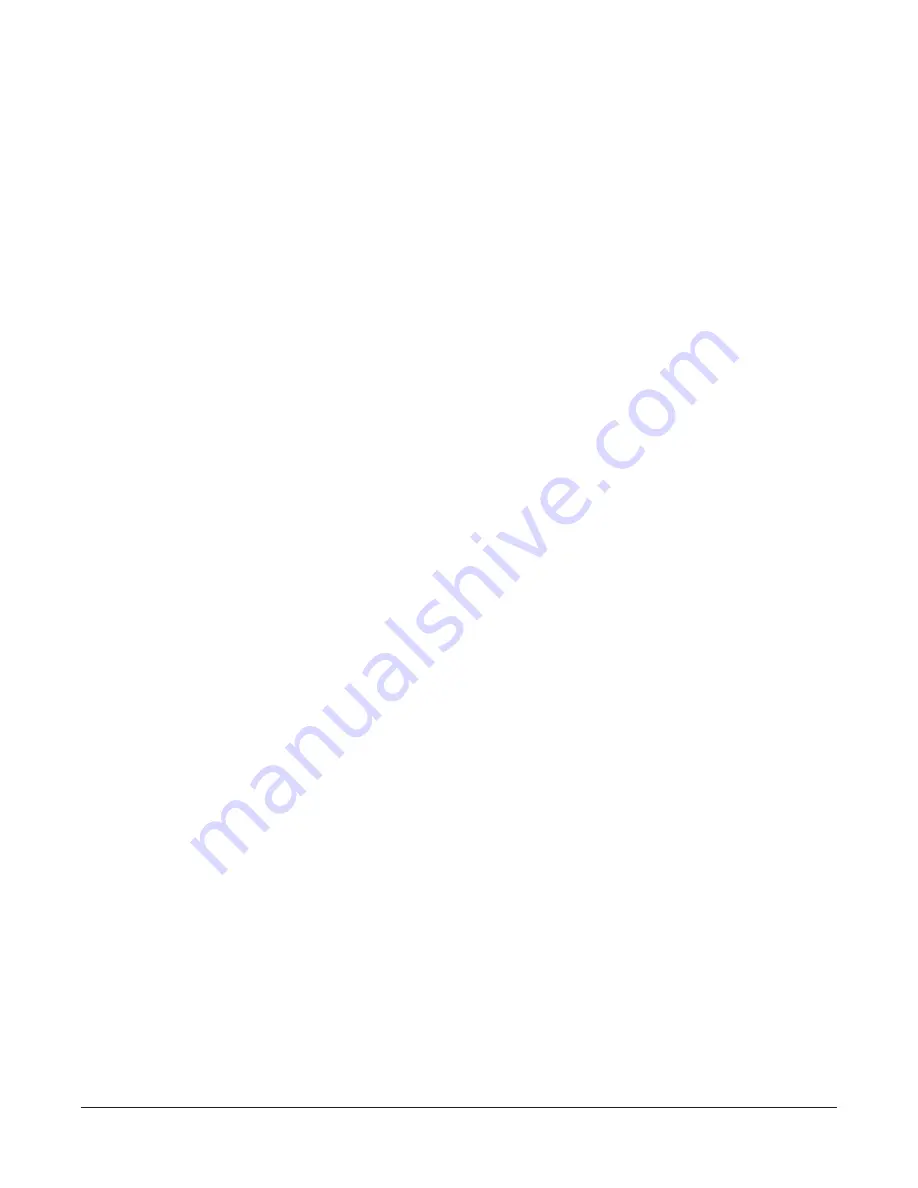
— 5 —
OPERATION
WARNING:
THE KETTLE AND ITS PARTS ARE HOT. USE CARE WHEN OPERATING, CLEANING
AND SERVICING THE KETTLE.
BEFORE FIRST USE
Using a non-corrosive, grease-dissolving commercial cleaner, clean the protective metal oils from all
surface parts and interior of the kettle. Follow the cleaner manufacturer's directions. Rinse thoroughly
with warm water to remove all traces of the cleaner. Drain the kettle. Wipe dry with a soft clean cloth.
CONTROLS
On-Off Switch
— Turns power to the kettle on or off.
Thermostat Switch,
— These three switches are wired in series and control the supply of
Low Water Cutoff Switch,
energy to the heating elements. Opening any one of these pressure
Limit Switch
switches will shut off the power supply to the heating elements.
Thermostat
— Senses the temperature in the steam jacket. At a dial setting of 5 to
6, it will cut power off as the pressure gauge needle moves off zero.
The higher dial settings are for cooking, the lower ones for holding. At
the higher dial settings, the steam pressure in the jacket will drop to
2 to 2
1
/
2
psi after the thermostat cuts the power off and before it cuts
it on.
Low Water Cutoff Switch
— Cuts off power to the heating elements if the jacket distilled water
level is too low.
Pressure Relief Valve,
— Protect the kettle against excessive pressure should the thermostat
Pressure Limit Switch
malfunction. The pressure relief valve is rated so that it will relieve
generated steam faster than the heating elements can generate it.
Pressure Gauge
— Indicates pressure in the jacket.
Sight Glass Assembly
— Visually shows the distilled water depth in the steam jacket.
Thermostatic Air Vent
— Lets air out of jacket as steam is generated; closes at approximately
180°F to prevent the steam from escaping.
Fill Assembly
— Location for adding distilled water to the jacket. It is equipped with
a manual valve plus a check valve to prevent a discharge should the
manual valve be inadvertently opened while the jacket is under pressure.
Food Draw-Off Valve
— Allows food and liquid to be drawn off from the kettle.
Summary of Contents for EL40
Page 14: ...14 WIRING DIAGRAM...
Page 15: ...15 WIRING DIAGRAM...
Page 16: ...16 WIRING DIAGRAM...
Page 17: ...17 WIRING DIAGRAM...
Page 19: ...19 NOTES...
Page 20: ...20 NOTES FORM 30965 8 97 Formerly 990202 PRINTED IN U S A...