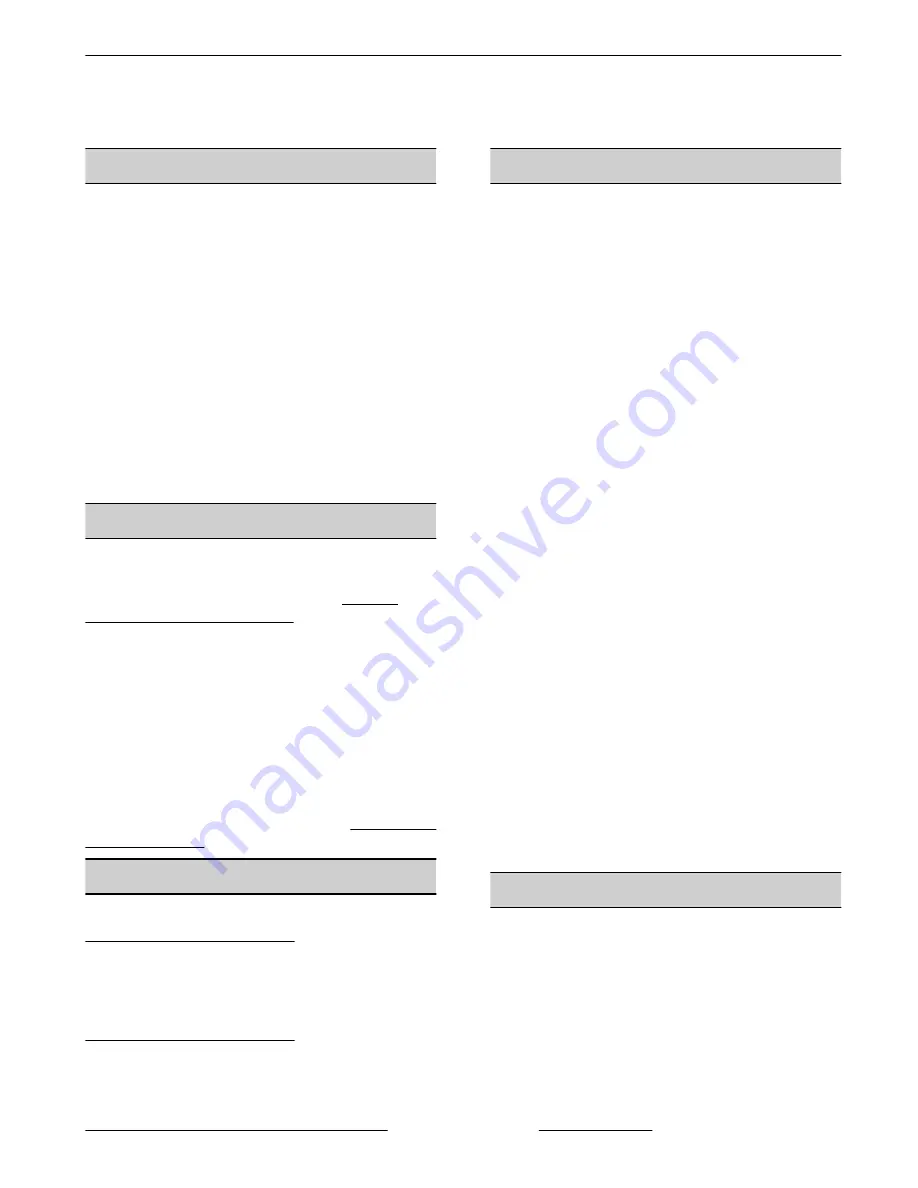
GENERAL
INTRODUCTION
This Service Manual covers specific service
information related to the models listed on the front
cover. Procedures in this manual will apply to all RRG
Heavy Duty Gas Griddles unless otherwise specified.
Raising of the griddle plate is not required for servicing
the griddle components. Griddle components are
serviced through the front and rear. Pictures and
illustrations can be of any model unless the picture or
illustration needs to be model specific.
The RRG, Rapid Recovery Griddle, plate is a
composite material which is engineered to provide a
high heat transfer rate to the food. The top surface can
be scored or dented by careless use of a spatula or
scraper. The center of the of the plate is an aluminum
core with sheets of stainless steel laminated to the top
and bottom exterior surfaces.
INSTALLATION
Generally, installations are made by the dealer or
contracted by the dealer or owner. Detailed
installation instructions are included in F-36981
Installation & Operation Manual that is sent with each
unit.
It should be noted that an improperly installed unit,
especially an unlevel unit can lead to premature
electrical component failures. A unit that is higher in
the front will cause the flue gases to vent improperly
and gather in the front near the electrical components.
All RRG models must be installed with an externally
mounted regulator.
The models, number of burners and BTU/HR input
rating are listed under GENERAL in the Installation &
Operation Manual.
OPERATION
Detailed operation instructions are included in the
Installation & Operation Manual sent with each unit.
The manual is also available online at
www.vulcanequipment.com.
The operation of the griddle controls, pilots and
burners are outlined under CONTROLS in the
Installation & Operation Manual.
SPECIFICATIONS
Electrical
- 120VAC 50/60Hz 1 Amp single phase.
- 6 foot corded plug with ground supplied.
Gas Manifold Pressure:
- Natural Gas 5.0" W.C.
- Propane Gas 10.0" W.C.
- Gas pressure regulator supplied with the unit must
be installed.
Incoming Gas Pressure:
- 7" to 9" W.C. Natural Gas
- 11" to 12" W.C. Propane Gas.
- Incoming pressure should not exceed 14.0" W.C.
(0.5 PSI) for either gas type.
Burners
- One 27,500 BTU/HR “U” shaped aluminized steel
burner for each 12" of griddle width.
Controls
- One Solid State thermostat with embeded
thermocouple for each 12" of griddle width.
- Temperature adjustment range 150°F to 450°F.
- Electronic ignition module with pilot safety system.
- There is one pilot for every two burners. A flash tube
mounted between two burners is used to light the
ignition ports on the burners.
- On 36” and 60” griddles there is an odd number of
burners to light. One pilot and one electronic ignition
module on these griddles will control a single burner
only.
TOOLS
Standard
•
Standard set of hand tools.
•
VOM and meter leads rated CAT III 600v or
higher. Meter must also have a certification.
•
Temperature tester (K type thermocouple
preferred) with surface probe.
•
U-Tube or Digital Manometer.
RRG SERIES HEAVY DUTY GAS GRIDDLE - GENERAL
Page 3 of 24
F45514 (0214)