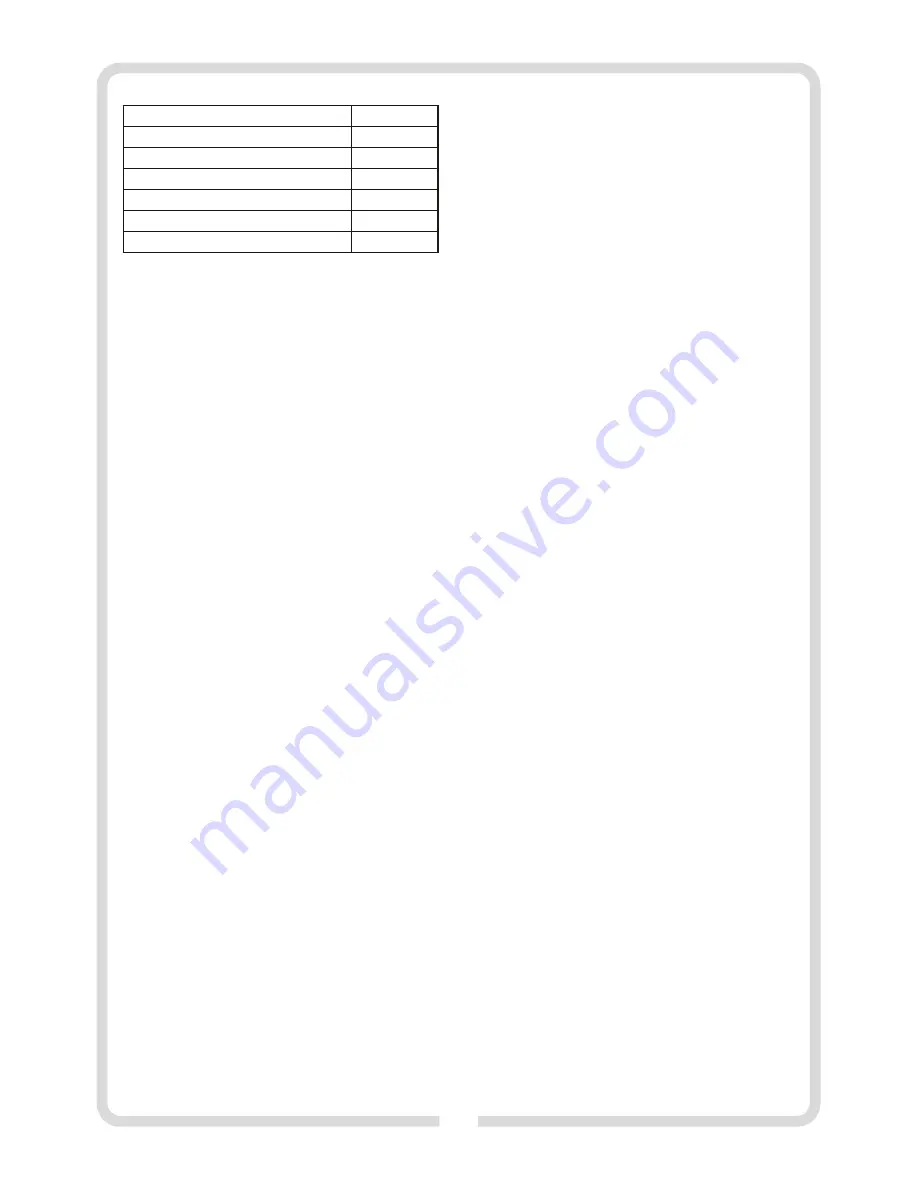
should always be parallel to the cutting disk. The adjustment of the
guide should always be monitored, using the cut-width scales (
12
) on
the surface of the workbench (
8
).
ź
In the event of mounting the guide on the other side of the
workbench, place the guide on the opposite side of the limiter rack and
screw it down.
OPERATION:
Prior to connecting the device check if the data on the rating plate
conform with the parameters of the mains. The mains, to which the
S2 30 min: casual work, nominal work time 30 min.
cutter is connected, must be safeguarded with a 10 A fuse.
CAUTION!
After 30 min of work with constant load pause the work until the
Turning on/off
cutter cools off completely.
To switch on the cutter, press the green button «
I
» of the on/off switch
PREPARATION FOR WORK:
(
4
). Prior to commencing work wait until the cutter reaches its maximum
CAUTION!
Ensure appropriate order and lighting of the work place.
rotational speed and the coolant pump starts forcing water onto the
Unpack the cutter and check for any transport damage.
cutting disk.
To turn the cutter off, press the red button «
0
» of the on/off switch (
4
).
Mounting the cutter
CAUTION!
After each adjustment please run a test cutting in order to
CAUTION!
Prior to any maintenance work, reattaching and assembly of
confirm the new parameters.
the device make sure that the power cord is disconnected from the power
supply.
General guidelines on cutting
Prior to mounting the cutter check the completion of the device and the
For all types of cutting first make sure that the cutting disk does not touch
condition and attachment of movable components (cutting disk (
20
)
the guides or any other parts of the device at all stages of work.
and protective screen (
10
) on the separating wedge (
11
) ):
Ensure that all screens are properly attached.
ź
turn the disk manually (make sure the plug is out of the mains socket)
Protect the cutting disk from falling down or shocks. Do not apply lateral
to check whether the drive transmission mechanism is not blocked
force to the disk.
and the disk is properly attached,
Operator's position
ź
the mounting nut of the protective screen on the separating wedge
Do not stand in line with the disk in front of the device. Always stand
should be tightened in a manner enabling the protective screen (
10
)
slightly to the side.
to lift when material reaches the cutting disk and return back when
Jamming
cutting is over.
In the event of jamming of the cutting disk, turn the cutter off, unplug it
After checking the components the cutter and the coolant container (
14
)
from the power supply and remove the processed material.
should be placed firmly and screwed down to the workbench or another
Straight cut
stable surface. Use the mounting openings to screw down the device (
1
).
Adjust the cut width using the parallel guide (
7
) and lock with wing bolts
Prior to turning on please install the separating wedge with the
(
5
). The width of the cut can be read using the scales (
12
).
CAUTION:
The
protective screen and fill the coolant container with water (
14
) to the
scales must be set identically on both sides of the table.
indicated level (
16
).
Fig.
E
demonstrates the appropriate position of hands for straight
Adjustment of the separating wedge
cutting. The tiles should be moved with both hands. Hands should be
CAUTION:
The separating wedge secures the processed item from
placed away from the cutting line of the tile.
capturing by the disk and ejecting it towards the operator. The wedge must
The movement must correspond to disk cutting capacity. Move the
be installed at all times. Properly adjusted wedge should be in line with the
processed material slowly and evenly forward. During cutting the
disk, approx. 2-5 mm from the disk edge.
cutting disk cannot significantly lower its rotational speed, so adjust the
ź
In order to adjust the separating wedge (
11
), loosen the wing bolts
pressure accordingly. After cutting the tile, turn the cutter off.
(
3
) on both sides of the workbench (
8
) and angle the workbench, so that
CAUTION:
Ejection of minor quantities of water by the disk during
the separating wedge can be placed in the holder (see: fig.
B
). Then,
operation is normal. The water level in the container should be monitored
place the wedge (
11
) in line with the cutting disk (
20
), adjust the
on a regular basis.
2-5 mm clearance between the wedge and the disk and tighten the
Diagonal cut
mounting bolts (
21
), locking the wedge in this position.
CAUTION:
When cutting using the angle guide, always use the parallel
Mounting the parallel guide
guide. This method is applicable only to small tiles.
The parallel guide (
7
) can be placed on both sides of the workbench (
8
).
ź
Rest the angle guide (
9
) against the parallel guide (
7
) (fig.
F
).
ź
Mount the wing bolts (
5
) and nuts for the guide (
7
).
ź
Adjust the parallel guide (
7
) to the proper width and lock with wing
ź
Slide the guide fixture into the stop strip (
6
) of the workbench (
8
).
bolts (
5
) on both sides of the cutter.
ź
Adjust the guide according to working requirements and screw down
ź
Place the material in the angle guide (
9
).
the mounting bolts (
5
).
In order to protect the processed material from jamming, the guide
ź
Turn the cutter on and, after reaching maximum rotational speed,
n
n
n
n
n
n
n
n
n
7
Sound pressure level
(LpA)
92 dB(A)
Sound power level
(LwA)
105 dB(A)
Gross/net weight
10,0 kg / 9,6 kg
Equipment class/ Ingress protection
I / IP 20
Workbench dimensions 360 x 330 mm
2
Vibration level a (K=1,5m/s ) acc. to EN 61029-1
n
2
<
2,5 m/s
Work cycle
S2 30 min
Summary of Contents for VG18601
Page 2: ...2 5 1 2 3 4 6 7 9 10 11 8 12 13 14 A 19 18 16 B 15 17 13 20 17...
Page 17: ...RCD VG18601 17...
Page 18: ...18 a a...
Page 19: ...a a a a RCD 19...
Page 22: ...2 D 2 n n n 14 15 n 13 7 5 18 12 19 B 20 E 17 n n 9 7 F 7 5 9 14 9 7 n n 3 8 22...
Page 23: ...34 03 228 23 n...
Page 39: ...39...
Page 40: ...www profix com pl...