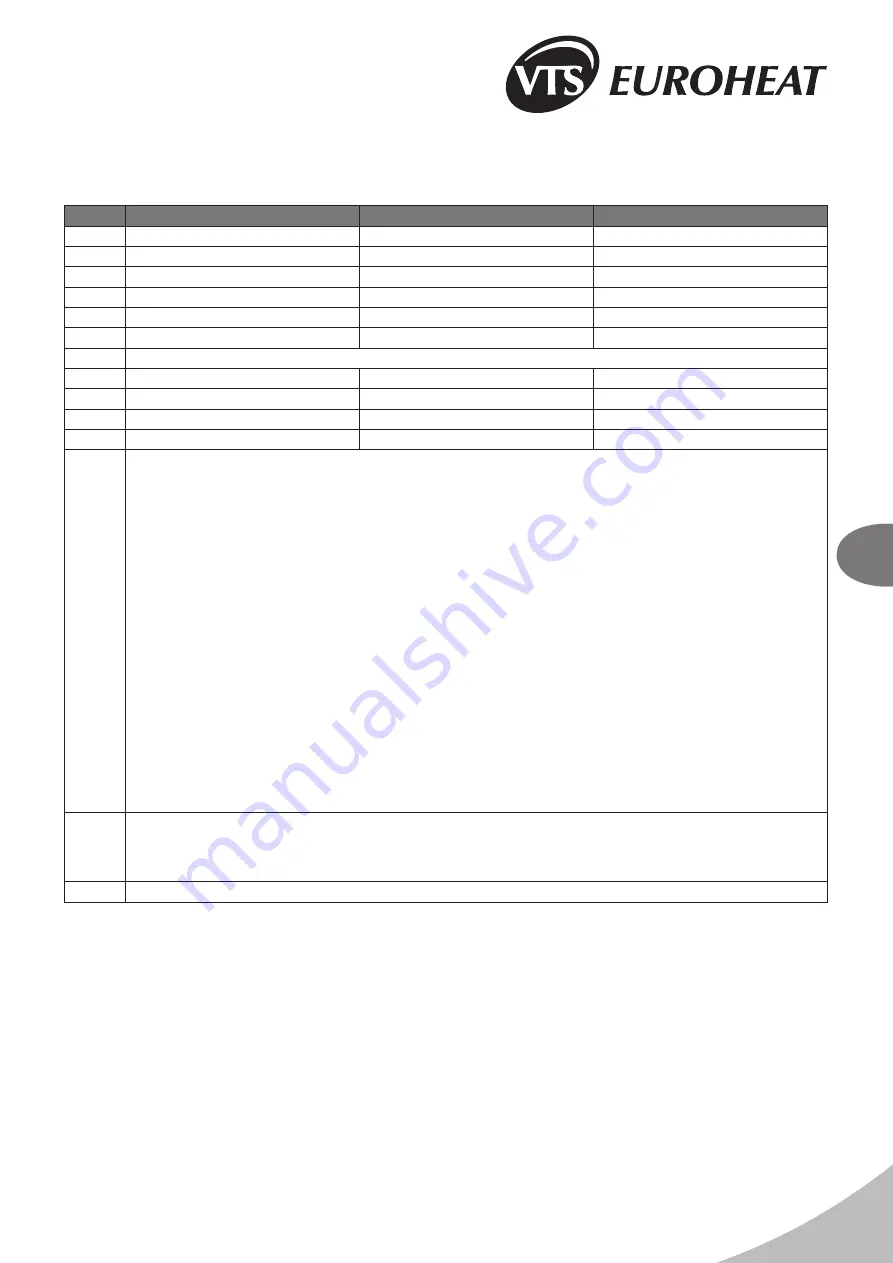
19
EN
10. TECHNICAL INFORMATION TO THE REGULATION (EU) NO
327/2011 IMPLEMENTING DIRECTIVE 2009/125/EC
DR 100
DR 150
DR 200
1.
26,0%
26,0%
26,0%
2.
B
B
B
3.
Total
Total
Total
4.
21
21
21
5.
VSD-No
VSD-No
VSD-No
6.
2014
2014
2014
7.
VTS Plant Sp. z o.o., CRN 0000144190, Poland
8.
1-2-2801-0232
1-2-2801-0233
1-2-2801-0234
9.
0,68kW, 6182m³/h, 128Pa
0,516kW, 4239m³/h, 124Pa
0,68kW, 6182m³/h, 128Pa
10.
1372RPM
1370RPM
1372RPM
11.
1,0
1,0
1,0
12.
Disassembly of the machine must be carried out and/or supervised by qualified personnel with appropriate expert
knowledge.
Contact a certified waste disposal organization in your vicinity. Clarify what is expected in terms of the quality of
dismantling the machine and provision of the components.
Dismantle the machine using the general procedures commonly used in mechanical engineering.
WARNING
Machine parts can fall The machine is made up of heavy parts. These parts are liable to fall during dismantling. This can
result in death, serious injury, or material damage.
Follow the safety rules:
1. Disconnect all electrical connections.
2. Prevent reconnection.
3. Make sure that the equipment is at zero voltage.
4. Cover or isolate nearby components that are still live.
To energize the system, apply the measures in reverse order.
Components:
The machines consist for the most part of steel and various proportions of copper, aluminum and plastics (Impeller made
of SAN - styrene, acrylonitryle, construction material with 20% glass fiber) and rubber-neoprene (seat of bearings/hub).
Metals are generally considered to be unlimitedly recyclable.
Sort the components for recycling according to whether they are:
Iron and steel, aluminum, non-ferrous metal, e.g. windings (the winding insulation is incinerated during copper recycling),
insulating materials, cables and wires, electronic waste (capacitor ect.), plastic parts (impeller, winding cover ect.),
rubber parts (neoprene). The same goes for cloths and cleaning substances which have been used while working on the
machine.
Dispose of the separated components according to local regulations or via a specialist disposal company.
13.
Long failure-free operation depends on keeping the product/device/fan within performance limitations described by
selection software or maintenance manual.
For proper operation, read carefully maintenance manual, with special attention on “installation”, “start-up”, and
“maintenance” chapters.
14.
fan casing, internal profiles