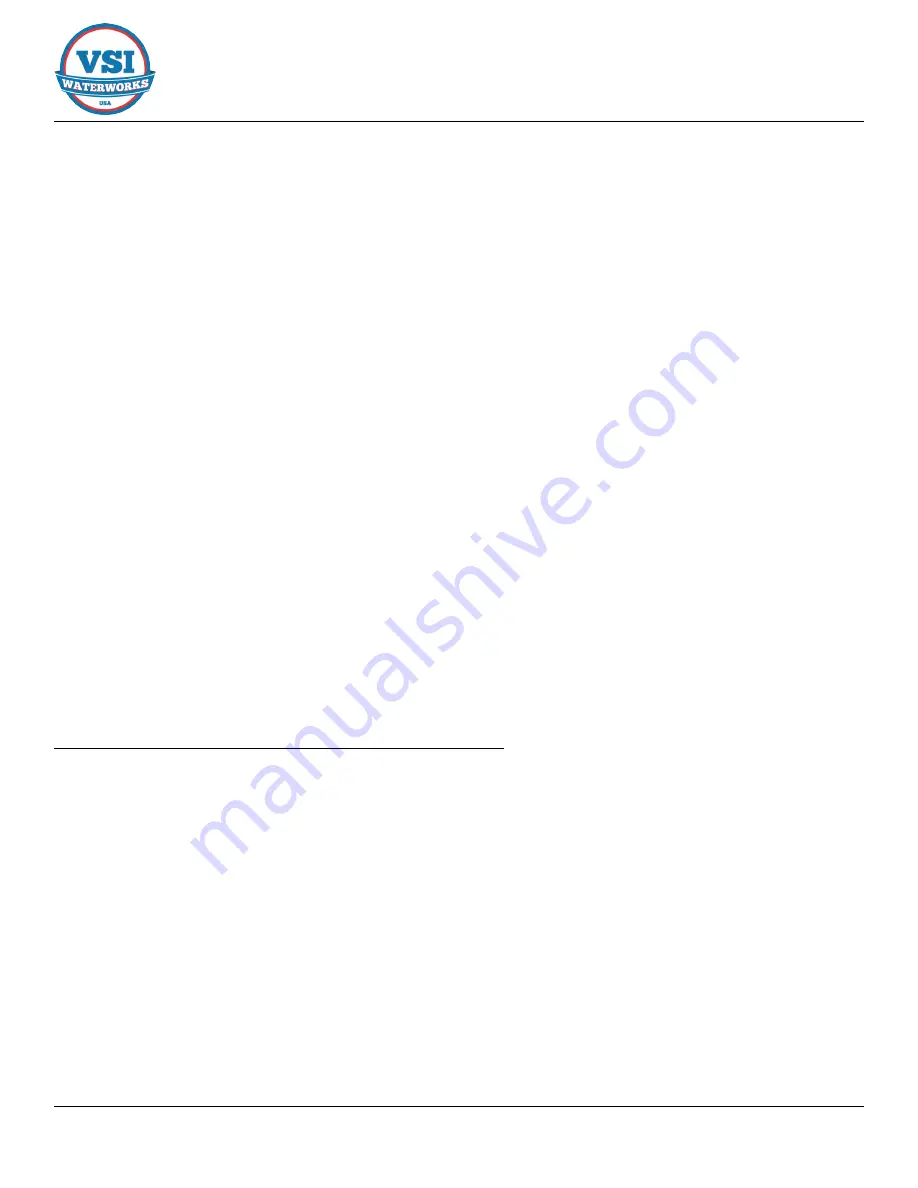
INSTALLATION, OPERATION AND MAINTENANCE
VSI AWWA C508 RUBBER FLAPPER CHECK VALVE
VRSG-3
02-16
© 2014 VSI Waterworks LLC
6
SECTION 6: INSPECTION AND MAINTENANCE
Sec. 6.1 Valve Exercising
Each Valve should be operated through a full cycle and returned to its normal position on a time schedule
designed to prevent a buildup of tuberculation or other deposits that could render the Valve. The interval of
time between operations of Valves in critical locations, or Valves subjected to severe operating conditions,
should be shorter than that for less important installations, but can be whatever time period is found to
be satisfactory based on local experience. Maintenance should be performed at the time a malfunction is
discovered. A recording system should be adopted that provides a written record of valve location, condition,
maintenance, and each subsequent inspection of the valve
Sec. 6.2 Spring Return Attachment Option
Rubber Flapper Swing Check Valves is designed to minimize or eliminate slam in high head applications where
rapid flow reversal causes the Swing Check Valve to slam. The Valve has a 35° disc stroke, leaving 80° to 90° of
travel. Having the spring return attachment option causes the disc to accelerate valve closure. Having the Valve
closed before reverse flow occurs can in many instances drastically reduce or even eliminate Valve slam.
Sec. 6.3 Inspection
Each valve should be operated through one complete operating cycle. With the Check Valve in the partially
open position, a visual inspection should be performed, where practical, to check for leakage at all joints,
connections, and areas of seals. If leakage is observed, all defective O-rings, seals, gaskets, or end connection
sealing members should be replaced. If the leakage cannot be corrected immediately, the nature of the
leakage should be reported promptly to those who are responsible for repairs. If the valve is inoperable
or irreparable, its location should be clearly established to save time for repair crews. The condition of the
valve and, if possible, the position, should be reported to personnel responsible for repairs. In addition, the
appropriate municipal departments should be informed that the valve is out of service.
Sec. 6.4 Maintenance
ATTENTION: DO NOT WORK ON ANY VALVE UNDER PRESSURE
Rubber Flapper Swing Check Valves does not require routine maintenance, but should be included as part of
the normal facility equipment inspections for any malfunction while under normal usage conditions.
a. Relieve the pressure in the line.
b. Isolate the Rubber Flapper Swing Check Valve from the system before loosening the cover bolts
to remove the cover.
c. Loosen each cover bolt only three to four full turns, tapping the side of the cover with a rubber
mallet to separate only Valve cover from the cover gasket. By doing so, this will relieve any
pressure in the Valve.
d. Loosen to remove all cover bolts and lift the cover. After removing the cover of the valve, the
Flapper will be fully exposed and freely removed. The Flapper, the cover gasket, and the body
surfaces of the Check Valve should be fully examined for wear. If replacement parts are needed,
contact the manufacture with Valve type, size, and the appropriate parts.
e. Reassemble, replace the cover gasket.
f. Replace Flapper and be sure that the Flapper rests flat and centered against the body seat
surfaces.