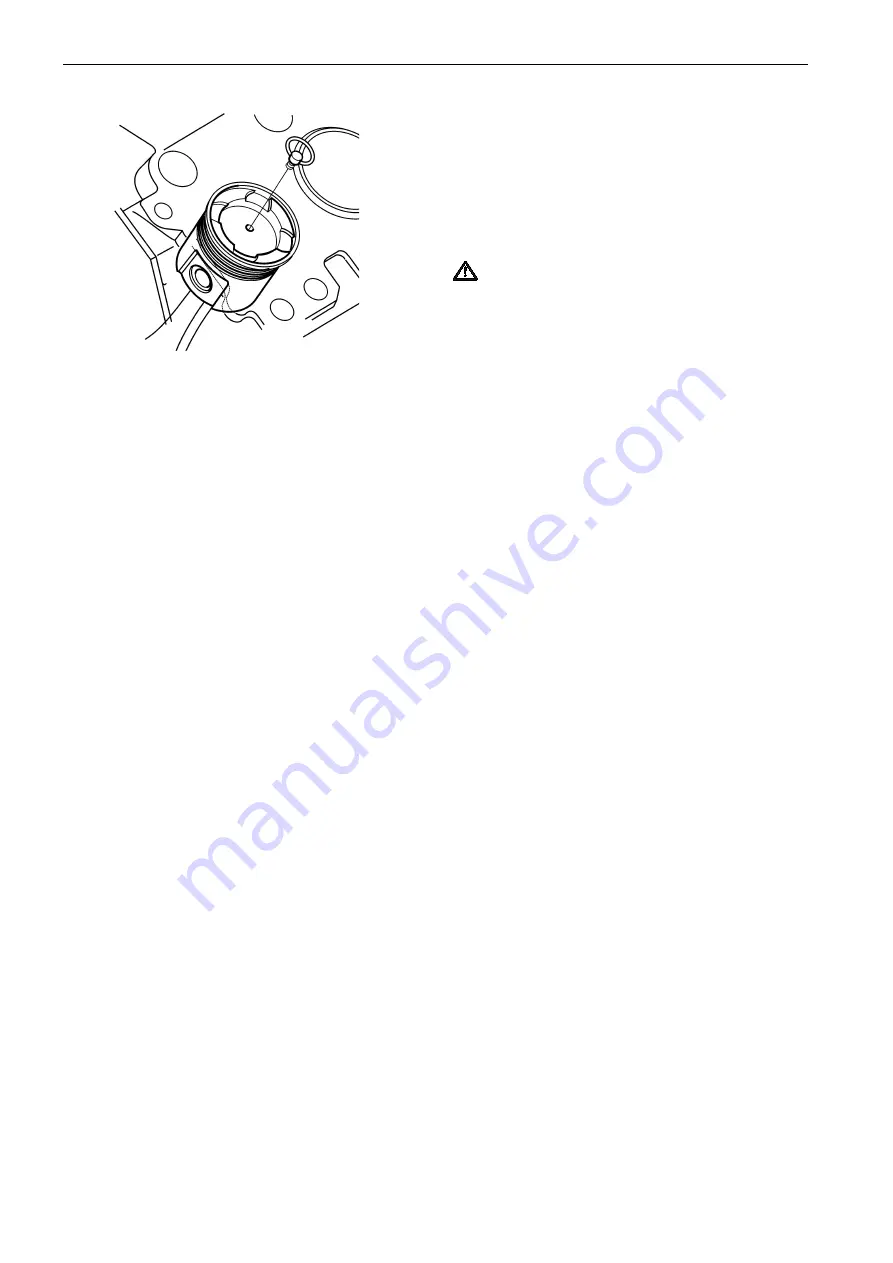
Group 21 Engine Body
94
Using the Piston remover
1.
Turn the crankshaft to bring the piston assembly
to 50° after top dead center for the left bank.
2.
Attach the Piston remover to the top of the piston.
Grip the handle of the remover, then lift the piston
and the connecting rod off the liner.
IMPORTANT!
Do not damage the piston when
you pull it out from the cylinder liner. Do not let
it hit the connecting rod with its skirt. Support
the connecting rod to avoid the cylinder liner
bore from scratching.
Removing the piston ring
Use the Piston ring tool to remove I the piston rings.
Removing piston pins
1.
Use the Ring pliers to remove the snap rings.
2.
Remove the piston pin to separate the piston
from the connecting rod.
3.
If it is difficult to pull out the pin, heat the piston
with a piston heater or in hot water to expand the
pin bore.
Plus d'informations sur : www.dbmoteurs.fr
Summary of Contents for D65A MS
Page 1: ...Workshop Manual H 2 0 D65A MS D65A MT Plus d informations sur www dbmoteurs fr ...
Page 2: ...Plus d informations sur www dbmoteurs fr ...
Page 212: ...Notes Plus d informations sur www dbmoteurs fr ...
Page 213: ...Notes Plus d informations sur www dbmoteurs fr ...
Page 214: ...Notes Plus d informations sur www dbmoteurs fr ...
Page 215: ...Plus d informations sur www dbmoteurs fr ...
Page 216: ...7742853 0 English 09 2003 Plus d informations sur www dbmoteurs fr ...