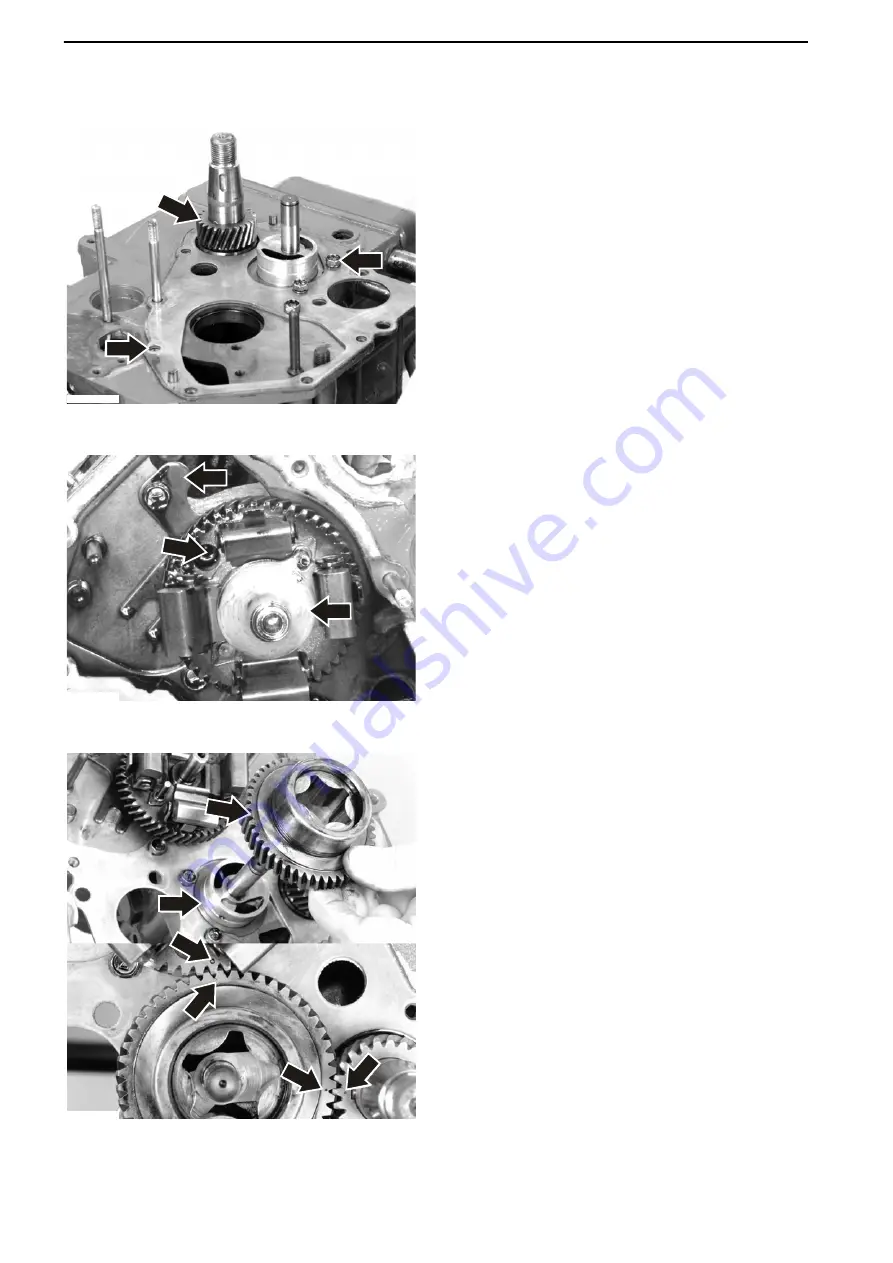
Timing Gear, Installation
1
Place the gear wheel (
1
) and its key on the crank-
shaft. Tap the gear wheel on.
Position the timing gear plate (
2
) and a new gas-
ket.
Fasten the timing gear plate inner bolts (
3
).
2
Carefully insert the camshaft.
IMPORTANT!
If the camshaft is forced in, there is a risk that one
of the cam lobes will damage an internal bearing.
Place the lock plate (
1
) in position. Rotate the cam-
shaft until the screw hole for the socket cap screw
(
2
) becomes visible in the hole in the camshaft
drive gear. Fasten the lock plate. Place the cam-
shaft regulator sleeve (
3
) in position.
3
Fit the thrust washing (
1
) in place. Put on the oil
pump gear wheel (
2
). Make sure that the mark-
ings (
3
) on the gear wheel line up with the mark-
ings (
4
) on the other gear wheels. Check the gear
.
1
3
2
P0008044
1
3
2
P0008045
1
3
3
4
4
2
P0008046
21-5 Timing Gears and Shaft
80
47701798 05-2013 © AB VOLVO PENTA
Summary of Contents for D1-13
Page 1: ...Group 21 26 Workshop Manual 2 0 A D1 13 D1 20 D1 30 D2 40 ...
Page 2: ......
Page 133: ...References to Service Bulletins Group No Date Refers to 131 ...
Page 134: ......
Page 136: ...47701798 English 05 2013 ...