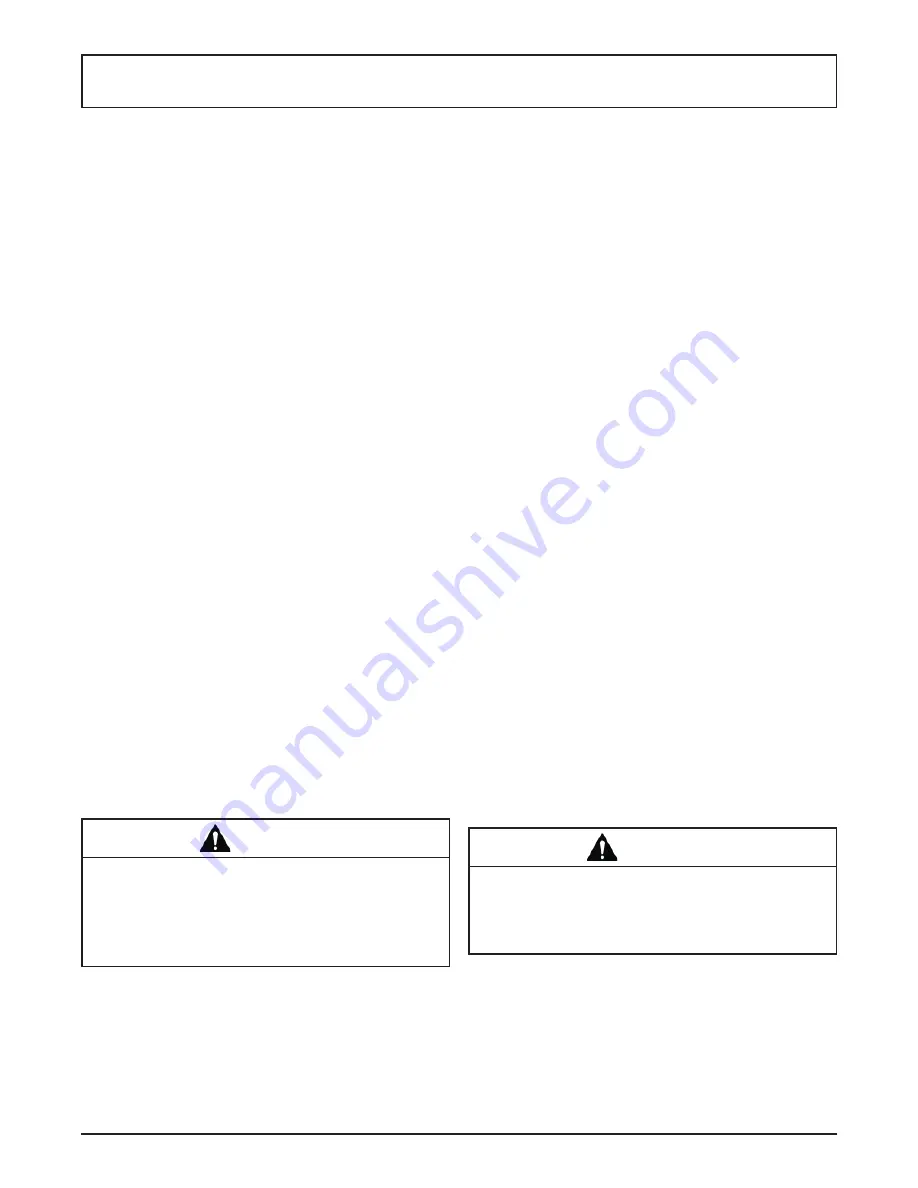
Owner’s Manual #513707
3
F231-2X Model Machines
SECTION 2
INSTALLATION INSTRUCTIONS
2.1 SAFETY PRECAUTIONS
Do not attempt to operate the machine until the safety
precautions and operating instructions in this manual are
read completely and are thoroughly understood.
Take notice of all warning labels on the machine. The la-
bels have been put there to help maintain a safe working
environment. The labels have been designed to withstand
washing and cleaning. All labels must remain legible for
the life of the machine. Labels should be checked periodi-
cally to be sure they can be recognized as warning labels.
If danger, warning or caution labels are needed, indicate
the part number, type of label, location of label, and quantity
required along with your address and mail to:
STOELTING
ATTENTION: Customer Service
502 Hwy. 67
Kiel, Wisconsin 53042
2.2 SHIPMENT AND TRANSIT
The machine has been assembled, operated and inspected
at the factory. Upon arrival at the
fi
nal destination, the
entire machine must be checked for any damage which
may have occurred during transit.
With the method of packaging used, the machine should
arrive in excellent condition. THE CARRIER IS RESPON-
SIBLE FOR ALL DAMAGE IN TRANSIT, WHETHER
VISIBLE OR CONCEALED. Do not pay the freight bill
until the machine has been checked for damage. Have
the carrier note any visible damage on the freight bill. If
concealed damage and/or shortage is found later, advise
the carrier within 10 days and request inspection. The
customer must place claim for damages and/or shortages
in shipment with the carrier. Stoelting, Inc. cannot make
any claims against the carrier.
2.3 MACHINE INSTALLATION
WARNING
Installation must be completed by a quali
fi
ed
electrician/refrigeration specialist.
Incorrect installation may cause personal injury,
severe damage to the machine and will void fac-
tory warranty.
Installation of the machine involves moving the machine
close to its permanent location, removing all crating, set-
ting in place, assembling parts, and cleaning.
PRIOR TO INSTALLATION
A.
Locate a copy of the service contact
fi
le (info.txt).
B. Modify
the
info.txt
fi
le with information from the
service company using the instructions in the
fi
le.
C.
Put the service contact
fi
le onto the root level of
a USB
fl
ash drive (do not put the
fi
les into any
folder).
INSTALLATION
A.
Uncrate the machine.
B.
Install the four casters. Turn the threaded end
into the machine until no threads are showing. To
level, turn out casters no more than 1/4” maximum,
then tighten all jam nuts.
C.
The machine must be placed in a solid level
position. If adjustment is necessary, level the
machine by turning the bottom part of each leg
in or out.
NOTE
Accurate leveling is necessary for correct drainage
of freezing cylinder and to insure correct overrun.
D.
Provide proper cooling requirements:
1. Air cooled machines require a minimum of 3”
(7,5cm) of space on both sides for proper air
circulation.
2. Water cooled machines require 1/2” NPT
supply and drain
fi
ttings.
E.
Connect the power cord to the proper power
supply. Refer to the nameplate on the machine for
the proper supply. The unit must be connected to a
properly grounded receptacle. The electrical cord
furnished as part of the machine has a three prong
grounding type plug. The use of an extension cord
is not recommended. Do not use an adapter to
circumvent the grounding requirement.
WARNING
Do not alter or deform the electrical plug in any
way. Altering the plug to
fi
t into an outlet of differ-
ent con
fi
guration may cause
fi
re, risk of electrical
shock, product damage, and will void the warranty.
Summary of Contents for Stoelting F231-2X
Page 1: ...Model F231 2X OPERATORS MANUAL Manual No 513707 Rev 2 A VOLLRATH DIVISION...
Page 2: ......
Page 6: ......
Page 12: ...Owner s Manual 513707 6 F231 2X Model Machines...
Page 24: ...Owner s Manual 513707 18 F231 2X Model Machines...
Page 28: ...Owner s Manual 513707 22 F231 2X Model Machines...