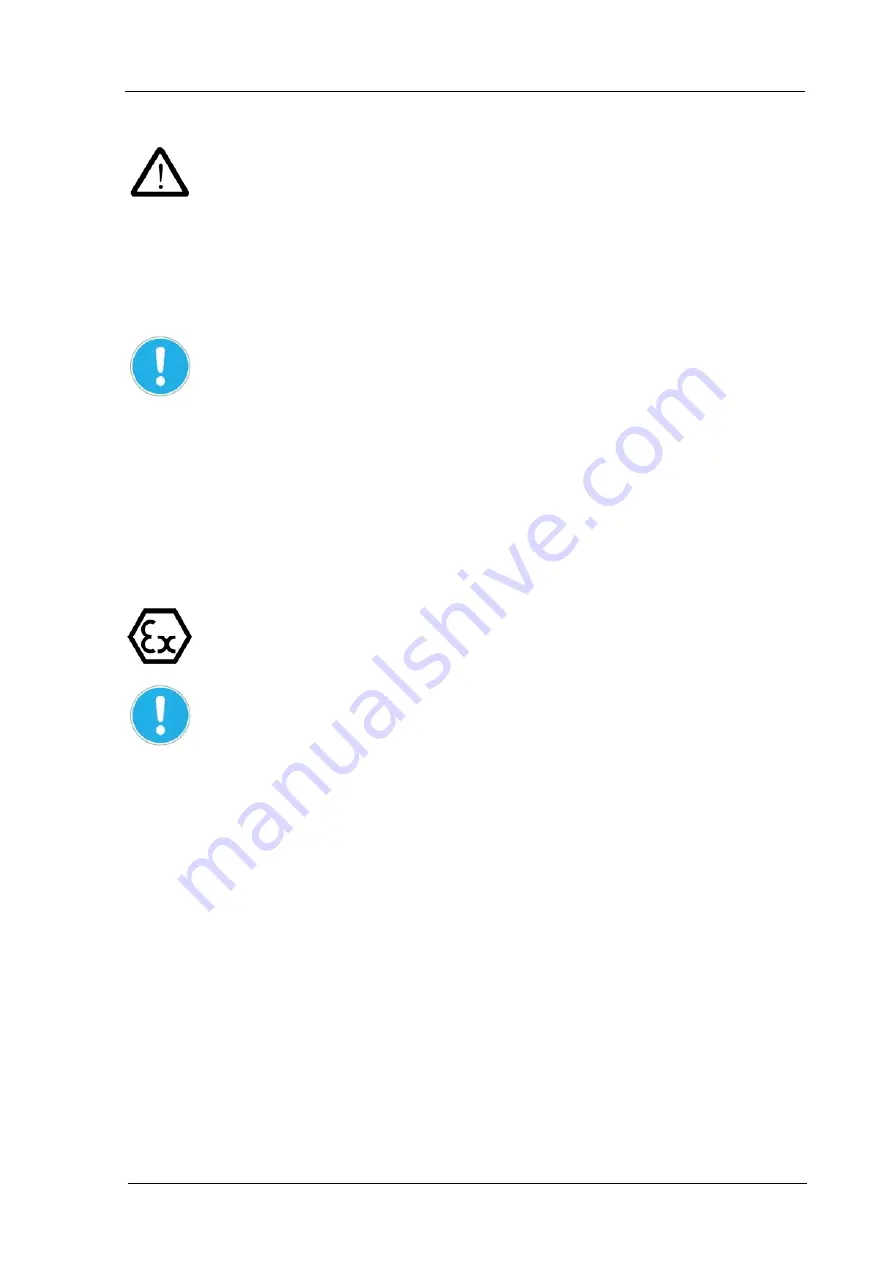
Instruction Manual
Voith Turbo
Way Valve WSR-D16212
2003 / 07 aie
Voith Turbo GmbH & Co. KG
Page: 13 / 24
918 3626 018870 en
D – 74564 Crailsheim
Version: 3.0
5.2 Hydraulic
connection
Wear protective glasses when connecting the way valve hydraulically.
Pay attention to the correct pressure stage when selecting pipes, flexible tubes, unions
and flanges.
Immediately replace any damaged pipes and flexible tubes.
When assembling the pipes, ensure that they are not fastened to any moving equipment,
but rather to fixed structures free from vibration.
Alterations in length caused by temperature variations must not apply constraining forces
to the way valve.
Fixing and hydraulic connection to a connecting flange is made via the hydraulic part.
Kant seal rings are used for sealing. The customer's connecting flange must
correspond to Ra
≤
1.6 µm and Rmax
≤
6.3 µm.
Residual oil (up to 0.3 l) may leak when removing the screw plugs. Collect the oil in a
suitable container and dispose it off properly.
Do not use fibrous or hardening sealing compounds, such as hemp or mastic to seal
the connections and pipe unions.
Prior to installation, clean pipes from dirt, cinder, sand, chips, etc.
Pickle welded pipes. Clean and flush carefully the pipes and the whole hydraulic system
before installing the way valve.
5.3 Electrical
connection
Only a certified electrician with experience and knowledge in the field of explosion
protection is allowed to connect the servomotor electrically in accordance with the
electro-technical rules and legal provisions of the country of manufacture.
Signal and supply lines provided by the customer to the way valve need to be
screened and laid separately from each other.
When connecting the customer's lines, please avoid parallel running of way valve lines
with the lines of the current converter assemblies.
Poor connecting points do not guarantee a reliable operation of the way valve.
Connect the way valve according to the connection diagram (see Chapter 10, annex).
Summary of Contents for WSR-D16212
Page 25: ......